SMV: Vi vil ikke sige nej til en million igen
SMV: Vi vil ikke sige nej til en million igen
Erfarne virksomheder skal hjælpe andre virksomheder i gang med 3D-print i Dansk AM Hubs AM Inspire, som allerede har matchet Widex med Scandinavian Packaging, som vil bruge teknologien til at gribe flere opgaver.
- For cirka et år siden fik vi en henvendelse fra en kunde i Norge, som havde en opgave til en lille million kroner. Men vi endte med at sige nej til opgaven, fordi vi kun kunne få den produceret i Kina og leveringstiden var for lang i forhold til kundens behov. Hvis vi havde været lidt længere fremme med 3D-print, kunne vi sandsynligvis have løst opgaven i Danmark, fortæller Hanne Zinck Jørgensen, som er COO og partner i virksomheden Scandinavian Packaging.
Virksomheden lever i dag af at producere store partier emballage – primært flasker og kapsler i plast – og det har de succes med. Til gengæld kniber det med at gribe de mindre ordrestørrelser, hvor eksempelvis en hotelkæde ønsker at få designet og produceret en mindre serie shampoo-flasker. Den type opgaver er faktisk røget helt ud af Danmark.
- Når jeg f.eks. ser en lækker, økologisk creme i en beholder fra Kina, synes jeg, det er en skam. For den kunne vi formentlig producere mere bæredygtigt ved hjælp af 3D-print herhjemme, siger Hanne Zinck Jørgensen, som er uddannet plastingeniør og betegner sig selv som lidt af en ’emballagenørd’.
Brug for input til at komme videre
Scandinavian Packaging er allerede så småt i gang med 3D-print – og de har masser af mod på at gå videre. Indtil videre har de bare manglet den nødvendige erfaring/viden til at tage det helt rigtige næste skridt.
- Vi har allerede to mindre 3D-printere, som vi bruger til at lave prototyper, men vi har bl.a. brug for mere viden om, hvilke materialer til 3D-print, der er på markedet. Vi vil også rigtig gerne have input i forhold til, hvilken 3D-printer vi skal investere i næste gang, siger Hanne Zinck Jørgensen.
Den viden er de nu på vej til at få gennem projektet AM Inspire, som er udviklet af Dansk AM Hub og Dansk Industri. Projektets mål er at matche virksomheder, som har stor erfaring med AM-teknologi – som f.eks. 3D-print – med virksomheder, der mangler input på området.
Danmark er desværre bagud på AM-området i forhold til andre lande.Hanne Zinck Jørgensen, COO i Scandinavian Packaging
Deler viden for at komme i front
Scandinavian Packaging er blevet matchet med virksomheden Widex A/S, som producerer høreapparater og allerede har stor erfaring med 3D-print.
- Vi skal mødes med Widex første gang her i juni, og det ser jeg meget frem til. Og når vi er kommet lidt videre, vil vores virksomhed også med stor glæde give vores erfaringer videre til andre danske virksomheder, for Danmark er desværre bagud på dette AM-området i forhold til andre lande, påpeger Hanne Zinck Jørgensen.
AM Inspire er et samarbejde mellem Dansk AM hub og Dansk Industri, finansieret af Dansk AM hub, der er initieret og udviklet af Industriens Fond. Programmet er åben for virksomheder, der vil have mere viden om hvordan de kan få gavn af AM-teknologi.
Historien er bragt i DI Business: https://www.danskindustri.dk/di-business/arkiv/nyheder/2018/5/smv-vi-vil-ikke-sige-nej-til-en-million-igen/
Læs mere om AM Inspire og tilmeld din virksomhed: https://am-hub.dk/am-inspire/
AM Inspire: Kom godt i gang med 3D print
AM Inspire: Kom godt i gang med 3D print
I 2017 sparede Danfoss mere end 400.000 Euro på at 3D-printe. De har givet deres erfaringer videre til Johs. Pedersen, der nu vil se på, hvor 3D-print kan give værdi i virksomheden, der fremstiller reservedele til blandt andre Porsche og VW.
Danfoss Drives har inspireret den mindre virksomhed Johs. Pedersen til at komme i gang med 3D-print. Det er sket gennem Dansk AM Hubs virksomhedsprogram: AM Inspire, der er et inspirationsforløb til danske SMV’er, der er nysgerrige på, hvordan 3D print med fordel kan bruges i produktionen.
AM Inspire er i al sin enkelthed et forløb med to sparringsmøder mellem en produktionsvirksomhed og en inspirator, der kommer fra en virksomhed, der er kommet i gang med at bruge 3D print.
Johs. Pedersen, der fremstiller reservedele til klassiske biler som Porsche og VW, har gennemgået forløbet sammen med Danfoss Drives, der er så godt i gang med 3D print, at de i 2017 sparede mindst 400.000 Euro på selv at 3D-printe. Johs. Pedersen har nu en stor forventning om, at 3D-print skal reducere deres ”time to market” væsentligt.
Se med i videoen her og hør om både Danfoss og Johs.Pedersens erfaringer og forventninger til 3D print.
Freeform Injection Molding i små-skalaproduktion vinder frem
”Vores kunder oplever at Freeform Injection Molding giver en fantastisk mulighed for teste prototypen af i det rigtige materiale til en rigtig fornuftig pris.”
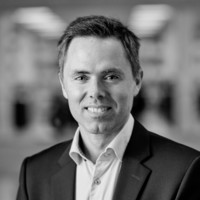
Krebs & Co. er en virksomhed i Skævinge, Nordsjælland, som har været i sprøjtestøbebranchen siden 1956. I dag er virksomheden to-benet. Dels sprøjteblæser og sprøjtestøber de, som de har gjort i mange år. For nylig har de investeret i 3D-print og Freeform Injection Molding.
