Videnscenter åbner 3D-labs på tre erhvervsskoler
Videnscenter åbner 3D-labs på tre erhvervsskoler
Nu kan erhvervsskoleelever få fingrene i 3D-teknologi, og byggefagene står i forreste række for at udnytte mulighederne.
Videnscenter for Håndværk – Design & Arkitektur åbner tre 3D laboratorier på tre store erhvervsskoler i landet. Nu kan erhvervsskoleelever fremover i deres undervisning eksperimentere med 3D printere, Virtual Reality, laser cuttere, 3D design mm. Åbningen fandt sted torsdag på Techcollege i Aalborg, Mercantec i Viborg og hos Next Uddannelse København.
De tre 3D-Labs er sat i verden for at udvikle erhvervsuddannelserne, så det forhåbentlig bliver mere attraktivt for unge at tage en uddannelse hvor man bruger sine hænder – men samtidig har mulighed for at lege med den nyeste teknologi.
Ole Heinager, direktør hos Next Uddannelse København og formand for DEG, understreger vigtigheden af at fremtidssikre uddannelserne: ”Hvis ikke vores unge elever og lærlinge kommer ud med den her teknologiforståelse, så får de et chok når de for alvor rammer arbejdsmarkedet derude”.
I Aalborg er begejstringen stor, og tømrerelev Philip Gerdes kan se fremtiden for sig: “Der er ingen tvivl om, at det også vil finde vej til for eksempel byggepladser, så hvis vi som tømrere lige mangler et bestemt stykke til et hjørne, så kan vi printe det frem for at skulle bestille det,” siger han.
Investeringerne på de tre skoler skal føre erhvervsskoleeleverne ind i det 21. århundredes 3D-teknologi. En teknologi, der stadig vinder heftigt frem, og som visualiserer problemløsninger på en hel ny måde: ”Det har været rigtig fedt, og en helt ny måde at se tingene på. Det giver en helt ny vinkel og et nyt perspektiv,” siger Simon Alexander Arnby, der er eux-tømrer-elev.
Hans klassekammerat, Claus Hønborg, er først lige blevet introduceret til VR, men bruger det allerede instinktivt og hurtigt. Han siger om mulighederne med 3D-lab: ”Det er federe end at sidde og tegne på en computer. Man se hvordan det er, og hvordan det føles at være derinde”.
Helt overordnet er det vigtigste, at eleverne får lov til at eksperimentere med 3D og snuse til mulighederne. Udstyret skaber en attraktiv teknologisk undervisning for de unge, og muligheden for at fordybe sig i 3D, VR og laser cuttere.
”Det er fedt at få adgang til alt det udstyr. Det gør det lidt sjovere at få at vide mandag morgen, at man skal sidde og tegne hele dagen”, slutter Claus Hønborg.
Vær bevidst om dit juridske ansvar ved brug af 3D print
Juridisk ansvar og 3D print
Accura advokater har samlet en række anbefalinger til dig, der bruger 3D print.
Det er vores erfaring, at virksomheder som til daglig er i berøring med 3D-print eller 3D-printede produkter ofte står med en række juridiske udfordringer, som kan være svære at identificere og som ofte bliver glemt eller nedprioriteret. Dette betyder, at mange virksomheder i dag uforvarende tager nogle betydelige juridiske og økonomiske risici, som i mange tilfælde forholdsvist enkelt ville kunne imødegås eller i hvert fald minimeres, skriver Accura, der her sætter fokus på Forskning og udvikling, juriske aspekter ved Joint Ventures i forbindelse med 3D print, samt varemærkebeskyttelse i Kina.
