3D print puster liv i udviklingsprojekter hos brændeovns-producenten
3D print puster liv i udviklingsprojekter hos brændeovns-producenten
Hos HWAM i Hørning producerer de brændeovne. Brændeovnene med elektronisk styring, så de kan blive styret med en app, da der sidder en elektronikboks under brændeovnen, der styrer lufttilførslen. Det styrer temperaturen og iltniveauet og sikrer en ren forbrænding. Det er til elektronikboksen, HWAM har eksperimenteret med 3D print.
I starten af 2020 ankommer Dansk AM Hub og CFI med en kasse til HWAM. I kassen er en makerbot 3D printer, der installeres og får til huse i HWAMs kantine den næste måned. De er med i Dansk AM Hubs projekt 3DP Try Out, der stiller en printer til rådighed til virksomheder i en måned ad gangen. Denne type printer producerer i plastik, og det rimer ikke umiddelbart på brændeovn, men hos HVAM laver man en boks til den intelligente styring i plast, og den seneste måned, er der blevet 3D printet nye prototyper til boksen.
”Vi har lånt en 3D printer, fordi vi syntes, det var rigtig spændende. Vi arbejder en del i plastik, blandt andet med denne her elektroniske styring, der sidder i et plastikkabinet, og der var det interessant, at vi kunne begynde at printe prototyper selv, så vi ligesom hurtigt kunne se, hvordan tingene ser ud”, fortæller Jakob Tophøj, Project Manager, HWAM og forsætter:
”Det er faktisk ret komplekst med alle de forskellige elementer og tilslutninger et modul består af, fx en motorholder, en underdel og en overdel. Ved at printe prototyper kan vi se, hvordan det hænger sammen. Det er jo klart, at man sparer en masse tid på at kunne printe sådan noget hen over natten i stedet for at skulle vente to til tre dage på at få det leveret fra en underleverandør”.
I løbet af den måned HWAM har lånt 3D printeren har både udviklingsafdelingen og konstruktionsafdelingen været i gang på printeren og fået et ret godt billede af, hvordan den kan bruges, og at der er masser af smarte måder at udvikle på med en 3D printer.
I forhold til vores udviklingsprojekter, så betyder det, at man ret hurtigt kan se om tingene passer sammen, om det kan trykkes sammen, om hullerne passer til hinanden. Når man trykker det sammen, er det vigtigt, at man kan se at det hele kører helt strømlinet. Det kan man se med det samme, fortæller Jakob Tophøj.
Den normale procedure for et udviklingsprojekt ville ellers være at få lavet nogle støbeforme, fx af en producent i Kina, og det tager lang tid at få de første prototyper hjem. Herefter skal de samles og først der, kan man se om de passer sammen. Med 3D print kan man se om tingene de passer sammen med det samme.
”Når vi skal have lavet prototyper, så plejer det normalt at tage to til tre uger at få dem fra Asien. Vores støbeforme får vi fra Belgien på cirka 14 dage. Med 3D print kan vi printe det i løbet af natten, og så kan vi allerede næste dag se resultatet, så det er klart det fremmer processen. Så der er ingen tvivl om, at det er fremtiden”, fortæller Jakob Tophøj.
Det betyder, at virksomheden sparer meget udviklingstid ved at bruge 3D print, fordi man lynhurtigt kan prøve om tingene passer sammen.
”Vi har blandt andet lavet sådan en røgring, som vi har fået 3D printet, og det er jo meget hurtigt at se om det passer, for normalt er det sådan noget der skal støbes i støbejern, og der er lidt lang leveringstid fra vores leverandør, når han skal lave prototyper, så det er helt klart en forbedring og en fremskyndelse af udviklingsprocessen”, siger Jakob Tophøj, Project Manager, HWAM.
Og han er da heller ikke i tvivl om, at det er noget HVAM skal arbejde videre med.
Rent strategisk vil 3D print kunne forkorte HWAMs ’lead time’ på mange udviklingsprodukter. Her kigger virksomheden også interesseret på metalprint med et ønske om at kunne lave prototyper på deres metalprodukter, som ikke først skal produceres for at se om de passer sammen. Det vil give en klar optimering af deres udviklingstid. Men Jakob ser mange muligheder, når først 3D print er kommet inden for døren og man kan printe alt fra hjælpeværktøjer til ting i dagligdagen, til hjælpi produktionen eller hvad man har behov for.
