AM i byggeindustrien
Additive Manufacturing (AM), which emerged in the 1980s as a polymer prototyping technique, revolutionised traditional manufacturing by introducing a layer-by-layer approach that adds material rather than subtracting it. Unlike conventional manufacturing, AM is tool-independent, making the process much faster, especially in the early stages of production, and offers unparalleled design flexibility, automation, digitisation benefits and high precision. Large-scale 3D printing has been shown to efficiently produce new geometries, opening new horizons for construction applications.
Danish AM Hub aims to support Danish manufacturers in the use of AM for bio-based materials, whose production is currently limited by scalability and economic challenges. By using AM, they could potentially improve product functionality and scalability, as well as create economic synergies through networking and collaboration with the Danish AM ecosystem.

Additive Manufacturing in Construction
Danish AM Hub has conducted an analysis of the construction industry’s biggest challenges, identifying key focus areas based on reduction of emissions, waste and resource consumption, the integration of sustainable materials and the level of flexibility of the system.
The analysis includes expert interviews, workshop results and 20 case studies, representative of different materials, system flexibility and building typologies.
Read the summary here or download the full report below.
Challenges and significant potential for sustainable improvements
Interest in AM for construction, but limited knowledge of technology, potential and use.
AM is mainly known as a structural onsite concrete solution or for experimental designs and small scale.
The documentation and sustainability aspects of AM need to be further explored to be able to scale AM in construction.
Key conclusions
Innovation at component level: AM offers scalable opportunities to develop modular, low-emission components that are resource efficient and readily compliant with building regulations.
Synergy with bio-based materials: The use of biogenic materials alongside AM technology reduces GHG emissions while enabling innovative and functional designs.
Circularity and adaptability: Emphasising design for disassembly and modularity is critical to minimising waste and extending the life cycle of materials and components.
Case studies
The analysis highlights two primary areas where Additive Manufacturing (AM) can significantly impact the construction industry: Sustainability and Flexibility. By addressing these areas, AM has the potential to align construction practices with global climate goals while enabling innovative, adaptive designs.
The illustration positions the case studies in four quadrants, based on the emissions associated with their materials and the adaptability of their designs.
Click the links below to read the cases.

I AM MSHRM
Closing waste loops through additive manufacturing
I AM MSHRM, a project developed by Danish AM Hub and Bjarke Ingels Group (BIG), is an example of how the combination of 3D printing and bio-based materials can promote environmental sustainability.


The modular pavilion combines 3D printed recycled plastic and baked mycelium. It is designed to be dismantled, reassembled or recycled after use, responding to urban and construction waste challenges. The technology allows the creation of complex curved structures that would be inefficient to produce using traditional methods.
According to the Danish AM Hub’s CO2e calculator, the pavilion emits less than 20% of the CO2 of a comparable structure built with conventional materials. The I AM MSHRM system has the potential to be scaled up for different applications, such as temporary housing or community spaces, using locally sourced waste materials.
Interesseret i at høre mere?
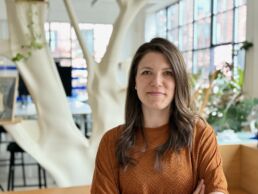
Kontakt
Eleonora Orsetti
Programme Director
+45 29 90 37 82
elo@am-hub.dk