Freeform Injection Molding er en hybrid af 3D-print og traditionel sprøjtestøbning. Fordelen er, at vi kan lave negativet eller skallen med 3D-printeren, som vi bagefter kan støbe ind i med allerede godkendte materialer. På den måde kan vi tage fat i materialer, der er godkendt til medicinsk brug. Kombinationen giver således en unik mulighed for at teste prototyper af i de rigtige materialer fra start, samtidig med at prisen holdes nede.
– Peter Bay, CEO i J. Krebs & Co.
I Danmark er mange teknologivirksomheder forholdsvis små, og derfor har de som oftest ikke de nødvendige ressourcer til at udvikle og producere nye teknologier. Det betyder, at det ofte er alfa og omega at samarbejde med en lang række aktører som videninstitutioner og andre private virksomheder.
En af de virksomheder, som J. Krebs & Co samarbejder tæt med, er AddiFab. Jylling-virksomheden er i disse måneder ved at tage springet fra innovationsvirksomhed til kommerciel vækstvirksomhed med FreeFrom Injection Molding som teknologisk flagskib.
For at teknologien Freeform Injection Molding rigtig skal vinde frem, kræver det løbende forbedringer af præcision og tolerance. Dertil skal produktionshastigheden øges – det er ikke forventeligt, at det skal være lige så hurtigt som traditionelt 3D-print, men det skal være hurtigere at arbejde med Freeform Injection Molding end at producere i metal. Målet er at kunne levere små serier eller prototyper med kort leveringstid, hvor træfsikkerhed kan garanteres.
Hos J. Krebs & Co er vi stadig i prototype-stadiet. Vi har en masse succeshistorier, men vi har selvfølgelig også en række historier, hvor det ikke gik, som vi håbede. Men sådan er det, når vi arbejder med nye materialer, der støbes ved over 300 grader og under meget højt tryk. Nu er der behov for en masse validering. Det kræver meget at føde en ny teknologi, og vi har det desværre med at sammenligne den nye teknologi med en gammel teknologi som sprøjtestøbning. Det betyder, at den nye teknologi risikerer at blive fejet af banen for hurtigt– og det er synd, siger Peter fra J. Krebs & Co.
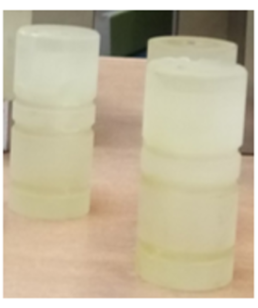
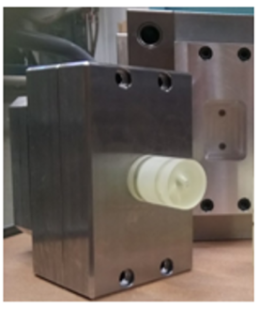
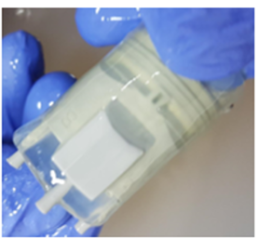
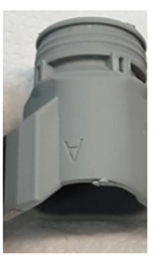
I AM HYBRID har Krebs og Co. anvendt FIM til en række produktudviklingsforløb sammen med deres kunder. Et eksempel er et el-stik til Danfoss A/S. Freeform Injection Molding har her givet stor mening, da det er tale om småskala produktion efter kundetilpasset design. De har også været med i en del af de efterfølgende cases til sammen med Teknologisk Institut at hjælpe virksomheder med FIM.
Vi har udelukkende 7 materialer, mange af dem fiberforstærkede, som vi bruger igen og igen. De er gennemtestede, og vi er rigtig gode til at lave produkter i dem. Vi har gennemsøgt markedet bl.a. i Tyskland og der findes i dag ikke nogen anden metode end FIM til at få produceret prototyper el. lave småskalaproduktion af nye designs i disse materialer.
– Saeed D. Farahani, Leder af Danfoss’ AM-afdeling
Silkeborg Stigefabrik - prototyping: Fra fire uger til fire dage
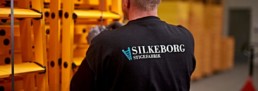
Silkeborg Stigefabrik – prototyping: Fra fire uger til fire dage
Alimak Group Denmark A/S er, via sit brand Silkeborg Stigefabrik, Danmarks største udbyder af stiger i træ, aluminium og glasfiber, foruden mobile lifte, stilladser, og specialløsninger.
Foruden professionelle stiger til bl.a. håndværkere, vinduespudsere og skorstensfejere, har Silkeborg Stigefabrik et bredt udvalg af produkter til den private. Brandet Silkeborg Stigefabrik har Danmarks største udvalg af stiger, stilladser og trapper – og samarbejder med nordens førende producenter, som sender varerne direkte fra fabrikken til din hoveddør. Markederne er – ud over privatsegmentet – generelt industri, entreprenører, bygningshåndværkere og vind industrien.
Baggrund for projekt
Alimak Group Denmark A/S har gennem de seneste år fået produceret plastikkomponenter hos eksterne leverandører i Fjernøsten, bl.a. fra Indien. Alimak Group Denmark A/S udvikler ikke selv deres prototyper in-house, da de ikke har maskine set-up, som kan løse disse opgaver. Alimak Group Denmark A/S har derfor søgt en proces – udvikling/fremstilling af prototype/proof of concept – og som kan skabe en kortere lead time frem tooling og den endelige fysiske udgave.