Hele organisationen har kigget på print
Jakob fortæller, at organisationen har taget meget godt imod printeren, som har stået og printet i kantinen, så hver gang folk har holdt pause, så har de stået og kigget meget nøjsomt efter og fulgt med i hvad det er den har printet og spurgt ind til det, så der har været meget interesse.
På sigt regner man i HWAM med, at det her er noget man vil kunne komme til at spare mange penge og meget tid på at bruge – og det bliver nemt at prøve nye ideer af, også dem, der først kan synes lidt skørt, men som faktisk ender med at blive en rigtig god løsning, eller rigtig god forretning.
Om HWAM
- HWAM er én af Danmarks største producenter af arkitekttegnede brændeovne.
- De producerer intelligente brændeovne, der kan styres med en app.
- Gennem mere end 35 år har HWAM designet og produceret moderne brændeovne af høj kvalitet og med flere patenterede fordele – først under navnet ABC og i dag under de to brands HWAM og WIKING.
- Virksomheden er grundlagt af Vagn Hvam Pedersen i 1973 og i dag ejer en af sønnerne Stefan 25% og Seguin 75%. Virksomheden bliver i dag ledet af sønnen Stefan og er på den måde gået i sin fars fodspor ind i brændeovns-branchen.
- HWAM har hjemme i Hørning syd for Århus, hvor teknologi og godt gedigent håndværk går op i en højere enhed. Omkring 80 % af produktionen eksporteres til kunder i hele Europa, med Tyskland som hovedmarked.
The Impact of COVID-19 on the Future of Advanced Manufacturing and Production
The Impact of COVID-19 on the Future of Advanced Manufacturing and Production: Insights from the World Economic Forum’s Global Network of Advanced Manufacturing Hubs
With the arrival of the coronavirus pandemic, there is a need for the industry to move faster than ever to support the response to this international health crisis while mitigating its impact on manufacturers and their respective supply chain networks around the globe. This paper reflects an aggregate of voices from the Global Network of AMHUBs and focuses on COVID-19’s impact in each region; response efforts from manufacturing and governments; and best practices to achieve rapid results and mitigate repercussions to subsequent regions by learning from those affected earlier. The World Economic Forum is committed to enabling and amplifying cross-AMHUB collaborations that accelerate the industry’s ability to adapt to the current crisis while ensuring future resilience through advanced manufacturing technologies and processes.
Læs mere om World Economic Forum netværket for Advanced Manufacturing og Dansk AM Hubs rolle
3D laser cladding fjerner slitageproblem i trykbeholdere
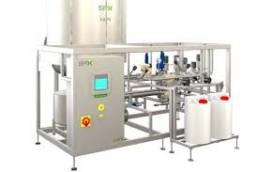
SPX FLOW leverer procesanlæg til fødevareindustrien. Tidligere måtte kunderne i værste fald udskifte trykbeholderne efter et år på grund af slitage fra flydende fødevarer. Det problem har FORCE Technology løst gennem additive manufacturing, hvor man ved brug af laser svejser en hårdfør metallegering på de rustfrit stålbeholdere.
Det er nu syv år siden, SPX FLOW første gang fik svejset en særligt slidstærk metallegering på en plade af rustfrit stål, som er en del af en trykbeholder i deres procesanlæg til fødevareindustrien. ”Den holder stadig. Vi kan ikke måle nogen slitage,” konstaterer Knud Thorsen, Mec. Engineer + IWE, Global R&D Technology i SPX FLOW.
Det er ellers ikke småting, som pladen bliver udsat for. Det vil sige – det er det faktisk! Nogle flydende fødevarer indeholder abrasive partikler, altså små partikler med en slibende effekt. Det kan f.eks. være kakaomælk, hvor der er sandpartikler fra høsten af kakaobønner. Det er helt normalt og uproblematisk for den menneskelige organisme. Det samme kan man ikke sige om beholderen. ”Fødevaren bliver ledt ind i beholderen med høj hastighed. Resultatet kan sammenlignes med, at overfladen konstant bliver sandblæst,” forklarer Knud Thorsen.