Få Accuras nyhedsbrev i PDF her:
3D print har skåret otte uger af DAFAs udviklingstid på nye produkter
3D print har skåret otte uger af DAFAs udviklingstid på nye produkter
Hos DAFA laver de produkter i skum, gummi og plastmaterialer til byggeri, industri og vindenergi, som eksempelvis pakninger, fugebånd, lyd- og vibrationsdæmpende løsninger. Kort sagt alt inden for skum og gummi, alt hvad der kan dæmpe, beskytte og tætne. Det kan være i en højtaler der sidder i en bildør, i et display der sidder i instrumentbrættet til en bil, det kan være i en ovnlåge, det kan være en køkkenmaskine eller en boremaskine eller en vindmølle, der skal være tæt for regnvand.
Og nu har DAFA også investeret i en 3D printer. Det sker efter at have deltage i Dansk AM Hub og Center For Industris 3DP Try Out, hvor virksomheder kan låne en printer i en måned.
Henrik Pedersen er Project Manager i DAFA og fortæller, at når de har kigget på 3D print og valgt at investere i egen printer, så er det for at kunne imødekomme kunder inden for det segment, der hedder ’støbte pakninger’. Det kræver specialproduceret værktøj og ved at 3D printe designet kan de få verificeret designet med det samme.
”Normalt er det en lang proces fra man får produktet tegnet, til man får de første prøver fra støbt værktøj, som typisk ligger mellem 6-10 uger alt efter hvor kompliceret det er. Den proces vil vi meget gerne springe over, så vi kan få valideret designet ved at lave en 3D-model. Printer vi så en 3D model, har vi sådan set svaret med det samme, som vi kan afprøve i vores applikation eller vi sende det direkte til kunden, og vi kan rette til med det samme. Når kunden er tilfreds bestiller vi værktøjet. Man sparer egentlig et langstrakt udviklingsforløb, og man sparer en masse værktøjer”, forklarer Henrik Pedersen.
Det betyder, at når man bestiller værktøjet, så er det det rigtige første gang og for vores kunder er det en stor tidsfaktor og omkostninger, vi reducerer.
DAFA var med i 3DP Try Out i starten af 2020 og har siden investeret i egen printer og fået ordre på nogle af de ting de har 3D printet og sendt til kunder.
”Det betyder, at vi har skåret otte uger af udviklingsforløbet og kunden får verificeret, at det her design det passer ind i konstruktionen, før vi bestiller forme. Så for os betyder det, at vi er hurtigere fremme hos kunden, og har en højere sandsynlighed for at lande en ordre. Samtidig sparer kunden også tid i forhold til at man ellers vil skulle tilbage og rette i værktøjet. Dermed får de i vores optik en bedre service end de ville have fået før, hvor man skulle vente. Så vi har udelukkende positiv erfaring med 3D print” siger Henrik Pedersen.
Et begejstret salgsteam
Også DAFAs salgs-stab har taget godt i mod de 3D printede prototyper, fordi de kan levere prototyper i løbet af én arbejdsdag.
”Hvis man får en forespørgsel, så kan man forberede sig som sælger ved at få printet en model inden man skal til det første salgsmøde, så du faktisk har en model med, som du kan vise kunden og snakke ud fra og det er altid rart at have noget i hænderne, så er der ikke så langt fra idé til ordre. Og det er jo i den sidste ende én af de årsager til at vi har investeret i 3D print – for at kunne generere mere omsætning”, fortæller Henrik Pedersen, som regner med at DAFA vil bruge 3D print både internt og til kundeforespørgsler.
For DAFA er det en strategisk satsning, at de har investeret i 3D print, som skal løfte deres udviklingshastighed. De har investeret i en noget mere avanceret 3D printer end den de brugte i projektet. I den kan man blande materialerne digitalt, dvs. så kan man blande et meget hårdt og et meget blødt materiale digitalt, så man selv kan bestemme hvilken hårdhed, man printer i og man kan kombinere en hård og en blød gummi i samme print.