Hidtil af prototype-opgaven og ansvaret ligget hos Alimak´s indiske underleverandør, og man har derfor været afhængig af lang leveringstid af en given prototype – på op til 4 uger. Ofte har det yderligere vist sig, at den pågældende prototype ikke har været helt som forventet. Derfor er der tit påløbet yderlige 4 uger i processen før den endelige prototype er nåede frem til endelig godkendelse i Silkeborg.
Processen
I samarbejde med AM-HUB´s TRY OUT indledte Center For Industri og Alimak et fælles udviklingsprojekt med fokus på netop PROTOTYPING. Virksomheden fik stillet en Makerbot Replicator 3D printer til rådighed, som del af deres technology assesment proces.
Hos Alimak er der således først udført en technology-assesment. Her er 4 emner (både inden for hovedområderne udvikling/prototyping, produktion/AM og tooling) blevet udvalgt til at indgå i denne proces. Filer, tegninger, kostberegninger m.m. er indgået i udarbejdelse af technology assessment analysen. Her har Alimak in-house printet emner på en Makerbot Replicator 3D-printer, og lavet benchmark op mod ekstern udførelse og konventionel fremstillingsteknologi.
Alimak har i processen kunnet arbejde med filer, som de har modtaget fra kunder – til 3D-print og mhp at udføre proof of concept tests.
Med 50% infill er printertiden 3-4 timer for fremstilling af komponenten i nedenstående fig.
Forløbet
Alimak Group Denmark A/S modtager en 3D tegnet fil fra en kunde. Ud fra denne fil laver Alimak nu et 3D-print af emnet, som fremsendes til kunden. Protypen evalueres af kunden, som kunden godkender eller anviser ændringer og rettelser til, som de ændrer i tegningsfilen. Alimak Group Denmark A/S laver herefter endnu et 3D print, til endelig godkendelse hos kunden.
Udbytte
Dette forløb kan gennemføres over 2-4 dage og dermed reduceres lead time i forhold til den oprindelige proces med op til 4 uger. Desuden kan Alimak undervejs i processen ændre på konstruktionsparametre som design, infill og materialevalg m.m., hvis det skulle være nødvendigt for at øge styrke, varmetolerance m.m. af den 3D printede komponent.
Foruden det tidsmæssige udbytte er der desuden en omkostningsreduktion på anslået 50%.
”Vi kunne gennemføre 3D print forløbet og levere en 3D printet komponent til kunden på 3-4 dage – hvor det normalt kan tage op til 4 uger”
Henrik Gadgaard, Production/Purchasing Manager Silkeborg Stigefabrik
Foruden den direkte ovennævnte værdiskabelse hos Alimak, skabes der også større værdi for Alimak´s kunder og en strategisk værdi Alimak via en stærkere relation overfor kunden.
Efterfølgende TRY-OUT forløbet har virksomhedens ledelse truffet en strategisk beslutning om at anskaffe sin egen 3D-printer til virksomheden i Silkeborg.
HYTOR løser kundernes problemer gennem 3D print
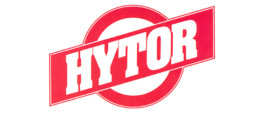
HYTOR løser kundernes problemer gennem 3D print
HYTOR består i dag af både HYTOR Fluid Solutions og HYTOR Tools Solutions. Som innovativ serviceminded gruppe designes og konstrueres der innovative systemløsninger med afsæt i hydraulik, ligesom man sælger proces og instrumenteringskomponenter i selskabet HYTOR Fluid Solutions, mens man i HYTOR Tools Solutions har fokus på levering, service og kalibrering af specialiseret værktøjsløsninger.
Design, konstruktion, samling og test udføres på eget værksted. Ligesom man er certificeret service og kalibreringsværksted for hydraulisk og elektrisk værktøj.
Sortimentet omfatter markedets bedste kvalitetsprodukter, der opfylder alle sikkerheds- og certificeringskrav. HYTOR er således i dag certificeret efter ISO 9001, ISO 14001 og OHSAS 18001.
Gennem HYTOR Tools Solutions serviceres primært vindmølleindustrien, men også forsyningskæden, den generelle industri og entreprenørbranche, med specialiseret værktøj inden for primært momentbespændingsteknologi, dækkende over blandt andet momentspændeværktøj, løfteværktøj, strækværktøj, møtrikknusere, momentnøgler (65.000Nm) samt flangeværktøj.
Med et ”rullende værksted” er HYTOR Tools Solutions med uddannede serviceteknikkere i stand til at servicere kunden on-site med reparation, service og kalibrering af specialiseret værktøj, og kan samtidig assistere kunderne med specielt vanskelige opgaver primært indenfor installation og service af vindmøller.
Med dette afsæt agerer HYTOR Tools Solutions problemløser for kunden og er parat til at modificere eksisterende løsninger både fra hovedkontoret i Esbjerg og on-site hos kunden.
I tæt samarbejde med Center for Industri har HYTOR Tools Solutions igangsat to forskellige projekter indenfor momentbespænding ved installation og servicering af vindmøller:
Projekt: COUNTER KEY
Et ændret behov banede vej for en nyudvikling af modholdsnøgler på bolte ved samling af naceller til vindmøller. Idegrundlaget var et betjeningsvenligt frigørelsesmodhold, som ikke i dag er tilgængeligt på markedet, og derfor skulle skabes fra bunden.
Teknikere hos HYTOR designede en prototype, som skabte grundlag for et 3D print PROTOTYPING projekt. Designet på frigørelsesmodholdet bestod af i alt 23 forskellige komponenter, hvori der også indgik komponenter som fjedre, bolte, afstands- og låseringe samt gummihåndtag.
