Solarsack
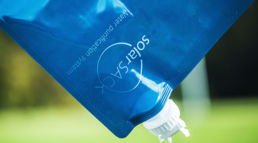
SOLARSACK
Den prisbelønnede vandbeholder SolarSack kan fjerne bakterier i drikkevand blot ved hjælp af solenergi. I AM HYBRID har de anvendt 3D-printede sprøjtestøbeforme til at optimere produktets design.
På verdensplan mangler over 800 millioner mennesker adgang til rent drikkevand og det problem vil iværksættervirksomheden SolarSack være med til at løse. Virksomheden har udviklet en vandbeholder i plastik, som kan fyldes med fire liter vand og placeres i solen i fire timer. Ved UV-stråling og varme fra solen bliver vandet renset for bakterier og brugeren kan herefter drikke vandet og genbruge posen til ny vandrensning. Indtil videre er posen blevet testet i flygtningelejre i Kenya og Uganda.
SolarSack vandt for nyligt 360 grader-prisen hos Dansk Erhverv, der uddeles til virksomheder der fremmer FNs 17 verdensmål, og var desuden nomineret i år til en Danish Design Award og Plastprisen for deres produkt.
Hurtigere og billigere produktudvikling
SolarSack har deltaget i AM HYBRID, hvor virksomheden har videreudviklet sit produkt. I projektet har SolarSack udviklet en hane til vandbeholderen, hvorpå man lettere kan tappe vandet med en særlig lukkemekanisme.
Teknologisk Institut og sprøjtestøbevirksomheden J. Krebs & Co. har været med til at hjælpe SolarSack i projektet.
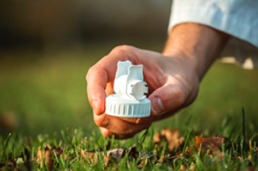
Traditionel udvikling af et plastprodukt kan koste mange penge og tager lang tid, og det har projektet AM Hybrid afhjulpet. Med en ny fremstillingsteknologi, der kombinerer 3D-print og forme til sprøjtestøbning af plast, har det været muligt at fremskynde fremstilling og test af det nye design i det plastmateriale, tappehanen skal fremstilles i og på denne måde minimeres risiko for fejldesign, siger Andreas Vestbø, seniorspecialist på Teknologisk Institut.
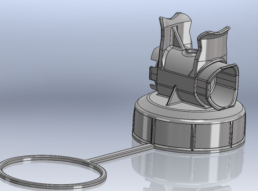
For en opstartsvirksomhed som SolarSack kan det have stor betydning at kunne teste designet løbende, uden at skulle investere i dyre forme til hver test.
Det har været essentielt at hanen er billig, da den skal passe til produktet, der i dag sælges i Uganda for 18 kr. stykket. Derfor har vi arbejdet med at gøre den vandtæt uden brug af ekstern gummipakning eller 2k støbning, og muligheden for at bruge FIM (Freeform Injection Molding) til at teste tolerancer og design for at optimere vandtætheden har derfor været uundværlig i processen.
– Alexander Løcke CTO og Founder af SolarSack.
Stor 3D-Printfarm i Humlebæk
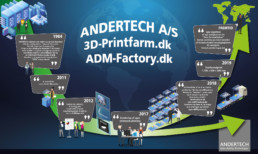
Stor 3D-Printfarm i Humlebæk
Andertech har de seneste år brugt AM til at producere et nyudviklet og patenteret produkt målrettet plastindustrien. Egentlig er produktet et ægte ADM mønstereksempel – idet det er udviklet på præmissen om at det skal og kun kan produceres med AM teknologi. ADM står for Additive Design & Manufacturing som i samlet koncept giver helt nye teknologiske og konkurrencemæssige muligheder og fordele. Disse fordele – og den store printkapacitet udbydes nu til andre virksomheder.
Andertechs idé er at udnytte allerede etablerede kapacitet til, at servicere hele produktionsbranchen gennem en såkaldt ”ADM-Factory eller 3D-Printfarm med foreløbig 60 printere. Med konceptet – der i et spinn-off får selvstændig identitet – kan der leveres 100-vis eller 1.000-vis af emner på få dage – og helt uden værktøjsomkostninger.
Næste step bliver automatisk flerfarveprint og oktober 2019 er det planen at lancere en mobil printfarm til brug for sports events og andre decentrale og real-time/at-place applikationer.
