3D print sikrer hurtig produktion af værnemidler under corona-krisen
3D print sikrer hurtig produktion af værnemidler under corona-krisen
Hos AddiFab i Jyllinge fandt man, under Corona-krisen i 2020, en ny anvendelse af 3D print teknologien.
3D print og additive manufacturing er kendt for korte udviklingsforløb, lave opstartsomkostninger og lokal produktion. Egenskaber, der har vist sig at være meget værdifulde i en sundhedskrise, hvor hele verden skulle bruge værnemidler samtidig. 3D print virksomheder i hele verden – også i Danmark – gik i gang med at printe værnemidler, som fx visirer. Dansk AM Hub samlede alle 3D print aktører sådan, at man til myndigheder havde et samlet overblik over printkapaciteten i Danmark. Det overblik og en samlet indgang har vi nu til fremtiden.
Men det er ikke kun med visirer, der blev udviklet og tænkt kreativt. Hos AddiFab gik man, efter italiensk forbillede, i gang med at omdanne en full face snorkelmaske til et værnemiddel mod Covid-19. AddiFab og overlæge Michael Mølmer satte sig for at lave adaptere til snorkelmaskerne, så de kan påmonteres et bakteriespærrende filter.
Efter blot tre ugers udvikling og tests i Danmark er AddiFab nu i gang med selv at producere den nyudviklede filter-adapter, og de første 2.000 stk er bestilt af McGill University Hospital i Canada. Derudover har også er lande som Italien, Spanien, USA, England, Belgien og Sverige udtrykt interesse.
Filter-adapteren, som lyder navnet MiMo, er en ny opfindelse fra overlægen Michael Mølmer, der har set et potentiale i at kunne montere et filter på de allerede tætte snorkelmasker. Maskerne dækker hele ansigtet og filteret i adapteren holder covid-19-virussen ude. Maske, adapter og filter er blandt andet testet af personalet på danske hospitalers corona-afsnit.
Læge Michal Mølmer viser masken frem på billedet.
– Vi står helt klar til rådighed for det danske sundhedsvæsen og er klar til at levere til Danmark. Vi er i dialog med myndighederne og venter på deres reaktion. I mellemtiden hører vi fra mange andre lande, som er interesseret, og derfor er vi allerede i fuld gang med at skrue op for produktionen, siger AddiFabs adm. direktør Lasse G. Staal.
En million masker i USA
Der er ultrakort fra udvikling til produktion, når det er muligt at 3D-printe. Og det vil Lasse G. Staal gerne udnytte i forhold til at hjælpe under corona-krisen.
– Vi valgte at påtage os opgaven med selv at producere, fordi det skulle gå ekstremt hurtigt med at komme i gang. Og MiMo-adapteren er en god løsning, fordi der allerede er rigtigt mange dykkermasker, hvor filteret passer til. Alene i USA er det måske helt op imod en million masker, fortæller Michael Mølmer.
AddiFab forventer at kunne fremstille 500-1000 adaptere om dagen, hvilket kun dækker en meget lille del af det forventede behov.
– Hvis du som udgangspunkt siger, at der er brug for en million adaptere, så forslår vores produktion i Jyllinge som en skrædder en vist varmt sted. AddiFab skal ikke være en flaskehals, så derfor har vi taget næste skridt med vores partner Mitsubishi Chemical, som kan producere markant flere end os. Det vil gøre det muligt at imødekomme den efterspørgsel, vi forventer, siger Lasse G. Staal.
Læs også historien i DI Business: https://www.danskindustri.dk/di-business/arkiv/nyheder/2020/4/danske-varnemidler-efterspurgt-kloden-rundt/
Læs mere om AddiFab og corona initiativet: https://www.addifab.com/addifab-covid19-reponse
Hybrid: 3D print og sprøjtestøbning skaber adapter til snorkelmaske
3D Printing + Injection Molding: COVID-19 Collaboration Scales Up Within A Week
MiMo mask adaptors made using KRAIBURG TM7 MED grade [Image: AddiFab]
Scaling up production to help in the fight against pandemic poses certain challenges — that are increasingly possible to overcome.
Most uses of 3D printing in addressing COVID-19 are quick-response, stop-gap supply chain needs for personal protective equipment (PPE) and other need-it-now goods. It is generally acknowledged that these first response measures are just that: a first response, typically the vanguard of full-scale efforts realized by more traditional mass production manufacturing like injection molding.