Minimering af nedetid for SPX FLOWs kunder
Tidligere var resultatet da også, at der blev slidt hul i beholderen. Ofte allerede efter et år, selvom procesanlægget som helhed er bygget til at holde til kunne køre i døgndrift i 30 år. Det var en præmis, som kunderne var bekendt med og accepterede, og løsningen var som regel, at procesbeholderen blev udskiftet med en ny for at minimere nedetiden for anlægget. Alternativet var at afmontere og sende beholderen til reparation hos SPX FLOW i Silkeborg. En sådan reparation kunne tage uger at få udført og sendt tilbage, afhængig af hvilken verdensdel procesanlægget stod i.
”Uanset løsningen vil man som fødevareproducerende virksomhed helst undgå at have smede gående og reparere på sit procesanlæg,” siger Knud Thorsen.
Alt i alt har den slidstærke metallegering, som FORCE Technology svejser på med 3D laser cladding, derfor stor værdi for SPX FLOWs kunder. Og dermed for SPX FLOW.
”I dag har alle vores specialprocesbeholdere, som kan blive udsat for abrasivt slidende fødevarer, påført denne metallegering. Og det er vores kunder ganske tilfredse med, og de vil gerne betale for få denne forbedring med,” siger Knud Thorsen.
FORCE Technology sørgede for dokumentation
Noget andet, som har stor værdi for SPX FLOW, er FORCE Technologys håndtering af den nødvendige dokumentation af metallegeringen. Da SPX FLOW i sin tid kom til FORCE Technology med problemet med procesbeholderne, var det med et krav om, at overfladebelægningen først og fremmest skulle være meget slidstærk over for abrasiv slitage. Den skulle være 100 procent massiv og uden nogen form for porer eller revner af hensyn til hygiejnen. Desuden måtte den påførte overflade på ingen måde måtte kunne falde af gennem hele beholderens levetid og kontaminere fødevaren. Sidst, men ikke mindst skulle den påførte overflade kunne godkendes i henhold til reglerne for fødevarekontaktmaterialer i både EU og USA.
”Dertil kom trykbeholdergodkendelsen af svejseproceduren, som er særdeles omstændelig – specielt i Nordamerika. De amerikanske ASME VIII-trykbeholderregler kan være noget af en jungle at finde vej igennem, og det var på et tidspunkt næsten ved at få hele projektet til at gå i stå. Men det lykkedes for FORCE Technology at finde en brugbar vej i henhold til ASME VIII,” siger Knud Thorsen.
Han er i det hele taget tilfreds med det mangeårige samarbejde med FORCE Technology, som han betegner som førende på sit felt. ”Jeg har selv en baggrund som svejseingeniør og har gennem årene gentagne gange haft stor gavn af FORCE Technologys ekspertise inden for svejseteknologi samt korrosion og metallurgi. Vi har til tider også haft glæde af FORCE Technologys laboratorier til at dykke dybere ned i forskellige specialcases,” fastslår Knud Thorsen.
Læs mere om historien her
Terma reducerer materialeforbrug og produktionstid markant med AM
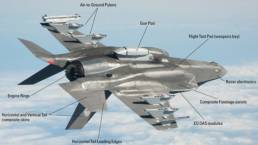
Hidtil har Terma A/S haft et højt materialespild i produktionen af en særlig komponent til kampflyet F-35. Det forsvinder med 3D-print, som også reducerer produktionstiden fra 55 til knap 5 timer. Næste skridt er at bruge fremstillingsmetoden til store støbeforme og aluminiumsdele.
De fleste virksomheder vil gå langt for at undgå et højt materialespild. Det behøver Terma ikke. Det rækker at tage til Lindø på Fyn. Her kan FORCE Technology producere en særlig komponent til kampflyet F-35 Lightning II ved hjælp ved hjælp af additive manufacturing (AM)-teknologi.