En MAKERBOT Replicator 3D Printer blev stillet til rådighed hos HYTOR Tools Solutions af AM-HUB i samarbejde med Center for Industri, således at udviklings- og fremstillingsprocessen af prototypen på frigørelsesmodholdet var tæt på udviklerne.
Prototypen på frigørelsesmodholdet, (en proof-of-concept) af dette yderst komplekse specialværktøj, blev fremstillet på få dage, hvilket havde afgørende betydning for det totale tidsforbrug for færdigudvikling af frigørelsesmodholdet. Integration af 3D print i udviklingsfasen muliggjorde nedbringelse af den samlede lead-time fra idegrundlag til reelt værktøj med en faktor fem. Den samlede omkostning for udvikling har beløbet sig til en tiendedel set i forhold til omkostningerne ved en konventionel prototype – 3D prototype print sat op mod en prototype fra en værktøjsproducent.
Projekt: HYDRAULISK SPÆNDEVÆRKTØJ
En modifikation af et pågældende værktøj var nødvendig for at løse en opstået problematik omkring pladsmangel.
Ved hjælp af en scanning af det eksisterende specialværktøj, blev der omgående fremstillet en 3D model af de relevante værktøjer, som så kunne bearbejdes og justeres on-site, for at opnå det korrekte design for momentbespændingsopgaven inden for den plads, der var til rådighed omkring bolten.
Den tilpassede 3D model blev en afgørende faktor, og dermed grundlaget for en egentlig modifikation på det konkrete værktøj. Værktøjsproducenten kunne ud fra 3D modellen modificere specialværktøjet, så det passede til den givne momentspændeopgave.
En uge var hvad det tog, fra problemet opstod hos vindmølleproducenten til HYTOR Tools Solutions nåede frem til en løsning, uden at skulle gøre nytte af producenten. Ikke kun en markant besparelse af tid blev opnået, men omkostningerne for udviklingsforløbet har været en tiendedel af, hvad omkostningerne ville være for et nyt specialværktøj, som modificeres med risiko for ødelæggelse.
I denne case blev der også stillet en MAKERBOT Replicator 3D Printer til rådighed hos HYTOR Tools Solutions af AM-HUB i samarbejde med Center for Industri
Konklusion
Begge cases har vist en markant kortere leveringstid, konkret er der tale om faktor fire, i kraft af muliggørelse af prototyping ved hjælp af 3D print.
Ydermere har omkostningerne forbundet med egen in-house løsning været reduceret væsentlig, i forhold til estimerede omkostning forbundet med leverance fra en ekstern leverandør.
Godkendelsesproceduren, såvel internt som eksternt, har været kort og processen har været effektiv for samarbejdspartner og ikke mindst slutkunden.
To cases som virksomheden ser mange muligheder i, både i kraft af den hurtige udviklingsfase, men bestemt også omkostningerne forbundet med udviklingsfasen. Samtidig har det været med til at manifestere et allerede eksisterende godt samarbejde alle parter imellem.
Perspektivering
I begge tilfælde blev proto-typing løst ved hjælp af udlånt Makerbot Replicator printer fra AM-HUB / Center for Industri, der gjorde det muligt for virksomheden, i eget værksted, at løse opgaven og samtidig få proof-of-concept hos alle steakholders. En proces der både havde stor gevinst rent tidsmæssigt men også økonomisk.
Center for Industri danner rammerne for udvikling inden for fremstillingsindustrien og tilbyder assistance og viden i samarbejde med Dansk AM-HUB for udbredelse af udviklingsmulighederne inden for 3D print. Kontakt Center for Industri via http://www.centerforindustri.dk/ og hør mere om dine muligheder.
HYTOR udtaler:
Klaus H Rasmussen, Fluid:
“Det har været utrolig nemt at arbejde med 3D printerne, programmerne og materialerne er nemme at gå til og Center for Industri har været en god sparring i forhold til mulighederne og alt det praktiske”
Anne Mette Lorentzen, Marketing Chef:
”Vi ser gode muligheder for anvendelse af 3D print i vores videre samarbejde med vores kunder, det giver os blandt andet mulighed for at lave produktjusteringer i samarbejde med producenten langt hurtigere end tidligere”
Med 3D print får vi langt mindre spild i designprocessen
Norr11: Med 3D print får vi langt mindre spild i designprocessen
Hos møbelvirksomheden NORR11 er det vigtigt både at turde tænke innovativt og bæredygtigt og samtidig være tro mod den danske designarv.
Enkelhed, naturmaterialer og rene linjer. Skandinavisk møbeldesign går i disse år sin sejrsgang over hele verden.
Bag ved succesen står en række dedikerede møbelproducenter, der skal få design og håndværk til at gå op i en højere enhed. En af dem er NORR11, der holder til i Østergade på Strøget i København. Her er både ledelsen og designteamet i fuld gang med at se på mulighederne inden for 3D print. Det fortæller virksomhedens CEO, Magnus B. Magnusson.
”For os er der overhovedet ingen tvivl om, at 3D print fremover vil indgå som en naturlig del af vores tilgang til produktion og bæredygtighed. Særligt når det gælder prototyper, som i dag skal sendes frem og tilbage mellem Asien og Europa, er det helt åbenlyst, at vi kan reducere både spild og transportomkostninger betragteligt ved at fremstille vores egne 3D prototyper i Danmark.”