A new joint effort, though, is seeing the benefit of 3D printing combined with injection molding to have reached a scale solution in six days.
Read the full story: 3D Printing + Injection Molding: COVID-19 Collaboration Scales Up Within A Week
The New York Times on Danish corona initiative
Danish Charity Network to 3D Print Protective Visors
New York Times March 26, 2020
COPENHAGEN — A group of Danish entrepreneurs have started a charity network that stands ready to make up to 20,000 protective visors a day using 3D printers, in an attempt to meet rising demand from doctors and nurses combating the coronavirus outbreak.
Read the full article in The New York Times
3D Print corona-beredskab
3D Print corona-beredskab
Vi samler et beredskab til at kunne 3D printe emner til hospitaler i forhold til Corona.
I Italien er der blevet fremstillet ventiler til respiratorer til hospitaler i forbindelse med Corona-krisen. I Danmark arbejder det danske 3DP øko-system på at være klar til det, at kunne gøre det samme.
Med 3D print kan man skabe fx ventiler præcist og hurtigt. Dansk AM Hub arbejder på at identificere emner, fx ventiler til respiratorer , som kan blive en mangelvare under corona-krisen til de danske hospitaler. Emner som kan 3D printes, så det kan produceres i en fart i Danmark.
Vi har en stærk branche af AM /3D print-aktører i Danmark, som alle vil hjælpe, men vi mangler konkrete emner, som vi kan begynde at tegne og omsætte til 3D print.
Vi er gået i gang med at kontakte medico-tekniske afdelinger på hospitalerne, men opfordrer også aktører til at kontakte os, hvis de har viden, filer og andet der kan bruges.
Du kan tage skrive til os på info@am-hub.dk eller kontakte Frank Rosengreen Lorenzen på frl@am-hub.dk
Læs mere om det italienske eksempel hos BBC.
Læs også finans.dk: 3D-printede produkter forsøger at komme Danmark til undsætning
Wohlers report 2020
New Wohlers Report 2020 Documents More than 250 Applications of Additive Manufacturing
Fort Collins, Colorado, USA, March 18, 2020—Wohlers Associates, Inc. today announced the publication of Wohlers Report 2020, the 25th annual installment of its undisputed, industry-leading report on additive manufacturing (AM) and 3D printing. Often referred to as the “bible” of 3D printing, the new report provides a unique window into the constantly advancing global industry. The publication provides countless details on AM applications, software, workflows, materials, systems, and post-processing. It gives specifics on patents, startups, investment, and research and development, and the future of AM.
The 380-page report includes a wealth of information on AM industry growth, including more than 250 examples of AM applications in production or development.
Read the danish press release from Teknologisk Institut: Ny rapport viser solid global vækst for 3D-print
In one case, Jabil redesigned an impeller for manufacture by AM. Instead of 73 metal parts assembled by hand, the impeller is made of fiber-reinforced polymer composite in a single part. Fifty impellers can be produced in the time it previously took to make one.
This week, it was announced that Italian firm Isinnova had designed and produced many respirator valves in under two days. The effort was in response to an urgent call for help from a hospital in northern Italy that was overwhelmed with COVID-19 patients. Ten patients were able to breathe with the aid of a machine that included the 3D-printed valve.
The era has begun where the users of AM are in the driver’s seat, pushing boundaries of what AM can achieve in production applications. System manufacturers, service providers, and producers of materials are responding with offerings to match.
Wohlers Report 2020 builds upon input from a record ensemble of 129 service providers, 114 manufacturers of industrial AM systems, and 40 producers of third-party materials and desktop 3D printers. The report documents government-sponsored research and development, collaborations and consortia, and the activities of 139 academic and research institutes around the world. Seventy-nine co-authors and contributors in 33 countries provided expert views and opinions in the report.
New and expanded features of the 2020 edition include:
- Maturing and emerging applications of AM for series production
- Review of AM in the dental industry
- Commentary on 77 early-stage investments valued at $1.1 billion
- Compilation of 72 industry partnerships from the past 12 months
- Expert reports from 35 countries
- Tables of systems, third-party materials, software tools, and emerging technologies
The 380-page Wohlers Report 2020 includes 42 charts and graphs, 168 tables, and 377 images and illustrations. It also includes more than 145 pages of supplemental online content available exclusively to the buyers of the report. More information on the new report is available here.
About Wohlers Associates, Inc.