Andertech er en teknologi- og produktionsvirksomhed, der siden 1984 primært har serviceret plastindustrien, men i dag også servicerer andre produktionsindustrier. Andertech der har en stor afdeling for industriel IT, har blandt andet udviklet et digitalt overvågningssystem til produktionsmaskiner kaldet Whisper 4.0 og en HMI/SCADA Platform kaldet A-Link. Desuden er en proprietær IoT vejeplatform netop lanceret.
am-hub
Author
3DP Try out Linatech
Fra første print til kunde på under en måned
Linatech har i en måned lånt en 3D printer af Dansk AM hub og Center for Industri. De har printet elementer til deres blodprøve transportsystem. Blodprøver tranporteres i traditionelle reagensglas via et rørsystem direkte til laboratoriet. Da Linatech fik AM-teknologien ind i huset på forsøgsbasis skulle de finde ud af, hvad den kunne bruges til.
Martin Jerga, der er projektleder, fik lov til at eksperimentere med den nye maskine. Og den har kørt næsten uafbrudt i den måned, de havde den. Til blodprøve transportsystemet har Linatech erstattet flere elementer, herunder nogle ’skuffer’ som blodprøverne lander i. Normalt produceres de i stål. Med additiv manufacturing/3D print har Linatech designet skufferne i plastic på stedet og med en struktur, der betyder, at blodprøverne ikke lander forkert og i øvrigt bliver i den skuffe, de skal være i.
”Det, vi har lavet med 3D print ville man ikke kunne lave i stål”, fortæller Martin Jerga og forsætter: ”De 3D printede elementer gør det muligt at transportere blodprøverne/prøveglas uden at ødelægge dem, fordi det er designet med speciel struktur”.
Første bekendtskab med 3D print
Den lånte printer fra Dansk AM Hub er Linatechs første bekendtskab med 3D printere i huset, men det bliver næppe det sidste.
”Det har været meget givtigt til det pågældende projekt at forsøge os med 3D print. Det er hurtigt at komme i gang. Vi startede med at lave et print, hvor prøver landende forkert. Men så printede vi bare 27 ny emner. Det tog en dag – i stedet for en uge, som det havde taget hvis vi skulle have haft det fra en underleverandør”, fortæller Martin Jerga.
Projektet her har givet Linatech mulighed for at forbedre deres udviklingstid. Blodprøvemaskinen med de 3D printede elementer er allerede sendt ud til test hos kunden, og Linatech vil nu gå i gang med at regne på deres businesscase og finde ud hvordan de i fremtiden skal bruge 3D print.
Om Linatech
Linatech har igennem mange år udviklet og produceret håndterings- og produktionsudstyr til vindmøllebranchen og blandt andet medicinalbranchen. Linatech beskæftiger i dag 60 medarbejdere fordelt på to afdelinger i Vium og Thorning.
Virksomheden råder derfor i dag over 7500 m² produktions-, lager- og administrationsbygninger. Linatech samarbejder med virksomheder i så forskellige brancher som plast-, pap-, isolerings-, medico– og vindmølleindustrien Linatechs kompetencer spænder over flere forretningsområder:
- Engineering og Udviklingsprojekter
- Specialmaskiner
- Underleverandørarbejde
- Automation
- Montage
- Service
3D-printet raketbrændkammer i aluminium
3D-printet raketbrændkammer i aluminium
I samarbejde med studerende fra det danske DanSTAR-projekt, har Teknologisk Institut 3D-printet et raketbrændkammer i aluminium til den raket, som skal deltage i den internationale Spaceport America Cup i New Mexico i sommeren 2019. 3D-print var den oplagte løsning til brændkammeret, da det består af nogle meget komplekse indvendige geometrier, som nærmest er umulige at opnå med andre produktionsteknologier.
Samarbejdet om brændkammeret startede tilbage i sommeren 2018, hvor de studerende på DanSTAR-projektet tog fat i Teknologisk Institut, fordi de i samarbejde med industrielle samarbejdspartnere skulle bygge en raket til deltagelse i Spaceport America Cup – og her var 3D-print i metal en oplagt løsning til rakettens brændkammer. Det blev derfor aftalt, at DanSTAR skulle designe brændkammeret specifikt til at blive lavet i 3D-print, således at projektet fra start udnyttede de muligheder, der ligger i 3D-printteknologien. Resultatet blev et brændkammer i aluminium, som er designet med avancerede kølekanaler, der udelukkende kan laves i 3D-print.
– Vi har længe kendt til 3D-print i metal og vidst, at det var en mulighed. Men at få lov til at arbejde med processen åbner selvfølgelig for nogle nye muligheder, hvor man som studerende i højere grad begynder at overveje 3D-print til fremtidige projekter, da det er en genial måde at fremstille ekstremt komplekse geometrier eller prototyper på, siger Rasmus Arnt Pedersen, som er formand for DanSTAR.
Løbende sparring på design
Første del af opgaven med at 3D-printe et raketbrændkammer i aluminium var at nå frem til det helt rigtige design, og her har der været en løbende dialog, hvor 3D-printeksperterne fra Teknologisk Institut har givet sparring og feedback på DanSTARs designfiler med henblik på at nå frem til det bedste resultat, som passer til rakettens kravspecifikationer, og som samtidig er muligt at printe. Det resulterede undervejs i nogle designjusteringer – fx i højden, som måtte reduceres en smule for at passe i printerens byggekammer, samt i det ydre design med henblik på at kunne få restpulver ud af brændkammerets indvendige kølekanaler.