Ud over at reducere miljøpåvirkningen kan 3D print også bidrage væsentligt til at mindske lead–time for nye produkter, fortæller Magnus B. Magnusson:
”Skal man overleve i møbelbranchen, SKAL man være klar i tide til de store møbelmesser, ligesom der også er ekstremt stramme deadlines, når produkter skal ud til forhandlerne. Her ved vi, at selv små fejl kan medføre voldsomme forsinkelser med store økonomiske konsekvenser til følge. Det er ganske enkelt en sårbarhed i hele vores forretningsmodel, som 3D print kan være med til at eliminere.”
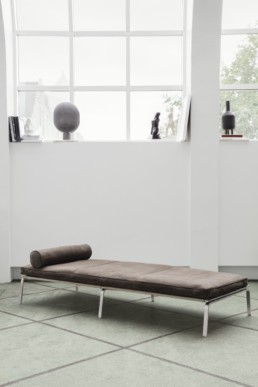
Også når det gælder de store indretningsopgaver, kan 3D teknologien være en game changer, fortæller Magnus B. Magnusson:
”Når en kunde beder os om at pitche et skræddersyet indretningsprojekt, ved vi godt, at de meget hurtigt vil se en prototype. Problemet er, at det let kan ende som et mareridt, når justeringer skal sendes frem og tilbage mellem kontinenter. Her kan 3D print give os en helt anden fleksibilitet, fordi vi kan lave rettelser med det samme. Igen kan vi eliminere både transport og besværlige forretningsgange. For enkelte prototyper regner vi med at kunne nedbringe time-to-market med op til 120 dage, hvilket vil være af utrolig høj kommerciel værdi.”
Ud over fremstillingen af prototyper er NORR11 også for længst gået i gang med at tænke 3D printede komponenter ind i deres slutdesign:
”Lige nu ser vi f.eks. på de møbelsko eller ’dupper’, som bl.a. sidder under vores sofastel af rustfrit stål. Her kan vi ikke bruge standardløsninger, dels fordi stålet er skarpt, og dels fordi vi insisterer på, at tingene skal være lækre hele vejen igennem. Alt det kan vi opnå ved at anvende 3D print. Det er ikke bare en bekvem løsning – det er faktisk også en metode til at fuldende og forbedre vores designs.”
I det hele taget har det ifølge Magnus B. Magnusson været en øjenåbner at opdage 3D teknologien med kyndig vejledning fra Dansk AM Hub, Teknologisk Institut og Deloitte:
”Både når det gælder 3D print og FN’s verdensmål har vi faktisk fået et helt nyt perspektiv på vores forretning. Selv om vi er en relativt ny virksomhed, har vi stadig haft vores faste vaner og vores måder at gøre tingene på. Her synes jeg virkelig, vi har rusket op i os selv og blevet bedre til at stille spørgsmålstegn ved det, vi gør. Fordi vi i dag har en helt anden viden og forståelse for, hvordan 3D teknologien kan bidrage til øget bæredygtighed, er vi også meget skarpere til at få øje på mulighederne.”
Sådan vil Norr11 bidrage til verdensmålene
- Reducere spild ved at fremstille egne 3D prototyper i Danmark.
- Anvende 3D printede komponenter i virksomhedens slutprodukter.
- Tænke bæredygtighed ind i alle processer.
Fakta om NORR11
- NORR11 er en dansk møbel- og designvirksomhed, som blev etableret i 2011.
- Virksomheden arbejder især med yngre og innovative designere om at videreføre og videreudvikle det skandinaviske design.
- Virksomheden har showrooms i både Berlin, London, Reykjavik og København.
- NORR11’s produkter forhandles i mere end 20 lande.
- Som en del af de større indretningsprojekter har NORR11 været med til at indrette Skt. Petri Hotel og Restaurant Kiin Kiin Bao Bao i København samt hoteller, restauranter, kontorer og lounges i bl.a. Reykjavik, Barcelona, Frankfurt, Berlin, Bruxelles, London og Costa Mesa i Californien.
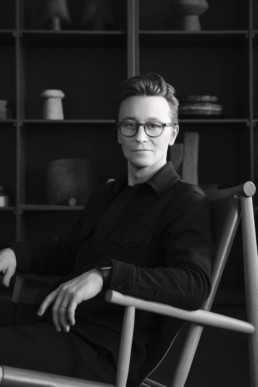
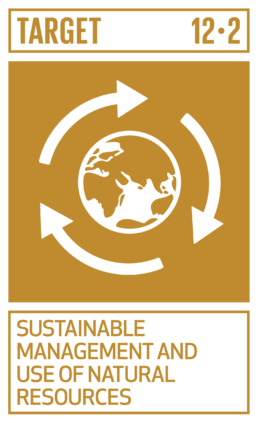
I fremtiden flyver vi ikke reservedele til Japan eller USA, vi sender bare en tegning
dvt: I fremtiden flyver vi ikke reservedele til Japan eller USA, vi sender bare en tegning
dvt i Frederikssund har i over 30 år fremstillet transport- og sorteringsanlæg til industrielle vaskerier. Det har medført et hav af specialudviklede dele, der alle skal lagerføres. Men det kan 3D print lave om på.
dvt er en virksomhed, der tager kunderne alvorligt: Når du køber et transport- eller sorteringsanlæg til et industrielt vaskeri, lover dvt at levere reservedele i hele anlæggets levetid, dvs. i mere end 30 år. Det løfte har skabt både glade og loyale kunder over hele verden, men har også bidraget til at fylde lagrene op. Det fortæller Sten Græse, der har været ansat i firmaet i hele 32 år, først som serviceteknikere, siden som produktionschef og nu som adm. direktør:
”Løftet om at levere reservedele over en 30-årig periode har uden tvivl været et unique selling point over for vores kunder. Udfordringen er dog, at vi i dag må lagerføre titusindvis af komponenter, hvilket har nødvendiggjort en enorm lokalekapacitet på fabrikken. Her er det helt åbenlyst, at 3D teknologien kan spille en afgørende rolle. I det øjeblik vi kan lave print-on-demand, kan vi nedbringe vores lager med ca. 20 pct. og dermed også reducere vores miljøpåvirkning væsentligt.”