”Det giver mulighed for at printe i den hårdhed kunderne efterspørger, hvorimod hvis man havde investeret i en lidt billigere teknologi, så ville man have haft et hårdt gummiagtig materiale, men slet ikke i de bløde varianter, som vi har brug for. Derfor har vi valgt at investere i en maskine, der er lidt dyrere, men som er rettet mere den verden som DAFA er en del af – altså gummi og støbte emner, slutter Henrik Pedersen.
Fakta
DAFA er en familieejet virksomhed, som blev grundlagt i 1939 af Børge Norby. Den daværende fremstilling og montering af bronzetætningslister har udviklet sig til produktion af produkter i skum, gummi og plastmaterialer til byggeri, industri og vindenergi, som eksempelvis pakninger, fugebånd, lyd- og vibrationsdæmpende løsninger.Efter etablering og opkøb af datterselskaber i udlandet beskæftiger DAFA gruppen samlet ca. 350 medarbejdere fordelt på tre kontinenter og i otte lande, med produktion i Danmark, Italien, Polen og Kina.
DAFAs hovedkvarter ligger i Aarhus, Danmark.
Meggit prøver 3D print
Meggit prøver 3D print i AM Inspire
Meggit har deltaget i AM Inspire med Danfoss som den erfarne mentor. Hos Meggit har 30 ud af 110 medarbejdere været med til at bruge 3D printeren. Et program der er udviklet af Dansk AM Hub og DI.
Der er blandt andet blevet skabt en holder, der kan håndtere mange små emner i produktionen, og hos Meggit er man ivrig efter, at komme i gang med de mange muligheder 3D print giver til fx prototyper og afprøvning af nye ideer.
Med AM Inspire og mentorforløbet er de kommet godt fra start.
3D print giver kørestolsbrugere styringen
3D print giver kørestolsbrugere styringen
Hos Aabentoft i Hornslet er man vant til at lave specialdesignede og kundetilpassede produkter. Og nu har de fået et nyt værktøj til netop det.
I starten af 2020 lander en ny maskine hos Aabentoft. Den er kun til låns, men det skal vise sig, at den hurtigt erstattes af en egen indkøbt en af slagsen. Aabentoft har deltaget i Dansk AM Hub og Center for Industris 3DP Try Out. Her låner virksomheder en 3D printer i en måned af gangen, og så er det ellers bare at komme i gang.
Hos Aabentoft laver de salg, service og totalløsninger indenfor REHAB-branchen og MEDICO-branchen. Totalløsninger til styring af joystickstyrede el-kørestole, samt al form for service og reparation af el-kørestole og andre former for handicaphjælpemidler, er én af virksomhedens forcer. Alle kørestolsbrugere er unikke, hvilket kræver, at stolen ligeledes er unik.
Der hvor 3D print giver rigtig god mening for Aabentoft er ved de mange specialproducerede hjælpemidler, de laver til fx kørestolsbrugere. Det kan være mennesker, der har nedsat muskelstyrke, som ikke kan betjene panelet eller joystikket på det standard-producerede kontrolpanel på kørestolen. Her kan man hurtigt designe en enhed, knap, nyt joy-stick eller hvad den enkelte har behov for, for at kunne betjene en kørestol.
”Normalt ville man skulle producere mange af en enhed, af fx printholdere, stik adaptere og lign, men med 3D print kan man skræddersy et produkt og lave en enkelt enhed tilpasset den enkelte bruger”, fortæller Rasmus Koch, Teknikker i Aabentoft.
Samtidig tager det ofte lang tid at få fremstillet de tilpassede produkter, og her ser virksomheden også store muligheder i at kunne nedbringe udviklings- og produktionstid for disse emner ved at lave dem med 3D print.
”Vi laver ofte specialproducerede emner, så til det vi laver, der er 3D print et rigtig godt medie, og noget vi glæder os til at dykke mere ned i”, siger Per Aabentoft, direktør i Aabentoft.