– Vi har løbende sparret med Teknologisk Institut under designprocessen, for der undervises ikke i design med henblik på additiv fremstilling på DTU, og selvom vi har stort kendskab til FDM-plastikprintere, er det alligevel en anden sag, når det er metalprint. Derfor har det været nødvendigt at blive hjulpet lidt på vej, men det har været en stor fornøjelse, og vi er endt med en state-of-the-art raketmotor, som kun de færreste raketklubber ville turde drømme om, fortæller Rasmus Arnt Pedersen.
Netop opgaven med at få restpulver ud af brændkammerets indvendige geometrier efter selve printprocessen var en af de mere spændende udfordringer for Teknologisk Instituts 3D-printeksperter, og den gav værdifuld læring til fremtiden – og et par grå hår undervejs.
– Vi endte med en funktionsmæssig løsning med små adgangspunkter til at få restpulveret ud. De er samtidig designet, så de giver DanSTAR mulighed for at sætte termofølere på brændkammeret og få driftsdata under test. Tillige er de konstrueret så adgangspunkterne kan forsegles med specialdesignede propper, når raketten skal flyve, fortæller Kristian Rand Henriksen fra Teknologisk Institut, som designede løsningen.
Intelligent brug af aluminium
I udviklingen af raketbrændkammeret har et væsentligt fokus været at holde vægten nede, da det betyder, at der skal bruges mindre energi på at løfte raketten fra jorden. Netop her kommer 3D-print til sin ret, fordi teknologien gør det muligt at bygge i lettere materialer pga. et design, hvor man køler brændkammeret samtidig med at forbrændingen finder sted – i stedet for at vælge et tungere materiale som fx kobber, der absorberer en masse varme, har man således kunnet bygge i aluminium, som er lettere.
Kølingen er nødvendig, da forbrændingen i kammeret sker ved meget høj temperatur – helt op til 3.200 °C – og meget få materialer kan holde til den temperatur, endsige bevare deres styrke. Når Teknologisk Institut og DanSTAR har valgt at 3D-printe brændkammeret i aluminium, som egentlig smelter ved meget lavere temperatur, er det fordi kammeret køles aktivt. Det er en tilgang, som er velkendt inden for rumfart, og samtidig har DanSTAR lavet et design, som virkelig udnytter mulighederne inden for 3D-print.
– Den raketmotor vi har lavet i samarbejde med Teknologisk Institut kunne ganske enkelt ikke produceres med konventionel produktion. Motoren er regenerativt kølet, hvilket vil sige at vi cirkulerer brændstoffet inde i væggen på motoren gennem en lang spiral. Denne motortype er mest anvendt i moderne raketmotordesign, men den er enormt kompliceret at producere, fordi man er nødt til at finde en måde at få kølemidlet ført ind i væggen. Men med 3D-print er den største udfordring snarere at designe en løsning – ikke at producere den, fortæller Rasmus Arnt Pedersen.
Forbrændingen i kammeret kører på tokomponent brændstof – NO2(eller lattergas) og isopropyl alkohol – og ved den regenerative køling køres den ene brændstofkomponent gennem en spiral, der løber indvendigt i brændkammeret. Det har den dobbelte effekt, at brændkammeret køles, så temperaturen holdes nede på et niveau, hvor kammeret ikke smelter og stadig har strukturel styrke, og samtidig varmes brændstoffet op, så der er mindre energitab, når det skal forbrændes – på den måde øges effektiviteten af forbrændingen.
Nye byggerekorder på Teknologisk Institut
For Teknologisk Institut har det været en spændende opgave at 3D-printe brændkammeret – både fordi det er designet med nogle komplicerede og skjulte indvendige geometrier, som ikke kan fremstilles på anden vis, men også fordi det stillede nogle udfordringer i forhold til byggestørrelse og kammerstørrelse, da der både blev bygget højt og helt til kanten af printkammeret.
– Dette er faktisk det højeste byg, vi indtil nu har lavet i metal, og det jo altid spændende at flytte grænserne, så vi får en bedre idé om, hvad vi kan i fremtiden. Og så er det jo spændende at arbejde sammen med engagerede mennesker, der kommer med ny viden og nye ideer, og brændkammeret har været et godt eksempel på, hvordan man kan komme uden om traditionelle begrænsninger, når man udnytter mulighederne ved 3D-print, fortæller Nikolaj Kjelgaard Vedel-Smith, der som konsulent på Teknologisk Institut har haft det direkte samarbejde med DanSTAR.