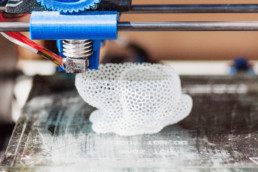
Også når det gælder bæredygtig innovation ser Sten Græse store muligheder inden for 3D print:
”Faktisk tror jeg, at hele lager- og reservedelsproblematikken er en kæmpe bremse for innovation i mange fremstillingsvirksomheder – og måske i langt større omfang, end man lige skulle tro. Med 3D print kan vi tænke innovation på en helt ny måde. Ikke alene kan vi fremstille et lavere styktal; vi kan også lave langt mere komplicerede komponenter. 3D printeren skal jo hverken fræse, dreje eller svejse. Den printer bare og er som udgangspunkt ligeglad med kompleksitet. Samtidig giver den også mulighed for, at en stor del af vores metalkomponenter over tid kan udskiftes med plast. Jeg regner med at ca. 10 pct. af vores sortiment på nuværende tidspunkt kan 3D printes billigere end ved traditionel fremstilling.”
For Sten Græse er det vigtigt, at dvt for alvor sætter et tydeligt aftryk på bæredygtighedsagendaen:
”Hvis man ser på bæredygtighed, er det jo helt basalt, at man ikke producerer ting, der ikke bliver brugt. Reelt er der jo i dag flere hundrede kilo komponenter, vi lægger på lager, som aldrig nogensinde kommer videre, og sådan vil jeg tro, at de fleste produktionsvirksomheder har det. Med 3D print kan vi komme meget tættere på det magiske tal, nemlig at producere blot ét styk ad gangen.”
Derfor ser Sten Græse også store perspektiver i 3D teknologien – ikke blot for dvt som virksomhed, men også for kunderne:
”For enhver virksomhed er leverancesikkerhed alfa omega, og vi kender alle virksomheder, som har brændt sig, fordi en leverandør pludselig er væk, og man ikke længere kan skaffe reservedele. Her kan 3D print virkelig revolutionere forsyningskæden, fordi man jo blot skal have tegningerne, hvorefter man selv kan få printet de reservedele, man har brug for til sine anlæg.
Om få år spår jeg faktisk, at vi helt holder op med at sende reservedele til f.eks. Japan og USA og i stedet blot sender en e-mail med dokumentationen. Tænk hvor meget unødig transport og CO2-udledning forbundet herved, vi som samfund kunne skære væk, hvis alle virksomheder begyndte at tænke sådan. Det ville være revolutionerende for hele industrien.”
Sådan vil dvt bidrage til verdensmålene
- Nedbringe lager med 20 pct. gennem print-on-demand.
- Undgå at producere varer, som aldrig bliver anvendt, hvilket på den korte bane vil svare til cirka 200 kg pr. år.
- Øge kundernes leverancesikkerhed gennem hele anlæggets livscyklus.
- Undgå unødig transport ved at stille dokumentation til rådighed, så reservedele kan printes lokalt og dermed mindske CO2 – aftrykket.
Fakta om dvt
- dvt blev etableret helt tilbage i 1864 som producent af kemikalier til vaskeindustrien.
- I 1960’erne begyndte virksomheden at installere Milnor vaskemaskiner, og senere udviklede man også transportsystemer.
- I dag leverer dvt transport- og sorteringsanlæg til industrielle vaskerier over hele verden.
- dvt holder til i Frederikssund.
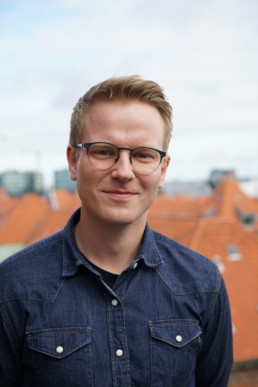
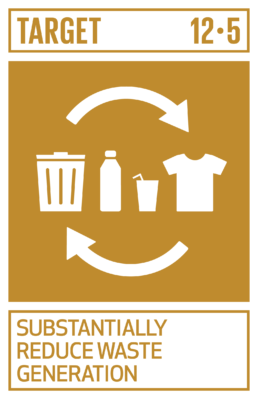
Med 3D print kan vi langt bedre supportere innovative startup-virksomheder
Carmo: Med 3D print kan vi langt bedre supportere innovative startup-virksomheder
Siden 1940’erne har danske Carmo fremstillet plast-komponenter til industrien. I dag åbner 3D print døren op for helt nye udviklingsopgaver, der bl.a. bygger på bæredygtighed og innovation.
Det var helt tilbage i 1946, at Carmo introducerede en af de første sprøjtestøbemaskiner i Danmark. Dengang, lige efter 2. Verdenskrig, var plast det nye vidundermiddel – billigt, fleksibelt og med et enormt potentiale til at revolutionere fremstillingssektoren og sætte helt nye standarder for masseproduktion.
Sprøjtestøbemaskinen hos Carmo blev da også starten på et langt industrieventyr, der lever videre den dag i dag. Det fortæller Anders Johnsen, VP R&D and Technology hos Carmo.
”Faktisk kan vi bryste os af at være pionerer inden for sprøjtestøbning gennem snart en menneskealder. Det har gjort os i stand til at opbygge en stor produktportefølje og en trofast kundeskare. I dag er vi bl.a. ISO 13485-certificeret til at levere medico-komponenter til eksempelvis urinposer. Samtidig leverer vi en lang række tekniske komponenter til industrien, herunder komponenter der kan højfrekvenssvejses på folier.”