Per Aabentoft er ikke sikker på, at der vil være en økonomisk gevinst lige nu og her ved 3D print, men han er ret sikker på, at de kan lave et bedre produkt ved at kunne producere de tilpassede holdere og andet, der kan gøre en verden til forskel for fx en kørestolsbruger, der ikke selv ville kunne betjene et kontrolpanel på kørestolen uden en specialtilpasset enhed, der fx gør, at man kan dreje på knapper med håndfladen i stedet for fingrene eller lign.
Hos Aabentoft har de selv investeret i en 3D printer efter at have været med i 3DP Try Out og har store forventninger til hvad man kan på sigt med 3D print.
”jeg ser et stort potentiale i nicheproduktionen, at vi kan lave små enheder, som er 100% specialiserede til den enkelte bruger”, slutter Rasmus Koch.
Om Aabentoft
A/S Aabentoft yder salg, service og totalløsninger indenfor REHAB-branchen og MEDICO-branchen, på landsdækkende plan.
Hovedsædet er beliggende i det nordlige Århus, og de har en underafdeling på Sjælland. Virksomheden startede med én mand, i 1985, og er nu vokset til at beskæftige p.t. 22 medarbejdere.
Design din virksomheds fremtid
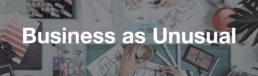
Design din virksomheds fremtid
Gennem Industriens Fond og indsatsen GenstartNU tilbyder Designit, Dansk AM Hub og en række partnere et gratis udviklingsforløb, der lærer dig at anvende designmetoder, som en måde at identificere muligheder, skabe innovation og forretningsudvikling. Forløbet er målrettet danske SMV’er og vil gennem en række workshops hjælpe 100 virksomheder til at bruge design til at accellerere genstarten i kølvandet på corona.
Business as Unusual forløbet tilbyder en anderledes måde at gentænke din virksomhedes værditilbud. I vil i forløbet blive introduceret til øvelser og værktøjer, der i en designproces åbner op for nye perspektiver og muligheder, der kan være med til at genstarte og gentænke en ny fremtid for virksomheden.
Forløbet af delt ind i 3 faser:

Få inspiration og introduktion til en række konkrete metoder og værktøjer som I kan bruge hjemme i virksomheden med det samme. Værktøjerne kan blandt andet hjælpe jer med at forstå jeres marked, kunder og udfordringer fra et nyt perspektiv.
I første fase har vi plads til 100 virksomheder.
Gå i dybden med konkrete udfordringer for jeres virksomhed og få sparring til hvordan design kan hjælpe med at skabe nye ideer til løsninger. Efterfølgende vil du zoome ind på konkrete ideer og skabe helstøbte koncepter rundt om ideen.
I anden fase har vi plads til 60 virksomheder.
Få hjælp til design af en prototype der er skræddersyet til din virksomhed. Prototypen kan være en digital løsning, et fysisk produkt, en service eller en forandringsproces. Gennem forløbet finder vi frem til hvilken prototype der er mest relevant for dig.
I sidste fase har vi plads til 10 virksomheder.
Det er gratis for enhver SMV i Danmark at deltage i forløbet. Du kan læse meget mere om forløbet, betingelser for deltagelse og praktisk information på: business-as-unusual.dk
Hvis du har spørgsmål til projektet, kontakt venligst Søren Hansen via skh@am-hub.dk
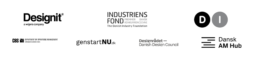
3D print puster liv i udviklingsprojekter hos brændeovns-producenten
3D print puster liv i udviklingsprojekter hos brændeovns-producenten
Hos HWAM i Hørning producerer de brændeovne. Brændeovnene med elektronisk styring, så de kan blive styret med en app, da der sidder en elektronikboks under brændeovnen, der styrer lufttilførslen. Det styrer temperaturen og iltniveauet og sikrer en ren forbrænding. Det er til elektronikboksen, HWAM har eksperimenteret med 3D print.