Om DanSTAR:
DanSTAR er et studenterdrevet projekt, hvor studerende fra DTU og Maskinmesterskolen i København samarbejder med industrielle partnere om at designe og udvikle en raket, der i sommeren 2019 skal deltage i SpacePort America Cup i New Mexico, USA i konkurrence med studerende fra hele verden.
DanSTAR raketten, der er 3,5 meter høj, skal flyve op i 9 kilometers højde, og den bærer 18 kg brændstof. Under opsendelsen er trykket i det 3D-printede aluminiumsbrændkammer på 20 bar, og brændstofblandingen skal brænde i 13 sekunder ved temperaturer op til ca. 3.200 °C.
3D-print er i øvrigt ved at blive mere og mere udbredt inden for rumfartsindustrien, fordi det er den bedste måde at løse udfordringerne med komplekse geometrier, og fx bruges 3D-print også af Elon Musks SpaceX og engelske Orbex, der også har kontor i Danmark
En ny måde at tænke på
En ny måde at tænke på
Da Johs. Pedersen tænkte de skulle i gang med 3D print var blikket rettet mod metalprint, fordi de primært laver reservedele i metal. De gik gennem et AM Inspire forløb med Danfoss og fik svar på en masse spørgsmål og mod på at gå stille og roligt i gang med at undersøge teknologien uden de helt store investeringer (Se mere om forløbet her).
Da Johs. Pedersen fik mulighed for at låne en 3D printer af Dansk AM Hub i en måned i 3DP Try Out gik de i gang med at printe og bruge af de erfaringer, de havde med fra forløbet i AM Inspire.
Efterfølgende er 3D print er for alvor kommet ind hos Johs.Pedersen, der ikke alene har købt en 3D printer, men også lavet deres eget 3D printcenter i den 43 år gamle maskinfabrik.
De printer modeller og holde-fixturer og det vækker stor begejstring i virksomheden.
”Det ændrer ens mind-set og giver en anden måde at tænke på”, fortæller Jesper Knudsen, der er Head of Technical Department hos Johs. Pedersen.
Ifølge Jesper Knudsen er der både tid og penge og spare ved at bruge 3D print, men også en verden af muligheder for hvad man kan producere fremadrettet.
Læs mere om 3DP Try Out og kontakt os hvis du er interesseret i at deltage.
Om Johs.Pedersen
JP koncernen har været en 100 %familieejet virksomhed siden grundlæggelsen i 1975.
De beskæftiger sig med produktion af pladedele, udstødningssystemer, olie og benzintanke til den Automotive branche. Produkterne afsættes dels via JP Group A/S, samt direkte til de store bilproducenters afdelinger for klassiske biler, herunder Porsche og Mercedes. Fremstilling og renovering af interiørkomponenter til togbranchen.
am-hub
Author
SMV: Vi vil ikke sige nej til en million igen
SMV: Vi vil ikke sige nej til en million igen
Erfarne virksomheder skal hjælpe andre virksomheder i gang med 3D-print i Dansk AM Hubs AM Inspire, som allerede har matchet Widex med Scandinavian Packaging, som vil bruge teknologien til at gribe flere opgaver.
- For cirka et år siden fik vi en henvendelse fra en kunde i Norge, som havde en opgave til en lille million kroner. Men vi endte med at sige nej til opgaven, fordi vi kun kunne få den produceret i Kina og leveringstiden var for lang i forhold til kundens behov. Hvis vi havde været lidt længere fremme med 3D-print, kunne vi sandsynligvis have løst opgaven i Danmark, fortæller Hanne Zinck Jørgensen, som er COO og partner i virksomheden Scandinavian Packaging.
Virksomheden lever i dag af at producere store partier emballage – primært flasker og kapsler i plast – og det har de succes med. Til gengæld kniber det med at gribe de mindre ordrestørrelser, hvor eksempelvis en hotelkæde ønsker at få designet og produceret en mindre serie shampoo-flasker. Den type opgaver er faktisk røget helt ud af Danmark.
- Når jeg f.eks. ser en lækker, økologisk creme i en beholder fra Kina, synes jeg, det er en skam. For den kunne vi formentlig producere mere bæredygtigt ved hjælp af 3D-print herhjemme, siger Hanne Zinck Jørgensen, som er uddannet plastingeniør og betegner sig selv som lidt af en ’emballagenørd’.
Brug for input til at komme videre
Scandinavian Packaging er allerede så småt i gang med 3D-print – og de har masser af mod på at gå videre. Indtil videre har de bare manglet den nødvendige erfaring/viden til at tage det helt rigtige næste skridt.
- Vi har allerede to mindre 3D-printere, som vi bruger til at lave prototyper, men vi har bl.a. brug for mere viden om, hvilke materialer til 3D-print, der er på markedet. Vi vil også rigtig gerne have input i forhold til, hvilken 3D-printer vi skal investere i næste gang, siger Hanne Zinck Jørgensen.
