Daniamant
Virksomheden Daniamant er en af de store aktører på markedet for udvikling, produktion og salg af sikkerhedsudstyr til redningsveste og redningskranse til søfartindustrien. Daniamant er som så mange andre virksomheder interesserede i at optimere deres produkter, så der kommer det rette optimum mellem kvalitet og pris. Et af de produkter, som Daniamant identificerede havde et optimeringspotentiale, var en af deres redningslysholdere. Den pågældende holder består i dag af 2 komponenter, som samles efter de er blevet støbt. Det er både en fordyrende proces, samtidig med at den ekstra håndtering og samleproces øger risikoen for produktionsfejl.
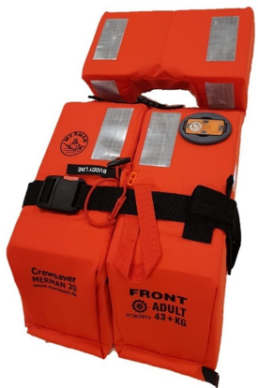
Daniamant gik i samarbejde med J. Krebs & Co i gang med at lave forskellige løsningsforslag til designs, som kunne eliminere samleprocessen og stadig opfylde formålet med produktet – holde redningslyset fast i redningsvesten. Efter flere iterationer på designet, blev et overordnet design udvalgt til test. Man valgte at benytte Freeform Injection Molding til at lave prototyperne, for på en hurtig og kosteffektiv måde at lave prøver på produktet, som kunne testes, men de rigtige materialeegenskaber (samme plastmateriale og samme produktionsproces). Der blev desuden lavet nogle modificerede emner, som kun bruges til at lave trækprøvetests – her tog man de specifikke detaljer fra plastemnet, som skulle være en del af testen og koblede dem med en løsning, hvor man havde noget at gribe i.
Resultatet af træktesten endte med at påvise, at den nye designløsning kunne modstå omtrent 600 N, hvilket var mere end det dobbelte af den nuværende redningslysholder der kan modstå en belastning på 250 N.
Det har været en stor fordel i designprocessen at man løbende har kunne teste kvaliteten af designet i forhold til produktkravene. Den helt store fordel er at Daniamants kunder har kunne få verificeret at det nye design bliver stærkere end det hidtidige og samtidig får reduceret risikoen for produktionsfejl.
De potentielle besparelser i værktøjsændringer har været massive, både i kroner og i tid
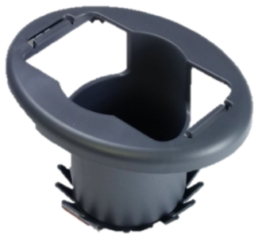
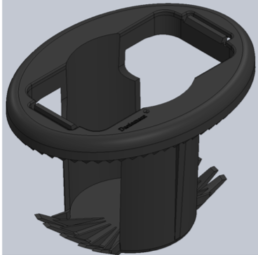
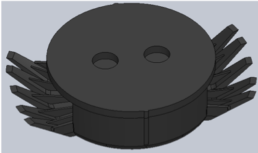
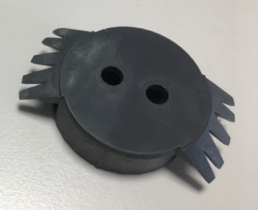
Related Posts
05/03/2025
3DCP sætter betonprint på skoleskemaet sammen med Herningsholm Erhvervsskole
I et undervisningsforløb mellem 3DCP…
18/11/2024
PERFI Prints a Hearing Aid in Seconds – Could Transform the Entire Industry
The startup company won a pitch…
19/09/2024
Derfor er industriel 3D-print en gevinst for historisk byggeri
Matteo Baldassari fra virksomheden…
12/12/2023
Redesignet kølesystem laver varmt vand til fjernvarmen
Heatflow, som laver kølesystemer til…
12/06/2023
Kan man designe en væg med mindre materiale og samme bæreevne?
Apex Wall er et bemærkelsesværdigt…
20/03/2023
Prototal Damvig cases: Højere kvalitet, funktionalitet og reduceret time to market
Prototal Damvig har på det seneste…
05/01/2023
Med AM-teknologi vil Wohn bygge billige og mere bæredygtige Tiny Houses
WOHN er en dansk startup med en vision…
27/12/2021
SEJMA Industries bekæmper klimaproblemer med 3D teknologi
SEJMA Industries har i 3DP Try Out…
20/12/2021
3D print løfter produktion, sikkerhed og service for DANILIFT
DANILIFT har deltaget i Dansk AM Hubs…
15/12/2021
Fra uger til timer: 3D print optimerer SIK Tekniks produktudvikling
SIK Teknik har stort fokus på…
08/12/2021
ChromaViso sparer lysår på fremstilling af prototyper
I 3DP Try-Out forløbet lånte ChromaViso…
18/03/2021
Med disruptiv teknologi forbedrer EYE-GO øjenpatienters vilkår
Ved at kombinere AM og sprøjtestøbning…
18/03/2021
FIM-teknologi forbedrer Quforas kontinens hjælpemiddel
FIM-teknologi har hjulpet Qufora A/S i…
18/03/2021
Carmo A/S kombinerer AM og sprøjtestøbning og finder frem til en game changer
Kombinationen af AM og sprøjtestøbning…
18/03/2021
3D print og FIM-teknologi bringer Spraino videre med sin produktudvikling
Sprainos produkt taler til…
11/03/2021
Den 3D printede opfindelse ‘Quickfact’ forbedrer prøvetagninger på hospital
Sjællands Universitetshospitalet har…
26/08/2020
3D print har skåret otte uger af DAFAs udviklingstid på nye produkter
3D print har skåret otte uger af DAFAs…
25/06/2020
3D print puster liv i udviklingsprojekter hos brændeovns-producenten
I starten af 2020 ankommer Dansk AM Hub…
02/03/2020
Freeform Injection Molding i små-skalaproduktion vinder frem
Gennem AM Hybrid har J. Krebs og Co.…
02/03/2020
Silkeborg Stigefabrik – prototyping: Fra fire uger til fire dage
Ved brug af 3D teknologi har HYTOR både…
02/03/2020
Med 3D print får vi langt mindre spild i designprocessen
Hos møbelvirksomheden NORR11 er det…
02/03/2020
Med 3D print kan vi langt bedre supportere innovative startup-virksomheder
Siden 1940’erne har danske Carmo…