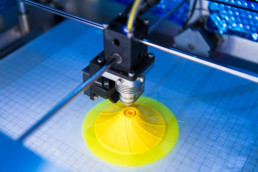
Som frontløbere inden for udviklingen af plastkomponenter var Carmo hurtige til at spotte, at 3D teknologien potentielt kunne rumme store muligheder inden for innovation og bæredygtighed. Derfor investerede man tidligt i en 3D printer på fabrikken i Espergærde for at tage de første spæde skridt og samtidig opbygge erfaring, fortæller Anders Johnsen:
”Vores første øvelser med 3D print var faktisk med robotgriberne til vores tekniske afdelinger. Med mere end 600 varegrupper har vi brug for en lang række forskellige gribere for at kunne automatisere produktionen. Langt hovedparten af disse bliver i dag printet i 3D, faktisk i så stort et omfang, at vores 3D printere nærmest kører i døgndrift.”
I dag er Carmos 3D printere for længst blevet en fast del af virksomhedens mange udviklingsopgaver. Derfor er Anders Johnsen og hans team klar til at gå endnu længere:
”Det har helt sikkert været vigtigt for os at gøre os en masse erfaringer for at forstå både mulighederne og kompleksiteten i 3D print. Det gør også, at vi føler os godt rustet til at tage de næste skridt. I tråd med bl.a. FN’s verdensmål vil vi gerne nedbringe vores lager og reducere spild ved at indføre print-on-demand. Vi vil også gerne kunne servicere lavvolumenprodukter. Endelig er der et enormt perspektiv i at kunne supportere startup-virksomheder med helt nye prototyper, der tidligere ville have været ekstremt dyre at fremstille ved hjælp af de traditionelle metoder. Også her åbner 3D print op for at tænke langt mere innovativt og bæredygtigt. I fremtiden kommer vi til at sige ja til langt flere af den slags opgaver.”
Selv om teamet hos Carmo med bistand fra Deloitte stadig er i gang med at lægge både en kort- og langsigtet plan for, hvordan virksomheden vil investere i 3D print, tør Anders Johnsen dog godt sætte tal på ambitionerne:
”Inden for 5 år vil vi skabe en årlig meromsætning på 5-8 mio. kr. i det omfang, at 3D print kan understøtte vores nuværende sprøjtestøbeforretning. Måske er potentialet endnu større, hvem ved? Det eneste vi ved med sikkerhed er, at vi hele tiden får nye aha-oplevelser, når vi kigger på 3D print. Hos Carmo er det en teknologi, der er kommet for at blive.”
Sådan vil Carmo bidrage til verdensmålene
- Nedbringe lager.
- Reducere spild ved at indføre print-on-demand.
- Servicere lavvolumenprodukter.
- Supportere startup-virksomheder med nye prototyper, der tidligere ville have været
ekstremt dyre at fremstille ved hjælp af traditionelle metoder. Også her åbner 3D print op for at tænke langt mere innovativt og bæredygtigt.
Fakta om Carmo
- Etableret under 2. Verdenskrig af Carl Mogensen, heraf navnet.
- Pionerer inden for sprøjtestøbning siden slutningen af 1940’erne.
- Carmo har netop været igennem et generationsskifte, hvor CEO Claus Steenstrup Ishøy har overtaget ejerskabet efter sin far.
- Carmo har i dag ca. 500 kunder på verdensplan.
- Virksomheden sælger ca. 80 pct. af sine produkter uden for Danmark.
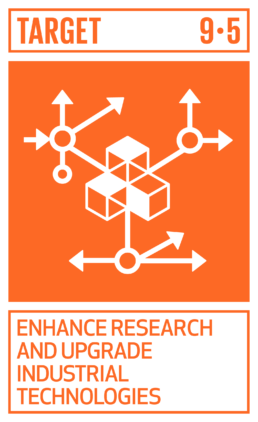
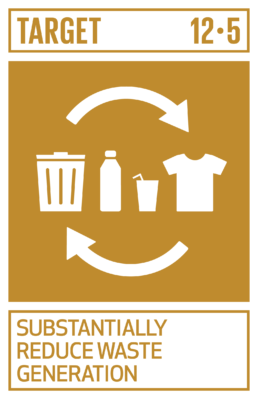
Danitech: Langt om længe er vi nået til et stadie, hvor det giver mening at 3D printe i metal
Danitech: Langt om længe er vi nået til et stadie, hvor det giver mening at 3D printe i metal
For sønderjyske Danitech, der er specialister i kraftfulde bevægelses- og kontrolløsninger, er det ikke blot et spørgsmål om at kunne 3D printe maskinkomponenter, men om at kunne 3D printe dem i metal.
Pappresseren på genbrugsstationen, affaldskomprimatoren bag supermarkedet eller løftebordet hos den store industrivirksomhed. Alt sammen er det eksempler på maskiner, der anvender moderne hydraulik og mekanik.
Hos Danitech kaldes den slags ’motion and control solutions’, en vital disciplin i konstruktionen af industrimaskiner. Selv om Danitech i mange år har været frontløbere på området, har virksomheden været tøvende med at udforske 3D teknologien på grund af de tekniske begrænsninger inden for metal-print. Men netop de begrænsninger er efterhånden ved at være fortid. Det fortæller Head of Business Development, Rasmus Iversen:
”Vi har haft mange diskussioner om 3D print hen over årene, men de er stort set alle sammen endt med konstateringen af, at 3D print primært egner sig til plastic. Sådan har det også været historisk, men sådan er det ikke nødvendigvis længere. Det har været en øjenåbner for os at finde ud af, at metal-print rent faktisk kan lade sig gøre.”