I starten af 2020 ankommer Dansk AM Hub og CFI med en kasse til HWAM. I kassen er en makerbot 3D printer, der installeres og får til huse i HWAMs kantine den næste måned. De er med i Dansk AM Hubs projekt 3DP Try Out, der stiller en printer til rådighed til virksomheder i en måned ad gangen. Denne type printer producerer i plastik, og det rimer ikke umiddelbart på brændeovn, men hos HVAM laver man en boks til den intelligente styring i plast, og den seneste måned, er der blevet 3D printet nye prototyper til boksen.
”Vi har lånt en 3D printer, fordi vi syntes, det var rigtig spændende. Vi arbejder en del i plastik, blandt andet med denne her elektroniske styring, der sidder i et plastikkabinet, og der var det interessant, at vi kunne begynde at printe prototyper selv, så vi ligesom hurtigt kunne se, hvordan tingene ser ud”, fortæller Jakob Tophøj, Project Manager, HWAM og forsætter:
”Det er faktisk ret komplekst med alle de forskellige elementer og tilslutninger et modul består af, fx en motorholder, en underdel og en overdel. Ved at printe prototyper kan vi se, hvordan det hænger sammen. Det er jo klart, at man sparer en masse tid på at kunne printe sådan noget hen over natten i stedet for at skulle vente to til tre dage på at få det leveret fra en underleverandør”.
I løbet af den måned HWAM har lånt 3D printeren har både udviklingsafdelingen og konstruktionsafdelingen været i gang på printeren og fået et ret godt billede af, hvordan den kan bruges, og at der er masser af smarte måder at udvikle på med en 3D printer.
I forhold til vores udviklingsprojekter, så betyder det, at man ret hurtigt kan se om tingene passer sammen, om det kan trykkes sammen, om hullerne passer til hinanden. Når man trykker det sammen, er det vigtigt, at man kan se at det hele kører helt strømlinet. Det kan man se med det samme, fortæller Jakob Tophøj.
Den normale procedure for et udviklingsprojekt ville ellers være at få lavet nogle støbeforme, fx af en producent i Kina, og det tager lang tid at få de første prototyper hjem. Herefter skal de samles og først der, kan man se om de passer sammen. Med 3D print kan man se om tingene de passer sammen med det samme.
”Når vi skal have lavet prototyper, så plejer det normalt at tage to til tre uger at få dem fra Asien. Vores støbeforme får vi fra Belgien på cirka 14 dage. Med 3D print kan vi printe det i løbet af natten, og så kan vi allerede næste dag se resultatet, så det er klart det fremmer processen. Så der er ingen tvivl om, at det er fremtiden”, fortæller Jakob Tophøj.
Det betyder, at virksomheden sparer meget udviklingstid ved at bruge 3D print, fordi man lynhurtigt kan prøve om tingene passer sammen.
”Vi har blandt andet lavet sådan en røgring, som vi har fået 3D printet, og det er jo meget hurtigt at se om det passer, for normalt er det sådan noget der skal støbes i støbejern, og der er lidt lang leveringstid fra vores leverandør, når han skal lave prototyper, så det er helt klart en forbedring og en fremskyndelse af udviklingsprocessen”, siger Jakob Tophøj, Project Manager, HWAM.
Og han er da heller ikke i tvivl om, at det er noget HVAM skal arbejde videre med.
Rent strategisk vil 3D print kunne forkorte HWAMs ’lead time’ på mange udviklingsprodukter. Her kigger virksomheden også interesseret på metalprint med et ønske om at kunne lave prototyper på deres metalprodukter, som ikke først skal produceres for at se om de passer sammen. Det vil give en klar optimering af deres udviklingstid. Men Jakob ser mange muligheder, når først 3D print er kommet inden for døren og man kan printe alt fra hjælpeværktøjer til ting i dagligdagen, til hjælpi produktionen eller hvad man har behov for.