Den viden er de nu på vej til at få gennem projektet AM Inspire, som er udviklet af Dansk AM Hub og Dansk Industri. Projektets mål er at matche virksomheder, som har stor erfaring med AM-teknologi – som f.eks. 3D-print – med virksomheder, der mangler input på området.
Danmark er desværre bagud på AM-området i forhold til andre lande.Hanne Zinck Jørgensen, COO i Scandinavian Packaging
Deler viden for at komme i front
Scandinavian Packaging er blevet matchet med virksomheden Widex A/S, som producerer høreapparater og allerede har stor erfaring med 3D-print.
- Vi skal mødes med Widex første gang her i juni, og det ser jeg meget frem til. Og når vi er kommet lidt videre, vil vores virksomhed også med stor glæde give vores erfaringer videre til andre danske virksomheder, for Danmark er desværre bagud på dette AM-området i forhold til andre lande, påpeger Hanne Zinck Jørgensen.
AM Inspire er et samarbejde mellem Dansk AM hub og Dansk Industri, finansieret af Dansk AM hub, der er initieret og udviklet af Industriens Fond. Programmet er åben for virksomheder, der vil have mere viden om hvordan de kan få gavn af AM-teknologi.
Historien er bragt i DI Business: https://www.danskindustri.dk/di-business/arkiv/nyheder/2018/5/smv-vi-vil-ikke-sige-nej-til-en-million-igen/
Læs mere om AM Inspire og tilmeld din virksomhed: https://am-hub.dk/am-inspire/
AM Inspire: Kom godt i gang med 3D print
AM Inspire: Kom godt i gang med 3D print
I 2017 sparede Danfoss mere end 400.000 Euro på at 3D-printe. De har givet deres erfaringer videre til Johs. Pedersen, der nu vil se på, hvor 3D-print kan give værdi i virksomheden, der fremstiller reservedele til blandt andre Porsche og VW.
Danfoss Drives har inspireret den mindre virksomhed Johs. Pedersen til at komme i gang med 3D-print. Det er sket gennem Dansk AM Hubs virksomhedsprogram: AM Inspire, der er et inspirationsforløb til danske SMV’er, der er nysgerrige på, hvordan 3D print med fordel kan bruges i produktionen.
AM Inspire er i al sin enkelthed et forløb med to sparringsmøder mellem en produktionsvirksomhed og en inspirator, der kommer fra en virksomhed, der er kommet i gang med at bruge 3D print.
Johs. Pedersen, der fremstiller reservedele til klassiske biler som Porsche og VW, har gennemgået forløbet sammen med Danfoss Drives, der er så godt i gang med 3D print, at de i 2017 sparede mindst 400.000 Euro på selv at 3D-printe. Johs. Pedersen har nu en stor forventning om, at 3D-print skal reducere deres ”time to market” væsentligt.
Se med i videoen her og hør om både Danfoss og Johs.Pedersens erfaringer og forventninger til 3D print.
Freeform Injection Molding i små-skalaproduktion vinder frem
”Vores kunder oplever at Freeform Injection Molding giver en fantastisk mulighed for teste prototypen af i det rigtige materiale til en rigtig fornuftig pris.”
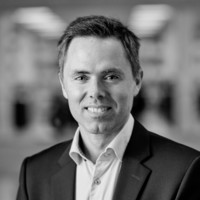
Krebs & Co. er en virksomhed i Skævinge, Nordsjælland, som har været i sprøjtestøbebranchen siden 1956. I dag er virksomheden to-benet. Dels sprøjteblæser og sprøjtestøber de, som de har gjort i mange år. For nylig har de investeret i 3D-print og Freeform Injection Molding.
Freeform Injection Molding er en hybrid af 3D-print og traditionel sprøjtestøbning. Fordelen er, at vi kan lave negativet eller skallen med 3D-printeren, som vi bagefter kan støbe ind i med allerede godkendte materialer. På den måde kan vi tage fat i materialer, der er godkendt til medicinsk brug. Kombinationen giver således en unik mulighed for at teste prototyper af i de rigtige materialer fra start, samtidig med at prisen holdes nede.
– Peter Bay, CEO i J. Krebs & Co.
I Danmark er mange teknologivirksomheder forholdsvis små, og derfor har de som oftest ikke de nødvendige ressourcer til at udvikle og producere nye teknologier. Det betyder, at det ofte er alfa og omega at samarbejde med en lang række aktører som videninstitutioner og andre private virksomheder.
En af de virksomheder, som J. Krebs & Co samarbejder tæt med, er AddiFab. Jylling-virksomheden er i disse måneder ved at tage springet fra innovationsvirksomhed til kommerciel vækstvirksomhed med FreeFrom Injection Molding som teknologisk flagskib.