The company offers an unparalleled window into AM and 3D printing. The independent consulting firm of 33 years provides technical, market, and strategic advice on the new developments and trends in rapid product development and AM. Wohlers Associates counts 275 organizations in 27 countries among its clients. Separately, the company has provided advice to more than 180 investors.
Plus Pack: Fra ide til forretning på seks måneder
Fra ide til forretning på under seks måneder
Det startede med et spørgsmål på et strategiforløb hos ledelsen i Plus Pack. ”Hvad sker der med 3D print. Er der noget her, vi går glip af”. Og det spørgsmål blev startskuddet til at komme med på Dansk AM Hubs AM Generatorforløb, som primært består af to workshops, hvor man arbejder med egne ideer til, hvor 3D print kan bruges i forretningen. Plus Packs ide gik på at forsøge at lave prototyper på en nemmere måde ved hjælp af 3D printede komponenter til presseværktøj.
”Vi vil gerne lave skræddersyede emballageløsninger, og det kræver en tæt dialog med kunden. Det kan vi have, når vi kommer med en realistisk prototype udover en tegning og 2D model, siger Bastian Fietje, Manager of Group Projects, Plus Pack.
Plus Pack har eksperimenteret med at 3D printe værktøjskomponenter i nylon, som i dag laves i stål. Det giver mulighed for en iterativ udviklingsproces, hvor Plus Pack hurtigere kan producere realistiske prototyper af aluminiumsbakker, som kunden kan teste og evaluerer. Før foregik udviklingen ofte ud fra tegninger og 2D modeller, og når Plus Pack skulle i gang med at producere aluminiumsbakken, så måtte de bestille de dyre værktøjskomponenter i stål.
Det specialdesignede værktøj til fx bunden af en foliebakke kan printes på et par dage og kræver en dags efterbehandling, hvilket står i kontrast til at vente 12-15 uger på værktøjskomponenterne i stål, som samtidig ikke giver mulighed for nye tilpasninger.
”Det giver et helt andet samarbejde med kunden i forhold til at skræddersy deres produkter”, fortæller Bastian Fietje.
På en konkret opgave fik Plus Pack hurtigt brug for at kunne lave en prototype til en ny kunde. En fransk snegleproducent havde et behov for en aluminiumsbakke, med fordybninger i bunden, så sneglene ikke rutsjer rundt. Plus Pack lykkedes med at 3D printe et nyt bunddesign og derved lave en skræddersyet bund til sneglene. Det tog en uges tid at designe, 3D printe og producere prototypen, og kunden kunne derved lynhurtigt give feedback på bakkens design og funktionalitet.
Bastian Fietje beskriver værdien i organisationen som to-foldig. Dels har brugen af 3D print en stor værdi internt i organisationen, fordi de har kunnet re-tænke den måde de designer produkter på. Der er ting, man kan teste, og 3D print rykker ved forestillingen om, hvad der er muligt.
Herudover har det stor værdi for deres kunder. ”Vi kommer med en rigtig bakke som prototype, så de kan prøve den af, og se hvordan emballagen opfører sig, når den bliver brugt”, fortæller Bastian Fietje.
3D print har helt klart fået en plads hos Plus Pack, og Bastians opfordring til andre virksomheder er da også klar: ”Det er bare med at komme i gang. Brug 3D print til at forsøge og eksperimentere. Ellers finder man ikke de gode muligheder” slutter han.
Om Plus Pack
Plus Pack er en international og innovativ virksomhed med hovedkontor i Danmark og med produktion i såvel Danmark (Odense) som i Belgien (Genk). Plus Pack er en familieejet virksomhed med rødder tilbage til 1914, og virksomheden drives i dag af 4. generation i Haustrup-familien. Plus Pack er specialiseret i udvikling og produktion af emballage-løsninger til fødevareindustrien og er i dag en af Europas førende virksomheder indenfor fremstilling af aluminium- og plastemballage med salg til 50 forskellige lande. Plus Pack har 220 medarbejdere, virksomheden vækster og er midt i en spændende udvikling med udgangspunkt i løftet ”We make food stand out”.
Mikkel Huse Studio
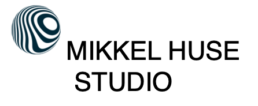
Mikkel Huse Studio er en designvirksomhed, som har anvender traditionelt 3D print til at lave fysiske modeller af deres designs. Med FIM har de fået mulighed for at lave modeller, som også har det ægte materiale, produktet til sidst skal fremstilles i.