“Hidtil er vi startet med 219 kg stål, som vi så har bearbejdet til en komponent på syv kg. Med additive manufacturing kræver det kun ti kg pulver,” siger Philippe Lovejoy-Courrier, der er Senior Specialist i Innovation Lab, Smart Manufacturing hos Terma.
Additive manufacturing reducerer ikke alene materialeforbruget. Det er også væsentligt hurtigere at producere komponenten. Med traditionel spåntagende bearbejdning tager det 55 timer. Dertil kommer efterbearbejdningen. Med additive manufacturing kan den produceres på 4,5 timer.
Kort produktionstid giver potentielt kort leveringstid, og når komponenten ydermere kan produceres on-demand, behøver Terma ikke have dyrt 15-5PH-stål på lager, hvilket giver et bedre cashflow.
Særdeles høje kvalitetskrav
Komponenten indgår som førnævnt i kampflyet F-35 Lightning II. Med andre ord er kvalitetskravene særdeles høje, og Terma har da også udsat komponenten, der er produceret med additive manufacturing, for omfattende udmattelsestest.
“Resultaterne er lovende, så næste skridt er at gå i dialog med kunden,” (Lockheed Martin, red.) siger Philippe Lovejoy-Courrier.
Komponenten kan blive startskuddet til, at Terma producerer andre komponenter i 15-5PH-stål med additive manufacturing. “Det er udfordrende at bearbejde den type stål. Generelt kan man sige, at laser cladding giver god mening ved hårde metaller og høje materialeomkostninger,” siger Philippe Lovejoy-Courrier.
Storskala 3D-print af støbeforme
Apropos dyre materialer er Terma og FORCE Technology også i gang med andet projekt, som er blevet muligt med den nye Multiprocess Large Scale 3D-printer på Lindø. “Vi ser på, om det kan lade sig gøre at printe støbeforme i højnikkellegeringen Invar. I dag producerer vores underleverandør støbeformene ved at svejse tykke plader sammen for derefter at fræse støbeformene ud. Vi taler om to-tre tons råmateriale pr. støbeform til en kilopris på 200-300 kr., og det er også dyrt i lønomkostninger og tager lang tid. Det ikke er unormalt med et halvt års leveringstid. I stedet kunne det være rart at have en tønde pulver stående på Fyn, så støbeformene kunne produceres hurtigere og billigere,” siger Philippe Lovejoy-Courrier og fortsætter: “Ingen har før printet støbeforme i Invar, så det er innovativt, men også udfordrende, for støbeformene er tre-fire kvadratmeter store.”
Førende i Skandinavien
Philippe Lovejoy-Courrier bringer også et tredje materiale i spil, når han taler om potentialet i 3D-print.
“Stål udgør under én procent i vores produktion. Vi anvender først og fremmest aluminium. Derfor er det interessant for os, at der udvikles højstyrkelegeringer i aluminium på pulverform. Det har ikke været muligt før nu, hvor der er kommet nogle nye pulvertyper, som vi ser på sammen med FORCE Technology. I første omgang vil vi fremstille nogle prøvestænger og trække dem over for at undersøge udmattelsesegenskaberne,” siger Philippe Lovejoy-Courrier.
Dermed fortsætter Terma og FORCE Technology et mangeårigt samarbejde, som han er glad for. “Man er i gode hænder hos FORCE Technology. De har alle de relevante kompetencer i huset, og det tager aldrig lang tid at få en kompetent vurdering – f.eks. hvis vi har lavet en udmattelsestest af et materiale, og ikke forstår resultatet. De er de bedste inden for metallurgi, og ingen andre i Skandinavien mestrer den type additive manufacturing, som vi får lavet på Lindø,” understreger Philippe Lovejoy-Courrier.
Læs mere om historien her
3D print sikrer hurtig produktion af værnemidler under corona-krisen
3D print sikrer hurtig produktion af værnemidler under corona-krisen
Hos AddiFab i Jyllinge fandt man, under Corona-krisen i 2020, en ny anvendelse af 3D print teknologien.
