Inspired by nature: Airbus is testing the limits for aircraft components.
Using a new approach to design and additive manufacturing, Airbus is challenging traditional aircraft design. This has resulted in a bionic component, inspired by nature, that is both stronger and lighter than current designs.
By Erik Holm
Strength, less weight and lower production costs. These are some of the goals of a project between Airbus and the Autodesk studio The Living in New York. The project is called The Bionic Partition Project. Inspired by nature, the project has developed a radical, other-worldly structure for aircraft cabins that may have great potential when it comes to the holy grail of the airplane industry. One of the key players is innovation manager Bastian Schaefer from Airbus in Hamburg, Germany.
Bastian, how did The Bionic Partition Project come about?
“The project was started by two departments at Airbus; Cabin Architects and Cabin Innovation in 2013. Airbus Cabin Innovation had previously worked on a project called Airbus Cabin Concept, which was an airplane concept that used a bionic structure. We wanted to move from the concept stage to producing prototypes using generative design (a technology that mimics evolutionary design) based on biologic growth patterns and additive manufacturing.”
What is the objective of the project?
The objective was to design a dividing wall that could hold a fold-down jumpseat for flight attendants as well as a cut-out section. This will help get wide objects through the airplane cabin. Both the jumpseat and the cut-out result in structural weakness in the wall, which is only one inch thick. This makes the dividing wall one of the most complex structures in the cabin to optimise. In addition to a 25% weight reduction, we also wanted to reduce the costs of producing the component.“
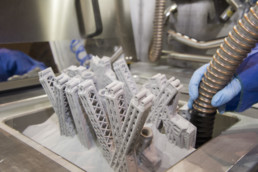
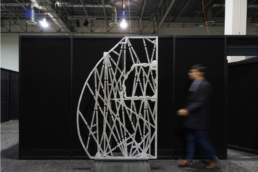
How did you develop the bionic structure and where did you find your inspiration?
“We worked together with Autodesk and The Living on this project. The Living, a firm of architects based in New York, introduced us to generative design. We created an algorithm using a computer model that drew on inspiration from a single-cell fungus that creates different structures in nature. The model can create tens of thousands of design suggestions for the “macrostructures” in the frame of the dividing wall, in a very short space of time. During another procedure, we used a parameterised lattice structure to create so-called “microstructures” in the material of the frame. This was inspired by animal bones.”
What is the role of additive manufacturing?
“A requirement right from the start was that all components must be 3D printed. Additive manufacturing was still in its infancy, but was at the top of what Gartner called ‘inflated expectations’. But we wanted to create structures that could only be produced using AM. Furthermore, we wanted to use a material developed by Airbus called ‘scalmalloy’ and demonstrate its abilities.”
What materials did you use?
“Scalmalloy is an aluminium-magnesium-scandium alloy with a high tensile strength of approximately 500 MPa. It’s a good material to use when dealing with the dynamic forces in an airplane. The material gets its strength from the rapid cooling in the 3D printer, which creates a chemical reaction between the scandium and the other ingredients.”
What is the benefit of these bionic components compared with traditional structures in an aircraft?
“In general, bionic structures can help minimize the weight of components. Additive manufacturing is the perfect technology to use when producing these kinds of components. For example, AM makes it possible to create hollow structures. Just like in a human bone, material is only used in areas where it is absolutely necessary to manage stresses and loads. This makes components much lighter.”
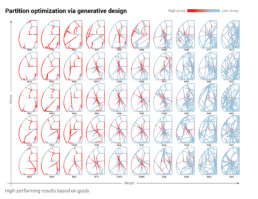
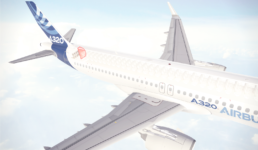
When will we see bionic structures in an aircraft?
“That depends on production costs. Bionic structures normally need additive manufacturing, which requires 13 process steps in order to match the quality required for aviation. As we increase automation and thereby reduce costs, we might begin to see more components. This may start to happen over the next five years. Until then, we’ll use generative design in more traditional production technologies to help bring them to the next level as well.”
What potential does this technology bring to your respective companies?
“For Airbus, the effect of these different products and components is of great interest. As is the effect they could have on the entire industry. Someday, our work may result in new software or plug-ins for existing software that could help Airbus and our suppliers design and build better airplanes.”
What are the most important learning points so far?
“We’ve learned a lot during this project. At the beginning, we thought that manufacturers of metal printers would quickly be able to produce larger and faster machines to help lower production costs. This was not the case. The machines did get bigger, but we had to deal with other problems such as thermal loads in the printer, particularly when printing larger components. We also knew that we needed to produce at a certain speed in order to minimise production costs. We needed a speed of 200cm3/hour for microstructures, and this would require multi-laser machines. However, in the beginning, we only had a speed of 11cm3/hour using single-laser machines. And finally, we underestimated the finishing necessary for the printed components. Today, roughly speaking, a third of the price of a 3D printed component is for the printing itself, while another two-thirds are for finishing.
What is the next step?
“At the moment, we’re looking at combining generative design with other production technologies, such as casting. New optimisation strategies help advance traditional production methods. Furthermore, together with Autodesk and The Living, we’re also looking into using generative design in other areas of the design and production process.”
The Bionic Partition Project:
Airbus, The Living and Autodesk are working together on the project. The objective was to build a dividing wall for the cabin of the Airbus A320 that:
- was significantly lighter than the current dividing wall, thus reducing the weight of the whole aircraft
- was strong enough to hold two jumpseats for flight attendants during take-off and landing
- had a cut-out section allow wide objects to be taken in and out of the cabin
- was no more than one inch thick
- was attached to the fuselage in no more than four places.
Generative design is a technology that mimics nature’s evolutionary approach to design.
It starts with a number of defined design objectives. A computer then explores every possible permutation of a given solution. Cloud computing means that software can very quickly go through thousands of different design choices, configurations and learning from each iteration. This process means that designers can create completely new opportunities to achieve the most efficient designs. The results, such as the dividing wall for the Airbus, may look almost random, but they have been optimised for strength and weight.
Bastian Schaefer has an engineering degree from the University of Applied Sciences in Hamburg. He works as an innovation manager at the Emerging Technologies & Concepts department at Airbus. Shaefer is part of a team of engineers. The head of the team, Peter Sander, calls the team “crazy guys” because of their constant efforts to push the boundaries of industrial processing into the future.
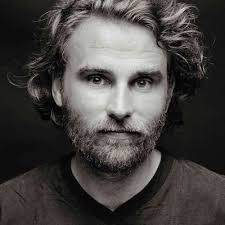