Baggrunden for arbejdet i AM HYBRID startede for 8 år siden i Præstø. Den tragiske historie om de 13 elever og 2 lærere fra Lundby Efterskole der sejlede i en tur i Præstø Fjord i februar måned og kæntrede er velkendt. 7 af eleverne blev umiddelbart lagt i koma og én af lærerne omkom.
Da personerne blev hentet op ad vandet blev de behandlet for hypotermi – alvorlig nedkøling af kroppen. Det skete ved at tappe deres blod, varme det op, og dernæst føre blodet ind i kroppen igen. Dette er omstændig proces.
Den læge der foretog behandlingen, speciallæge Claus Lie, er én af bagmændene bag en ny opfindelse, der vil gøre behandling af hypotermi lettere og hurtigere. Claus Lie, som også er medstifter af virksomheden HeathCath kontaktede Mikkel Huse Studio for at bede om hjælp med designet.
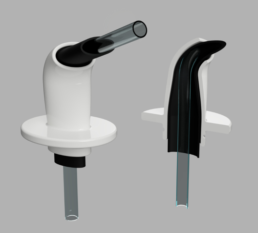
Systemet er mere skånsomt og desuden langt mere mobilt end de teknikker, man benytter i dag, og behandlingen kan simpelthen påbegyndes tidligere end det er muligt i dag
– Speciallæge Claus Lie
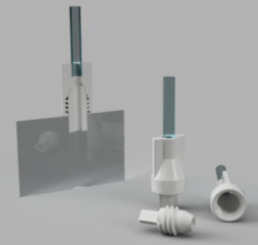
I AM HYBRID har Mikkel Huse Studio fået hjælp til at teste designs af gennem FIM. Det har hjulpet i processen i udvælgelse af dét design der har de optimale produktegenskaber. Produkterne, som er indføringskateteret og en luer lock fitting mellem vandslange og varmepose, blev fremstillet i polypropylen.
Kombinationen af 3D-print og sprøjtestøbning har gjort det muligt for os at få lavet ægte fysiske modeller af vores design som er i det materiale, produkterne skal produceres i. Det gør det muligt at sikre sig, at et bestemt design er det rigtige, inden en egentlig produktion sættes op
– Mikkel Huse, ejer af Mikkel Huse Studio
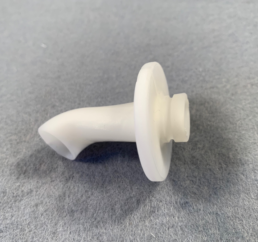
Daniamant
Daniamant
Virksomheden Daniamant er en af de store aktører på markedet for udvikling, produktion og salg af sikkerhedsudstyr til redningsveste og redningskranse til søfartindustrien. Daniamant er som så mange andre virksomheder interesserede i at optimere deres produkter, så der kommer det rette optimum mellem kvalitet og pris. Et af de produkter, som Daniamant identificerede havde et optimeringspotentiale, var en af deres redningslysholdere. Den pågældende holder består i dag af 2 komponenter, som samles efter de er blevet støbt. Det er både en fordyrende proces, samtidig med at den ekstra håndtering og samleproces øger risikoen for produktionsfejl.
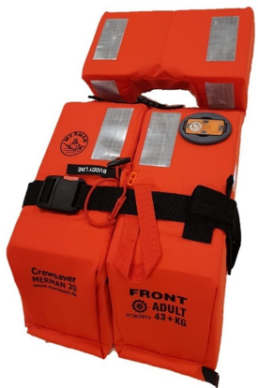
Daniamant gik i samarbejde med J. Krebs & Co i gang med at lave forskellige løsningsforslag til designs, som kunne eliminere samleprocessen og stadig opfylde formålet med produktet – holde redningslyset fast i redningsvesten. Efter flere iterationer på designet, blev et overordnet design udvalgt til test. Man valgte at benytte Freeform Injection Molding til at lave prototyperne, for på en hurtig og kosteffektiv måde at lave prøver på produktet, som kunne testes, men de rigtige materialeegenskaber (samme plastmateriale og samme produktionsproces). Der blev desuden lavet nogle modificerede emner, som kun bruges til at lave trækprøvetests – her tog man de specifikke detaljer fra plastemnet, som skulle være en del af testen og koblede dem med en løsning, hvor man havde noget at gribe i.
Resultatet af træktesten endte med at påvise, at den nye designløsning kunne modstå omtrent 600 N, hvilket var mere end det dobbelte af den nuværende redningslysholder der kan modstå en belastning på 250 N.