Hele organisationen har kigget på print
Jakob fortæller, at organisationen har taget meget godt imod printeren, som har stået og printet i kantinen, så hver gang folk har holdt pause, så har de stået og kigget meget nøjsomt efter og fulgt med i hvad det er den har printet og spurgt ind til det, så der har været meget interesse.
På sigt regner man i HWAM med, at det her er noget man vil kunne komme til at spare mange penge og meget tid på at bruge – og det bliver nemt at prøve nye ideer af, også dem, der først kan synes lidt skørt, men som faktisk ender med at blive en rigtig god løsning, eller rigtig god forretning.
Om HWAM
- HWAM er én af Danmarks største producenter af arkitekttegnede brændeovne.
- De producerer intelligente brændeovne, der kan styres med en app.
- Gennem mere end 35 år har HWAM designet og produceret moderne brændeovne af høj kvalitet og med flere patenterede fordele – først under navnet ABC og i dag under de to brands HWAM og WIKING.
- Virksomheden er grundlagt af Vagn Hvam Pedersen i 1973 og i dag ejer en af sønnerne Stefan 25% og Seguin 75%. Virksomheden bliver i dag ledet af sønnen Stefan og er på den måde gået i sin fars fodspor ind i brændeovns-branchen.
- HWAM har hjemme i Hørning syd for Århus, hvor teknologi og godt gedigent håndværk går op i en højere enhed. Omkring 80 % af produktionen eksporteres til kunder i hele Europa, med Tyskland som hovedmarked.
The Impact of COVID-19 on the Future of Advanced Manufacturing and Production
The Impact of COVID-19 on the Future of Advanced Manufacturing and Production: Insights from the World Economic Forum’s Global Network of Advanced Manufacturing Hubs
With the arrival of the coronavirus pandemic, there is a need for the industry to move faster than ever to support the response to this international health crisis while mitigating its impact on manufacturers and their respective supply chain networks around the globe. This paper reflects an aggregate of voices from the Global Network of AMHUBs and focuses on COVID-19’s impact in each region; response efforts from manufacturing and governments; and best practices to achieve rapid results and mitigate repercussions to subsequent regions by learning from those affected earlier. The World Economic Forum is committed to enabling and amplifying cross-AMHUB collaborations that accelerate the industry’s ability to adapt to the current crisis while ensuring future resilience through advanced manufacturing technologies and processes.
Læs mere om World Economic Forum netværket for Advanced Manufacturing og Dansk AM Hubs rolle
3D laser cladding fjerner slitageproblem i trykbeholdere
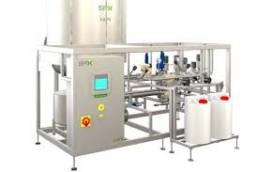
SPX FLOW leverer procesanlæg til fødevareindustrien. Tidligere måtte kunderne i værste fald udskifte trykbeholderne efter et år på grund af slitage fra flydende fødevarer. Det problem har FORCE Technology løst gennem additive manufacturing, hvor man ved brug af laser svejser en hårdfør metallegering på de rustfrit stålbeholdere.
Det er nu syv år siden, SPX FLOW første gang fik svejset en særligt slidstærk metallegering på en plade af rustfrit stål, som er en del af en trykbeholder i deres procesanlæg til fødevareindustrien. ”Den holder stadig. Vi kan ikke måle nogen slitage,” konstaterer Knud Thorsen, Mec. Engineer + IWE, Global R&D Technology i SPX FLOW.
Det er ellers ikke småting, som pladen bliver udsat for. Det vil sige – det er det faktisk! Nogle flydende fødevarer indeholder abrasive partikler, altså små partikler med en slibende effekt. Det kan f.eks. være kakaomælk, hvor der er sandpartikler fra høsten af kakaobønner. Det er helt normalt og uproblematisk for den menneskelige organisme. Det samme kan man ikke sige om beholderen. ”Fødevaren bliver ledt ind i beholderen med høj hastighed. Resultatet kan sammenlignes med, at overfladen konstant bliver sandblæst,” forklarer Knud Thorsen.