For at teknologien Freeform Injection Molding rigtig skal vinde frem, kræver det løbende forbedringer af præcision og tolerance. Dertil skal produktionshastigheden øges – det er ikke forventeligt, at det skal være lige så hurtigt som traditionelt 3D-print, men det skal være hurtigere at arbejde med Freeform Injection Molding end at producere i metal. Målet er at kunne levere små serier eller prototyper med kort leveringstid, hvor træfsikkerhed kan garanteres.
Hos J. Krebs & Co er vi stadig i prototype-stadiet. Vi har en masse succeshistorier, men vi har selvfølgelig også en række historier, hvor det ikke gik, som vi håbede. Men sådan er det, når vi arbejder med nye materialer, der støbes ved over 300 grader og under meget højt tryk. Nu er der behov for en masse validering. Det kræver meget at føde en ny teknologi, og vi har det desværre med at sammenligne den nye teknologi med en gammel teknologi som sprøjtestøbning. Det betyder, at den nye teknologi risikerer at blive fejet af banen for hurtigt– og det er synd, siger Peter fra J. Krebs & Co.
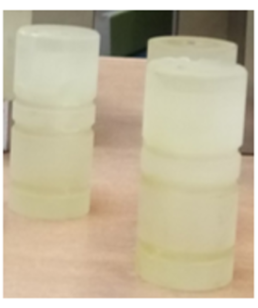
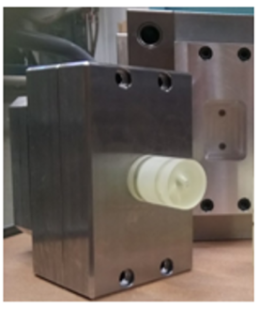
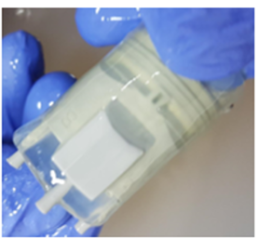
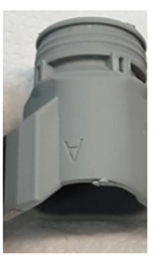
I AM HYBRID har Krebs og Co. anvendt FIM til en række produktudviklingsforløb sammen med deres kunder. Et eksempel er et el-stik til Danfoss A/S. Freeform Injection Molding har her givet stor mening, da det er tale om småskala produktion efter kundetilpasset design. De har også været med i en del af de efterfølgende cases til sammen med Teknologisk Institut at hjælpe virksomheder med FIM.
Vi har udelukkende 7 materialer, mange af dem fiberforstærkede, som vi bruger igen og igen. De er gennemtestede, og vi er rigtig gode til at lave produkter i dem. Vi har gennemsøgt markedet bl.a. i Tyskland og der findes i dag ikke nogen anden metode end FIM til at få produceret prototyper el. lave småskalaproduktion af nye designs i disse materialer.
– Saeed D. Farahani, Leder af Danfoss’ AM-afdeling
Silkeborg Stigefabrik - prototyping: Fra fire uger til fire dage
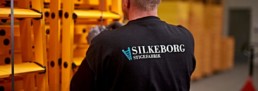
Silkeborg Stigefabrik – prototyping: Fra fire uger til fire dage
Alimak Group Denmark A/S er, via sit brand Silkeborg Stigefabrik, Danmarks største udbyder af stiger i træ, aluminium og glasfiber, foruden mobile lifte, stilladser, og specialløsninger.
Foruden professionelle stiger til bl.a. håndværkere, vinduespudsere og skorstensfejere, har Silkeborg Stigefabrik et bredt udvalg af produkter til den private. Brandet Silkeborg Stigefabrik har Danmarks største udvalg af stiger, stilladser og trapper – og samarbejder med nordens førende producenter, som sender varerne direkte fra fabrikken til din hoveddør. Markederne er – ud over privatsegmentet – generelt industri, entreprenører, bygningshåndværkere og vind industrien.
Baggrund for projekt
Alimak Group Denmark A/S har gennem de seneste år fået produceret plastikkomponenter hos eksterne leverandører i Fjernøsten, bl.a. fra Indien. Alimak Group Denmark A/S udvikler ikke selv deres prototyper in-house, da de ikke har maskine set-up, som kan løse disse opgaver. Alimak Group Denmark A/S har derfor søgt en proces – udvikling/fremstilling af prototype/proof of concept – og som kan skabe en kortere lead time frem tooling og den endelige fysiske udgave.
Hidtil af prototype-opgaven og ansvaret ligget hos Alimak´s indiske underleverandør, og man har derfor været afhængig af lang leveringstid af en given prototype – på op til 4 uger. Ofte har det yderligere vist sig, at den pågældende prototype ikke har været helt som forventet. Derfor er der tit påløbet yderlige 4 uger i processen før den endelige prototype er nåede frem til endelig godkendelse i Silkeborg.