3D print og additive manufacturing er kendt for korte udviklingsforløb, lave opstartsomkostninger og lokal produktion. Egenskaber, der har vist sig at være meget værdifulde i en sundhedskrise, hvor hele verden skulle bruge værnemidler samtidig. 3D print virksomheder i hele verden – også i Danmark – gik i gang med at printe værnemidler, som fx visirer. Dansk AM Hub samlede alle 3D print aktører sådan, at man til myndigheder havde et samlet overblik over printkapaciteten i Danmark. Det overblik og en samlet indgang har vi nu til fremtiden.
Men det er ikke kun med visirer, der blev udviklet og tænkt kreativt. Hos AddiFab gik man, efter italiensk forbillede, i gang med at omdanne en full face snorkelmaske til et værnemiddel mod Covid-19. AddiFab og overlæge Michael Mølmer satte sig for at lave adaptere til snorkelmaskerne, så de kan påmonteres et bakteriespærrende filter.
Efter blot tre ugers udvikling og tests i Danmark er AddiFab nu i gang med selv at producere den nyudviklede filter-adapter, og de første 2.000 stk er bestilt af McGill University Hospital i Canada. Derudover har også er lande som Italien, Spanien, USA, England, Belgien og Sverige udtrykt interesse.
Filter-adapteren, som lyder navnet MiMo, er en ny opfindelse fra overlægen Michael Mølmer, der har set et potentiale i at kunne montere et filter på de allerede tætte snorkelmasker. Maskerne dækker hele ansigtet og filteret i adapteren holder covid-19-virussen ude. Maske, adapter og filter er blandt andet testet af personalet på danske hospitalers corona-afsnit.
Læge Michal Mølmer viser masken frem på billedet.
– Vi står helt klar til rådighed for det danske sundhedsvæsen og er klar til at levere til Danmark. Vi er i dialog med myndighederne og venter på deres reaktion. I mellemtiden hører vi fra mange andre lande, som er interesseret, og derfor er vi allerede i fuld gang med at skrue op for produktionen, siger AddiFabs adm. direktør Lasse G. Staal.
En million masker i USA
Der er ultrakort fra udvikling til produktion, når det er muligt at 3D-printe. Og det vil Lasse G. Staal gerne udnytte i forhold til at hjælpe under corona-krisen.
– Vi valgte at påtage os opgaven med selv at producere, fordi det skulle gå ekstremt hurtigt med at komme i gang. Og MiMo-adapteren er en god løsning, fordi der allerede er rigtigt mange dykkermasker, hvor filteret passer til. Alene i USA er det måske helt op imod en million masker, fortæller Michael Mølmer.
AddiFab forventer at kunne fremstille 500-1000 adaptere om dagen, hvilket kun dækker en meget lille del af det forventede behov.
– Hvis du som udgangspunkt siger, at der er brug for en million adaptere, så forslår vores produktion i Jyllinge som en skrædder en vist varmt sted. AddiFab skal ikke være en flaskehals, så derfor har vi taget næste skridt med vores partner Mitsubishi Chemical, som kan producere markant flere end os. Det vil gøre det muligt at imødekomme den efterspørgsel, vi forventer, siger Lasse G. Staal.
Læs også historien i DI Business: https://www.danskindustri.dk/di-business/arkiv/nyheder/2020/4/danske-varnemidler-efterspurgt-kloden-rundt/
Læs mere om AddiFab og corona initiativet: https://www.addifab.com/addifab-covid19-reponse
Hybrid: 3D print og sprøjtestøbning skaber adapter til snorkelmaske
3D Printing + Injection Molding: COVID-19 Collaboration Scales Up Within A Week
MiMo mask adaptors made using KRAIBURG TM7 MED grade [Image: AddiFab]
Scaling up production to help in the fight against pandemic poses certain challenges — that are increasingly possible to overcome.
Most uses of 3D printing in addressing COVID-19 are quick-response, stop-gap supply chain needs for personal protective equipment (PPE) and other need-it-now goods. It is generally acknowledged that these first response measures are just that: a first response, typically the vanguard of full-scale efforts realized by more traditional mass production manufacturing like injection molding.
A new joint effort, though, is seeing the benefit of 3D printing combined with injection molding to have reached a scale solution in six days.