Minimering af nedetid for SPX FLOWs kunder
Tidligere var resultatet da også, at der blev slidt hul i beholderen. Ofte allerede efter et år, selvom procesanlægget som helhed er bygget til at holde til kunne køre i døgndrift i 30 år. Det var en præmis, som kunderne var bekendt med og accepterede, og løsningen var som regel, at procesbeholderen blev udskiftet med en ny for at minimere nedetiden for anlægget. Alternativet var at afmontere og sende beholderen til reparation hos SPX FLOW i Silkeborg. En sådan reparation kunne tage uger at få udført og sendt tilbage, afhængig af hvilken verdensdel procesanlægget stod i.
”Uanset løsningen vil man som fødevareproducerende virksomhed helst undgå at have smede gående og reparere på sit procesanlæg,” siger Knud Thorsen.
Alt i alt har den slidstærke metallegering, som FORCE Technology svejser på med 3D laser cladding, derfor stor værdi for SPX FLOWs kunder. Og dermed for SPX FLOW.
”I dag har alle vores specialprocesbeholdere, som kan blive udsat for abrasivt slidende fødevarer, påført denne metallegering. Og det er vores kunder ganske tilfredse med, og de vil gerne betale for få denne forbedring med,” siger Knud Thorsen.
FORCE Technology sørgede for dokumentation
Noget andet, som har stor værdi for SPX FLOW, er FORCE Technologys håndtering af den nødvendige dokumentation af metallegeringen. Da SPX FLOW i sin tid kom til FORCE Technology med problemet med procesbeholderne, var det med et krav om, at overfladebelægningen først og fremmest skulle være meget slidstærk over for abrasiv slitage. Den skulle være 100 procent massiv og uden nogen form for porer eller revner af hensyn til hygiejnen. Desuden måtte den påførte overflade på ingen måde måtte kunne falde af gennem hele beholderens levetid og kontaminere fødevaren. Sidst, men ikke mindst skulle den påførte overflade kunne godkendes i henhold til reglerne for fødevarekontaktmaterialer i både EU og USA.
”Dertil kom trykbeholdergodkendelsen af svejseproceduren, som er særdeles omstændelig – specielt i Nordamerika. De amerikanske ASME VIII-trykbeholderregler kan være noget af en jungle at finde vej igennem, og det var på et tidspunkt næsten ved at få hele projektet til at gå i stå. Men det lykkedes for FORCE Technology at finde en brugbar vej i henhold til ASME VIII,” siger Knud Thorsen.
Han er i det hele taget tilfreds med det mangeårige samarbejde med FORCE Technology, som han betegner som førende på sit felt. ”Jeg har selv en baggrund som svejseingeniør og har gennem årene gentagne gange haft stor gavn af FORCE Technologys ekspertise inden for svejseteknologi samt korrosion og metallurgi. Vi har til tider også haft glæde af FORCE Technologys laboratorier til at dykke dybere ned i forskellige specialcases,” fastslår Knud Thorsen.
Læs mere om historien her
Terma reducerer materialeforbrug og produktionstid markant med AM
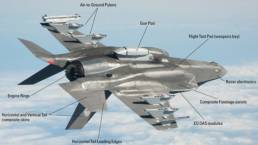
Hidtil har Terma A/S haft et højt materialespild i produktionen af en særlig komponent til kampflyet F-35. Det forsvinder med 3D-print, som også reducerer produktionstiden fra 55 til knap 5 timer. Næste skridt er at bruge fremstillingsmetoden til store støbeforme og aluminiumsdele.
De fleste virksomheder vil gå langt for at undgå et højt materialespild. Det behøver Terma ikke. Det rækker at tage til Lindø på Fyn. Her kan FORCE Technology producere en særlig komponent til kampflyet F-35 Lightning II ved hjælp ved hjælp af additive manufacturing (AM)-teknologi.