Det har været en stor fordel i designprocessen at man løbende har kunne teste kvaliteten af designet i forhold til produktkravene. Den helt store fordel er at Daniamants kunder har kunne få verificeret at det nye design bliver stærkere end det hidtidige og samtidig får reduceret risikoen for produktionsfejl.
De potentielle besparelser i værktøjsændringer har været massive, både i kroner og i tid
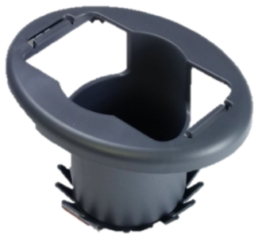
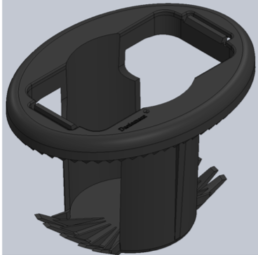
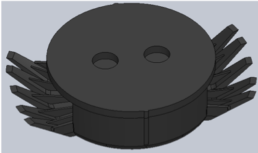
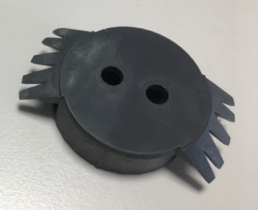
AM Hybrid
AM Hybrid
Hybridfremstilling gennem 3D print og nye kollaborative samarbejdsformer
I AM Hybrid projektet vil Teknologisk Institut, på vegne af Dansk AM Hub, gennem et antal virksomhedscases demonstrere værdien ved at implementere 3D print i deres produktudviklingsfase. 3D printteknologien oplever en rivende udvikling, men der er stadig et stykke vej til, at den er blevet veletableret i danske virksomheder.
En stor værdi ved 3D print opleves i en virksomheds produktudviklingsfase. Når den bruger 3D print har den mulighed for hurtigt at fremstille et emne, der kan testes på forskellig vis. Dette giver feedback til virksomhedens produktdesignansvarlige, som kan komme med ændringer til en ny prototype. Samlet set sparer denne proces tid og penge.
I AM Hybrid projektet er fokus på, at lave støbeforme i 3D print. Emnerne støbes i formen, hvorefter den opløses.
Se hvordan J.Krebs & co. har kombineret 3D print og sprøjtestøbning.
AM Hybrid cases
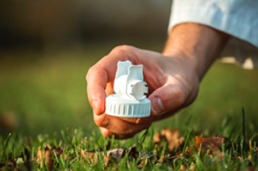
På verdensplan mangler over 800 millioner mennesker adgang til rent drikkevand og det problem vil iværksættervirksomheden SolarSack være med til at løse. Virksomheden har udviklet en vandbeholder i plastik, som kan fyldes med fire liter vand og placeres i solen i fire timer. I AM HYBRID har de anvendt 3D-printede sprøjtestøbeforme til at optimere produktets design.
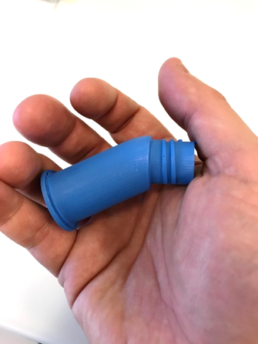
BlueTipTools har udviklet et par fugedyser, som gennem optimering af den geometriske udformning af konventionelle lige dyser kombineret med en unik plastblend, har lavet dyser, som er bedre end det der ellers findes på markedet.
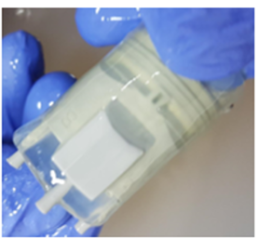
Krebs & Co. er en virksomhed i Skævinge, Nordsjælland, som har været i sprøjtestøbebranchen siden 1956. I dag er virksomheden to-benet. Dels sprøjteblæser og sprøjtestøber de, som de har gjort i mange år. For nylig har de investeret i 3D-print og Freeform Injection Molding.
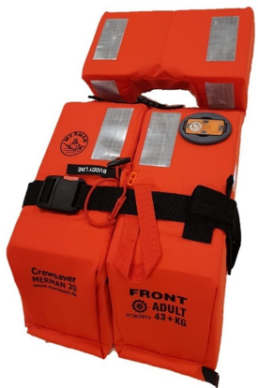
Et af de produkter, som Daniamant identificerede havde et optimeringspotentiale, var en af deres redningslysholdere. Den pågældende holder består i dag af 2 komponenter, som samles efter de er blevet støbt. Det er både en fordyrende proces, samtidig med at den ekstra håndtering og samleproces øger risikoen for produktionsfejl.