Danske 3Shape gør det uopnåelige til allemandseje
Danske 3Shape gør det uopnåelige til allemandseje
Med missionen ”innovate to improve patient care” har 3Shape sat sig på tandlægemarkedet med teknologi, der muliggør behandlinger og kvalitet, der ellers ikke var mulige.
3Shape laver scannere og software, der i kombination med 3D print stiller behandling til rådighed, som ellers var uopnåeligt. Tandlægerne får nogle redskaber, så de kan skabe proteser, gebis og meget andet langt mere præcist, hurtigere og billigere.
3Shapes historie starter egentlig med høreapparater, eller nærmere betegnet scannere til at kunne lave individuelle høreapparater. Og med en kontrakt med Widex, var starten til den store vækstsucces, som 3Shape er blevet, allerede lagt. Høreapparatsmarkedet er blevet vendt helt på hovedet med 3Shapes scannere og industriens produktion med 3D print. Fra store fabrikshaller med folk i hvide kitler med slibemaskiner, der bøjede, malede og limede til 3D print og montering af elektronik, design og software.
I 2005 gik 3Shape ind på dentalmarkedet, og er gået fra at være en start-up virksomhed til at have knap 1600 medarbejdere på verdensplan og et bruttoresultat der steg 6.721 % fra 2012-2016.
Men hvad er det så de kan?
3Shapes scannere og software, der kan bruges til bl.a. 3D print skaber mass customization produktion. Altså masseproduktion af individuelle produkter. Man kan producere mange enheder på én dag, men de kan alle være forskellige. Det er fx modeller af folks tænder, der før blevet lavet som gipsaftryk med langt flere skridt og til langt større gene for patienten. Så ikke alene gør man produktionen hurtigere og billigere, man forbedrer kvaliteten for patienterne og demokratiserer på sin vis markedet, fordi flere vil kunne få råd til at lave tænder, når man kan lave det med nye metoder.
Tandlægebranchen er ikke så hurtig at forandre som høreapparatsindustrien. Tandlæger laver rigtig mange forskellige ting. Bøjler, gebisser, implantater, broer, kroner m.m. Rigtig meget af det kan laves med 3D print, og spørger man David Fischer, der er Director for R&D Software hos 3Shape, vil rigtig meget blive lavet med 3D print i fremtiden.
”Ny teknologi kommer ind alle steder. Alle tandlægerne kommer til at have en scanner. Ligesom røntgen i dag. Og når du så har scanneren og det er nemt at designe produkterne, så er det helt oplagt, at næste skridt er en 3D printer i klinikken, så man kan producere på stedet”.
Han tilføjer, at der stadig vil være specialiserede produkter, der skal laves på laboratorier, men at de nye teknologiske muligheder også vil forandre arbejdsmarkedet for tandlæger og teknikkere i branchen.
Hvor hører arbejdskraften hjemme?
Med traditionelle metoder var der mange manuelle skridt og meget arbejde omkring tænder er håndlavet. Kompetencerne omkring det bliver bygget op over lang tid, fordi meget af det sidder i fingrene, når tænder skal bygges og komme til at se så naturtro ud som muligt.
Så udover at man får et andet produkt, så vil det også være et andet sæt arbejdskraft, der bliver behov for.
Og det er ifølge David Fischer ikke en dårlig ting, for der er ikke mange der uddanner sig til det håndværk, der tidligere var brug for. Det er tidskrævende at producere, så en stor del af produktionen vil alligevel blive sendt til Kina eller andre lande med lavere omkostninger, og det tager dermed også længere tid end det gør med scanning og 3D print.
Ved at introducere 3D print til produktionen, bliver det nogle andre mennesker og arbejdskraft, der er behov for. Man skal vide noget om computere og teknologi. Men det er ikke et kunstværk, der skal sidde i fingrene.
”Det vi ser i dag, er en maskine. Den bruger strøm og kører af sig selv. Hertil kommer efterbehandling, men overhead på dette retfærdiggør ikke at sende det til Kina. Og dermed flytter arbejdet tilbage til det sted, produktet skal bruges”, fortæller David Fischer.
For 3Shape og David Fischer er rådet til andre virksomheder omkring 3D print klart:
”Det lyder fancy med 3D print. Men det er relativt simpelt. Man tilføjer materiale i stedet for at fjerne det. Hvis man går med overvejelser om at kunne bruge 3D print, så er det bedste råd simpelthen at hoppe ud i det. Det kan sagtens være med én lille printer til at starte med, men få medarbejdere involveret, så opstår de nye ideer og man får hele tiden ny erfaring” slutter David Fischer.
Om 3Shape
- 3Shape blev stiftet i 2000 af Tais Clausen og Nikolaj Deichmann.
- Virksomheden omsatte i 2017 for 1,56 milliarder kroner mod 942 millioner kroner i 2016. En vækst på 60 % på et år.
- Overskuddet for 2017 var 457 millioner kroner efter skat, svarende til knap 30 % af omsætningen.
- 95 % af 3Shapes salg er til eksport.
- 3Shape har kontorer og udviklingsafdelinger i 20 lande.
- Hardwaren produceres på en fabrik i Polen.
- 3Shape har knap 1600 medarbejdere, hvoraf cirka en tredjedel arbejder med forskning og udvikling.
- I 2016 kårede Dagbladet Børsen 3Shape til året gazellevirksomhed, bl.a. med begrundelsen, at firmaets bruttoresultat på dentalt udstyr var stedet 6.721 % i løbet af de sidste fire år.