“Hidtil er vi startet med 219 kg stål, som vi så har bearbejdet til en komponent på syv kg. Med additive manufacturing kræver det kun ti kg pulver,” siger Philippe Lovejoy-Courrier, der er Senior Specialist i Innovation Lab, Smart Manufacturing hos Terma.
Additive manufacturing reducerer ikke alene materialeforbruget. Det er også væsentligt hurtigere at producere komponenten. Med traditionel spåntagende bearbejdning tager det 55 timer. Dertil kommer efterbearbejdningen. Med additive manufacturing kan den produceres på 4,5 timer.
Kort produktionstid giver potentielt kort leveringstid, og når komponenten ydermere kan produceres on-demand, behøver Terma ikke have dyrt 15-5PH-stål på lager, hvilket giver et bedre cashflow.
Særdeles høje kvalitetskrav
Komponenten indgår som førnævnt i kampflyet F-35 Lightning II. Med andre ord er kvalitetskravene særdeles høje, og Terma har da også udsat komponenten, der er produceret med additive manufacturing, for omfattende udmattelsestest.
“Resultaterne er lovende, så næste skridt er at gå i dialog med kunden,” (Lockheed Martin, red.) siger Philippe Lovejoy-Courrier.
Komponenten kan blive startskuddet til, at Terma producerer andre komponenter i 15-5PH-stål med additive manufacturing. “Det er udfordrende at bearbejde den type stål. Generelt kan man sige, at laser cladding giver god mening ved hårde metaller og høje materialeomkostninger,” siger Philippe Lovejoy-Courrier.
Storskala 3D-print af støbeforme
Apropos dyre materialer er Terma og FORCE Technology også i gang med andet projekt, som er blevet muligt med den nye Multiprocess Large Scale 3D-printer på Lindø. “Vi ser på, om det kan lade sig gøre at printe støbeforme i højnikkellegeringen Invar. I dag producerer vores underleverandør støbeformene ved at svejse tykke plader sammen for derefter at fræse støbeformene ud. Vi taler om to-tre tons råmateriale pr. støbeform til en kilopris på 200-300 kr., og det er også dyrt i lønomkostninger og tager lang tid. Det ikke er unormalt med et halvt års leveringstid. I stedet kunne det være rart at have en tønde pulver stående på Fyn, så støbeformene kunne produceres hurtigere og billigere,” siger Philippe Lovejoy-Courrier og fortsætter: “Ingen har før printet støbeforme i Invar, så det er innovativt, men også udfordrende, for støbeformene er tre-fire kvadratmeter store.”
Førende i Skandinavien
Philippe Lovejoy-Courrier bringer også et tredje materiale i spil, når han taler om potentialet i 3D-print.
“Stål udgør under én procent i vores produktion. Vi anvender først og fremmest aluminium. Derfor er det interessant for os, at der udvikles højstyrkelegeringer i aluminium på pulverform. Det har ikke været muligt før nu, hvor der er kommet nogle nye pulvertyper, som vi ser på sammen med FORCE Technology. I første omgang vil vi fremstille nogle prøvestænger og trække dem over for at undersøge udmattelsesegenskaberne,” siger Philippe Lovejoy-Courrier.
Dermed fortsætter Terma og FORCE Technology et mangeårigt samarbejde, som han er glad for. “Man er i gode hænder hos FORCE Technology. De har alle de relevante kompetencer i huset, og det tager aldrig lang tid at få en kompetent vurdering – f.eks. hvis vi har lavet en udmattelsestest af et materiale, og ikke forstår resultatet. De er de bedste inden for metallurgi, og ingen andre i Skandinavien mestrer den type additive manufacturing, som vi får lavet på Lindø,” understreger Philippe Lovejoy-Courrier.
Læs mere om historien her