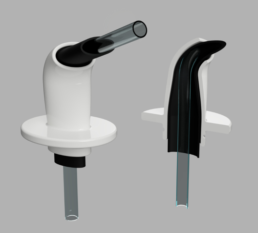
Baggrunden for arbejdet i AM HYBRID startede for 8 år siden i Præstø. Den tragiske historie om de 13 elever og 2 lærere fra Lundby Efterskole der sejlede i en tur i Præstø Fjord i februar måned og kæntrede er velkendt. 7 af eleverne blev umiddelbart lagt i koma og én af lærerne omkom.
BlueTipTools
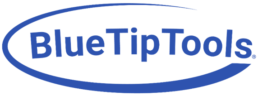
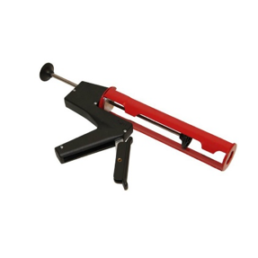
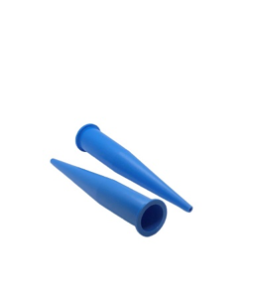
BlueTipTools er en opstartsvirksomhed der fokuserer på at udvikle, fremstille og distribuere kvalitetsprodukter til fugebranchen. Givet virksomhedsejerens mangeårige erfaring med fugebranchen er ønsket at lave høj-kvalitetsprodukter der er rettet mod det professionelle marked inden for fugearbejde.
BlueTipTools har udviklet et par fugedyser, som gennem optimering af den geometriske udformning af konventionelle lige dyser kombineret med en unik plastblend, har lavet dyser, som er bedre end det der ellers findes på markedet. Det næste skridt i den udvikling er at lave fugedyser, som rammer nogle af de mere specielle behov, som opstår i forbindelse med fugearbejde. For at minimere tidsforbruget i udviklingsfasen og begrænse omkostninger til værktøjsændringer har BlueTipTools benyttet Freeform Injection Molding til at lave nogle af de tidlige design og funktionsoplæg – for hurtigere at komme frem til det design der bruges til de endelige produktdesign til at lave værktøj ud fra.
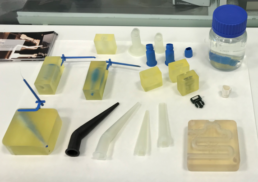
BlueTipTools har behov for at lave en hel portefølje af produktvarianter, så de på sigt kan servicere deres kunder endnu bedre end de kan i dag – og da der er behov for at nytænke den måde værktøjet til fugebranchen er designet. Det er en kæmpe opgave for en opstartsvirksomhed, men Freeform Injection Molding muliggør at de hurtigere kommer frem til de rigtige designs, samtidig med at de minimerer risikoen for fejlbehæftede værktøjsinvesteringer. Det giver samtidig mulighed for at prøve nogle løsninger af, som er mere dristige end hvad man normalt tillader sig og samtidig kan der gennemføres løsninger, som værktøjsteknisk er voldsomt komplicerede, men relativt fornuftigt kan laves med Freeform Injection Molding.
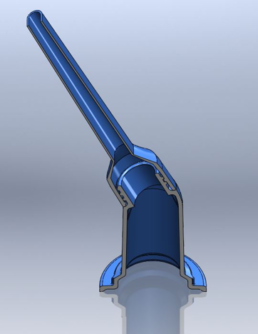
I AM HYBRID har BlueTipTools fået hjælp til at udvikle en såkaldt knækdyse via FIM. Inden investering i en sprøjtestøbeform til masseproduktion fik de lavet prototyper i forskellige designs i de materialer, dysen skulle have, når det blev markedsført. På denne måde har virksomheden kunne teste idéer af og sikre sig, at løsningen kunne holde i praksis.
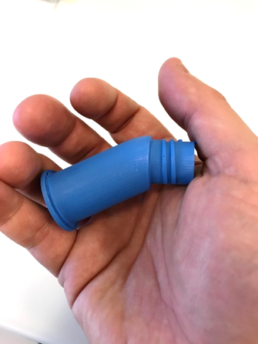