Read the full story: 3D Printing + Injection Molding: COVID-19 Collaboration Scales Up Within A Week
The New York Times on Danish corona initiative
Danish Charity Network to 3D Print Protective Visors
New York Times March 26, 2020
COPENHAGEN — A group of Danish entrepreneurs have started a charity network that stands ready to make up to 20,000 protective visors a day using 3D printers, in an attempt to meet rising demand from doctors and nurses combating the coronavirus outbreak.
Read the full article in The New York Times
3D Print corona-beredskab
3D Print corona-beredskab
Vi samler et beredskab til at kunne 3D printe emner til hospitaler i forhold til Corona.
I Italien er der blevet fremstillet ventiler til respiratorer til hospitaler i forbindelse med Corona-krisen. I Danmark arbejder det danske 3DP øko-system på at være klar til det, at kunne gøre det samme.
Med 3D print kan man skabe fx ventiler præcist og hurtigt. Dansk AM Hub arbejder på at identificere emner, fx ventiler til respiratorer , som kan blive en mangelvare under corona-krisen til de danske hospitaler. Emner som kan 3D printes, så det kan produceres i en fart i Danmark.
Vi har en stærk branche af AM /3D print-aktører i Danmark, som alle vil hjælpe, men vi mangler konkrete emner, som vi kan begynde at tegne og omsætte til 3D print.
Vi er gået i gang med at kontakte medico-tekniske afdelinger på hospitalerne, men opfordrer også aktører til at kontakte os, hvis de har viden, filer og andet der kan bruges.
Du kan tage skrive til os på info@am-hub.dk eller kontakte Frank Rosengreen Lorenzen på frl@am-hub.dk
Læs mere om det italienske eksempel hos BBC.
Læs også finans.dk: 3D-printede produkter forsøger at komme Danmark til undsætning
Wohlers report 2020
New Wohlers Report 2020 Documents More than 250 Applications of Additive Manufacturing
Fort Collins, Colorado, USA, March 18, 2020—Wohlers Associates, Inc. today announced the publication of Wohlers Report 2020, the 25th annual installment of its undisputed, industry-leading report on additive manufacturing (AM) and 3D printing. Often referred to as the “bible” of 3D printing, the new report provides a unique window into the constantly advancing global industry. The publication provides countless details on AM applications, software, workflows, materials, systems, and post-processing. It gives specifics on patents, startups, investment, and research and development, and the future of AM.
The 380-page report includes a wealth of information on AM industry growth, including more than 250 examples of AM applications in production or development.
Read the danish press release from Teknologisk Institut: Ny rapport viser solid global vækst for 3D-print
In one case, Jabil redesigned an impeller for manufacture by AM. Instead of 73 metal parts assembled by hand, the impeller is made of fiber-reinforced polymer composite in a single part. Fifty impellers can be produced in the time it previously took to make one.
This week, it was announced that Italian firm Isinnova had designed and produced many respirator valves in under two days. The effort was in response to an urgent call for help from a hospital in northern Italy that was overwhelmed with COVID-19 patients. Ten patients were able to breathe with the aid of a machine that included the 3D-printed valve.
The era has begun where the users of AM are in the driver’s seat, pushing boundaries of what AM can achieve in production applications. System manufacturers, service providers, and producers of materials are responding with offerings to match.
Wohlers Report 2020 builds upon input from a record ensemble of 129 service providers, 114 manufacturers of industrial AM systems, and 40 producers of third-party materials and desktop 3D printers. The report documents government-sponsored research and development, collaborations and consortia, and the activities of 139 academic and research institutes around the world. Seventy-nine co-authors and contributors in 33 countries provided expert views and opinions in the report.
New and expanded features of the 2020 edition include:
- Maturing and emerging applications of AM for series production
- Review of AM in the dental industry
- Commentary on 77 early-stage investments valued at $1.1 billion
- Compilation of 72 industry partnerships from the past 12 months
- Expert reports from 35 countries
- Tables of systems, third-party materials, software tools, and emerging technologies
The 380-page Wohlers Report 2020 includes 42 charts and graphs, 168 tables, and 377 images and illustrations. It also includes more than 145 pages of supplemental online content available exclusively to the buyers of the report. More information on the new report is available here.