Processen
I samarbejde med AM-HUB´s TRY OUT indledte Center For Industri og Alimak et fælles udviklingsprojekt med fokus på netop PROTOTYPING. Virksomheden fik stillet en Makerbot Replicator 3D printer til rådighed, som del af deres technology assesment proces.
Hos Alimak er der således først udført en technology-assesment. Her er 4 emner (både inden for hovedområderne udvikling/prototyping, produktion/AM og tooling) blevet udvalgt til at indgå i denne proces. Filer, tegninger, kostberegninger m.m. er indgået i udarbejdelse af technology assessment analysen. Her har Alimak in-house printet emner på en Makerbot Replicator 3D-printer, og lavet benchmark op mod ekstern udførelse og konventionel fremstillingsteknologi.
Alimak har i processen kunnet arbejde med filer, som de har modtaget fra kunder – til 3D-print og mhp at udføre proof of concept tests.
Med 50% infill er printertiden 3-4 timer for fremstilling af komponenten i nedenstående fig.
Forløbet
Alimak Group Denmark A/S modtager en 3D tegnet fil fra en kunde. Ud fra denne fil laver Alimak nu et 3D-print af emnet, som fremsendes til kunden. Protypen evalueres af kunden, som kunden godkender eller anviser ændringer og rettelser til, som de ændrer i tegningsfilen. Alimak Group Denmark A/S laver herefter endnu et 3D print, til endelig godkendelse hos kunden.
Udbytte
Dette forløb kan gennemføres over 2-4 dage og dermed reduceres lead time i forhold til den oprindelige proces med op til 4 uger. Desuden kan Alimak undervejs i processen ændre på konstruktionsparametre som design, infill og materialevalg m.m., hvis det skulle være nødvendigt for at øge styrke, varmetolerance m.m. af den 3D printede komponent.
Foruden det tidsmæssige udbytte er der desuden en omkostningsreduktion på anslået 50%.
”Vi kunne gennemføre 3D print forløbet og levere en 3D printet komponent til kunden på 3-4 dage – hvor det normalt kan tage op til 4 uger”
Henrik Gadgaard, Production/Purchasing Manager Silkeborg Stigefabrik
Foruden den direkte ovennævnte værdiskabelse hos Alimak, skabes der også større værdi for Alimak´s kunder og en strategisk værdi Alimak via en stærkere relation overfor kunden.
Efterfølgende TRY-OUT forløbet har virksomhedens ledelse truffet en strategisk beslutning om at anskaffe sin egen 3D-printer til virksomheden i Silkeborg.
HYTOR løser kundernes problemer gennem 3D print
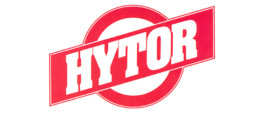
HYTOR løser kundernes problemer gennem 3D print
HYTOR består i dag af både HYTOR Fluid Solutions og HYTOR Tools Solutions. Som innovativ serviceminded gruppe designes og konstrueres der innovative systemløsninger med afsæt i hydraulik, ligesom man sælger proces og instrumenteringskomponenter i selskabet HYTOR Fluid Solutions, mens man i HYTOR Tools Solutions har fokus på levering, service og kalibrering af specialiseret værktøjsløsninger.
Design, konstruktion, samling og test udføres på eget værksted. Ligesom man er certificeret service og kalibreringsværksted for hydraulisk og elektrisk værktøj.
Sortimentet omfatter markedets bedste kvalitetsprodukter, der opfylder alle sikkerheds- og certificeringskrav. HYTOR er således i dag certificeret efter ISO 9001, ISO 14001 og OHSAS 18001.
Gennem HYTOR Tools Solutions serviceres primært vindmølleindustrien, men også forsyningskæden, den generelle industri og entreprenørbranche, med specialiseret værktøj inden for primært momentbespændingsteknologi, dækkende over blandt andet momentspændeværktøj, løfteværktøj, strækværktøj, møtrikknusere, momentnøgler (65.000Nm) samt flangeværktøj.
Med et ”rullende værksted” er HYTOR Tools Solutions med uddannede serviceteknikkere i stand til at servicere kunden on-site med reparation, service og kalibrering af specialiseret værktøj, og kan samtidig assistere kunderne med specielt vanskelige opgaver primært indenfor installation og service af vindmøller.
Med dette afsæt agerer HYTOR Tools Solutions problemløser for kunden og er parat til at modificere eksisterende løsninger både fra hovedkontoret i Esbjerg og on-site hos kunden.