About Wohlers Associates, Inc.
The company offers an unparalleled window into AM and 3D printing. The independent consulting firm of 33 years provides technical, market, and strategic advice on the new developments and trends in rapid product development and AM. Wohlers Associates counts 275 organizations in 27 countries among its clients. Separately, the company has provided advice to more than 180 investors.
Plus Pack: Fra ide til forretning på seks måneder
Fra ide til forretning på under seks måneder
Det startede med et spørgsmål på et strategiforløb hos ledelsen i Plus Pack. ”Hvad sker der med 3D print. Er der noget her, vi går glip af”. Og det spørgsmål blev startskuddet til at komme med på Dansk AM Hubs AM Generatorforløb, som primært består af to workshops, hvor man arbejder med egne ideer til, hvor 3D print kan bruges i forretningen. Plus Packs ide gik på at forsøge at lave prototyper på en nemmere måde ved hjælp af 3D printede komponenter til presseværktøj.
”Vi vil gerne lave skræddersyede emballageløsninger, og det kræver en tæt dialog med kunden. Det kan vi have, når vi kommer med en realistisk prototype udover en tegning og 2D model, siger Bastian Fietje, Manager of Group Projects, Plus Pack.
Plus Pack har eksperimenteret med at 3D printe værktøjskomponenter i nylon, som i dag laves i stål. Det giver mulighed for en iterativ udviklingsproces, hvor Plus Pack hurtigere kan producere realistiske prototyper af aluminiumsbakker, som kunden kan teste og evaluerer. Før foregik udviklingen ofte ud fra tegninger og 2D modeller, og når Plus Pack skulle i gang med at producere aluminiumsbakken, så måtte de bestille de dyre værktøjskomponenter i stål.
Det specialdesignede værktøj til fx bunden af en foliebakke kan printes på et par dage og kræver en dags efterbehandling, hvilket står i kontrast til at vente 12-15 uger på værktøjskomponenterne i stål, som samtidig ikke giver mulighed for nye tilpasninger.
”Det giver et helt andet samarbejde med kunden i forhold til at skræddersy deres produkter”, fortæller Bastian Fietje.
På en konkret opgave fik Plus Pack hurtigt brug for at kunne lave en prototype til en ny kunde. En fransk snegleproducent havde et behov for en aluminiumsbakke, med fordybninger i bunden, så sneglene ikke rutsjer rundt. Plus Pack lykkedes med at 3D printe et nyt bunddesign og derved lave en skræddersyet bund til sneglene. Det tog en uges tid at designe, 3D printe og producere prototypen, og kunden kunne derved lynhurtigt give feedback på bakkens design og funktionalitet.
Bastian Fietje beskriver værdien i organisationen som to-foldig. Dels har brugen af 3D print en stor værdi internt i organisationen, fordi de har kunnet re-tænke den måde de designer produkter på. Der er ting, man kan teste, og 3D print rykker ved forestillingen om, hvad der er muligt.
Herudover har det stor værdi for deres kunder. ”Vi kommer med en rigtig bakke som prototype, så de kan prøve den af, og se hvordan emballagen opfører sig, når den bliver brugt”, fortæller Bastian Fietje.
3D print har helt klart fået en plads hos Plus Pack, og Bastians opfordring til andre virksomheder er da også klar: ”Det er bare med at komme i gang. Brug 3D print til at forsøge og eksperimentere. Ellers finder man ikke de gode muligheder” slutter han.
Om Plus Pack
Plus Pack er en international og innovativ virksomhed med hovedkontor i Danmark og med produktion i såvel Danmark (Odense) som i Belgien (Genk). Plus Pack er en familieejet virksomhed med rødder tilbage til 1914, og virksomheden drives i dag af 4. generation i Haustrup-familien. Plus Pack er specialiseret i udvikling og produktion af emballage-løsninger til fødevareindustrien og er i dag en af Europas førende virksomheder indenfor fremstilling af aluminium- og plastemballage med salg til 50 forskellige lande. Plus Pack har 220 medarbejdere, virksomheden vækster og er midt i en spændende udvikling med udgangspunkt i løftet ”We make food stand out”.