I tæt samarbejde med Center for Industri har HYTOR Tools Solutions igangsat to forskellige projekter indenfor momentbespænding ved installation og servicering af vindmøller:
Projekt: COUNTER KEY
Et ændret behov banede vej for en nyudvikling af modholdsnøgler på bolte ved samling af naceller til vindmøller. Idegrundlaget var et betjeningsvenligt frigørelsesmodhold, som ikke i dag er tilgængeligt på markedet, og derfor skulle skabes fra bunden.
Teknikere hos HYTOR designede en prototype, som skabte grundlag for et 3D print PROTOTYPING projekt. Designet på frigørelsesmodholdet bestod af i alt 23 forskellige komponenter, hvori der også indgik komponenter som fjedre, bolte, afstands- og låseringe samt gummihåndtag.
En MAKERBOT Replicator 3D Printer blev stillet til rådighed hos HYTOR Tools Solutions af AM-HUB i samarbejde med Center for Industri, således at udviklings- og fremstillingsprocessen af prototypen på frigørelsesmodholdet var tæt på udviklerne.
Prototypen på frigørelsesmodholdet, (en proof-of-concept) af dette yderst komplekse specialværktøj, blev fremstillet på få dage, hvilket havde afgørende betydning for det totale tidsforbrug for færdigudvikling af frigørelsesmodholdet. Integration af 3D print i udviklingsfasen muliggjorde nedbringelse af den samlede lead-time fra idegrundlag til reelt værktøj med en faktor fem. Den samlede omkostning for udvikling har beløbet sig til en tiendedel set i forhold til omkostningerne ved en konventionel prototype – 3D prototype print sat op mod en prototype fra en værktøjsproducent.
Projekt: HYDRAULISK SPÆNDEVÆRKTØJ
En modifikation af et pågældende værktøj var nødvendig for at løse en opstået problematik omkring pladsmangel.
Ved hjælp af en scanning af det eksisterende specialværktøj, blev der omgående fremstillet en 3D model af de relevante værktøjer, som så kunne bearbejdes og justeres on-site, for at opnå det korrekte design for momentbespændingsopgaven inden for den plads, der var til rådighed omkring bolten.
Den tilpassede 3D model blev en afgørende faktor, og dermed grundlaget for en egentlig modifikation på det konkrete værktøj. Værktøjsproducenten kunne ud fra 3D modellen modificere specialværktøjet, så det passede til den givne momentspændeopgave.
En uge var hvad det tog, fra problemet opstod hos vindmølleproducenten til HYTOR Tools Solutions nåede frem til en løsning, uden at skulle gøre nytte af producenten. Ikke kun en markant besparelse af tid blev opnået, men omkostningerne for udviklingsforløbet har været en tiendedel af, hvad omkostningerne ville være for et nyt specialværktøj, som modificeres med risiko for ødelæggelse.
I denne case blev der også stillet en MAKERBOT Replicator 3D Printer til rådighed hos HYTOR Tools Solutions af AM-HUB i samarbejde med Center for Industri
Konklusion
Begge cases har vist en markant kortere leveringstid, konkret er der tale om faktor fire, i kraft af muliggørelse af prototyping ved hjælp af 3D print.
Ydermere har omkostningerne forbundet med egen in-house løsning været reduceret væsentlig, i forhold til estimerede omkostning forbundet med leverance fra en ekstern leverandør.
Godkendelsesproceduren, såvel internt som eksternt, har været kort og processen har været effektiv for samarbejdspartner og ikke mindst slutkunden.
To cases som virksomheden ser mange muligheder i, både i kraft af den hurtige udviklingsfase, men bestemt også omkostningerne forbundet med udviklingsfasen. Samtidig har det været med til at manifestere et allerede eksisterende godt samarbejde alle parter imellem.
Perspektivering
I begge tilfælde blev proto-typing løst ved hjælp af udlånt Makerbot Replicator printer fra AM-HUB / Center for Industri, der gjorde det muligt for virksomheden, i eget værksted, at løse opgaven og samtidig få proof-of-concept hos alle steakholders. En proces der både havde stor gevinst rent tidsmæssigt men også økonomisk.
Center for Industri danner rammerne for udvikling inden for fremstillingsindustrien og tilbyder assistance og viden i samarbejde med Dansk AM-HUB for udbredelse af udviklingsmulighederne inden for 3D print. Kontakt Center for Industri via http://www.centerforindustri.dk/ og hør mere om dine muligheder.
HYTOR udtaler:
Klaus H Rasmussen, Fluid:
“Det har været utrolig nemt at arbejde med 3D printerne, programmerne og materialerne er nemme at gå til og Center for Industri har været en god sparring i forhold til mulighederne og alt det praktiske”
Anne Mette Lorentzen, Marketing Chef:
”Vi ser gode muligheder for anvendelse af 3D print i vores videre samarbejde med vores kunder, det giver os blandt andet mulighed for at lave produktjusteringer i samarbejde med producenten langt hurtigere end tidligere”