AM Sustain
AM Sustain
I videoen foroven kan du høre mere om vores Innovationsprogram for små og mellemstore virksomheder, AM Sustain, som skal udvikle bæredygtige løsninger med afsæt i 3D print og additive manufacturing. AM Sustain implementeres i samarbejde med Deloitte og kombinerer 3D prints store forretningspotentiale med Verdensmålenes (Sustainable Development Goals) strategiske fokus på fremtidens markedsbehov.
Igennem AM Sustain programmet får de deltagende virksomheder en solid metode til at udvikle og accelerere bæredygtige forretningsløsninger, der tager afsæt i AM-teknologi og 3D-print, og med potentiale til at drive vækst, konkurrenceevne og reduktion af omkostninger.
Kontakt
Ønsker du at deltage eller høre mere om AM Sustain kan du kontakte Lars Holmegaard, Projekt og Udviklingschef i Dansk AM Hub, lh@am-hub.dk
3DP Try out Linatech
3DP Try Out casehistorie: Linatech
Fra første print til kunde på under en måned
Linatech har i en måned lånt en 3D printer af Dansk AM hub og Center for Industri. De har printet elementer til deres blodprøve transportsystem. Blodprøver tranporteres i traditionelle reagensglas via et rørsystem direkte til laboratoriet. Da Linatech fik AM-teknologien ind i huset på forsøgsbasis skulle de finde ud af, hvad den kunne bruges til.
Martin Jerga, der er projektleder, fik lov til at eksperimentere med den nye maskine. Og den har kørt næsten uafbrudt i den måned, de havde den. Til blodprøve transportsystemet har Linatech erstattet flere elementer, herunder nogle ’skuffer’ som blodprøverne lander i. Normalt produceres de i stål. Med additiv manufacturing/3D print har Linatech designet skufferne i plastic på stedet og med en struktur, der betyder, at blodprøverne ikke lander forkert og i øvrigt bliver i den skuffe, de skal være i.
”Det, vi har lavet med 3D print ville man ikke kunne lave i stål”, fortæller Martin Jerga og forsætter: ”De 3D printede elementer gør det muligt at transportere blodprøverne/prøveglas uden at ødelægge dem, fordi det er designet med speciel struktur”.
Første bekendtskab med 3D print
Den lånte printer fra Dansk AM Hub er Linatechs første bekendtskab med 3D printere i huset, men det bliver næppe det sidste.
”Det har været meget givtigt til det pågældende projekt at forsøge os med 3D print. Det er hurtigt at komme i gang. Vi startede med at lave et print, hvor prøver landende forkert. Men så printede vi bare 27 ny emner. Det tog en dag – i stedet for en uge, som det havde taget hvis vi skulle have haft det fra en underleverandør”, fortæller Martin Jerga.
Projektet her har givet Linatech mulighed for at forbedre deres udviklingstid. Blodprøvemaskinen med de 3D printede elementer er allerede sendt ud til test hos kunden, og Linatech vil nu gå i gang med at regne på deres businesscase og finde ud hvordan de i fremtiden skal bruge 3D print.
Om Linatech
Linatech har igennem mange år udviklet og produceret håndterings- og produktionsudstyr til vindmøllebranchen og blandt andet medicinalbranchen. Linatech beskæftiger i dag 60 medarbejdere fordelt på to afdelinger i Vium og Thorning.
Virksomheden råder derfor i dag over 7500 m² produktions-, lager- og administrationsbygninger. Linatech samarbejder med virksomheder i så forskellige brancher som plast-, pap-, isolerings-, medico– og vindmølleindustrien Linatechs kompetencer spænder over flere forretningsområder:
- Engineering og Udviklingsprojekter
- Specialmaskiner
- Underleverandørarbejde
- Automation
- Montage
- Service
SDG Super Heroes
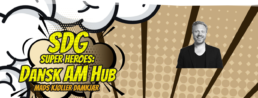
Dansk AM Hub er nomineret til SDG Tech Awards Denmark, der afholdes d. 6. juni i København af Sustainary. Vi er, udover at være rigtig glade for nomineringen, ydermere glade for et fokus på en bæredygtig verden og ikke mindst, hvordan vi når dertil.
Læs mere om eventet her.
Sustainary har hertil introduceret SDG Super Heroes serien, hvor individer, NGO’er eller virksomheder hyldes for at integrere verdensmålene ind i deres kernekompetencer og dermed bidrage til at nå FN’s 17 verdensmål for en bæredygtig udvikling.
Læs om Dansk AM Hub som superhelt her.
3D-printet raketbrændkammer i aluminium
3D-printet raketbrændkammer i aluminium
I samarbejde med studerende fra det danske DanSTAR-projekt, har Teknologisk Institut 3D-printet et raketbrændkammer i aluminium til den raket, som skal deltage i den internationale Spaceport America Cup i New Mexico i sommeren 2019. 3D-print var den oplagte løsning til brændkammeret, da det består af nogle meget komplekse indvendige geometrier, som nærmest er umulige at opnå med andre produktionsteknologier.
Samarbejdet om brændkammeret startede tilbage i sommeren 2018, hvor de studerende på DanSTAR-projektet tog fat i Teknologisk Institut, fordi de i samarbejde med industrielle samarbejdspartnere skulle bygge en raket til deltagelse i Spaceport America Cup – og her var 3D-print i metal en oplagt løsning til rakettens brændkammer. Det blev derfor aftalt, at DanSTAR skulle designe brændkammeret specifikt til at blive lavet i 3D-print, således at projektet fra start udnyttede de muligheder, der ligger i 3D-printteknologien. Resultatet blev et brændkammer i aluminium, som er designet med avancerede kølekanaler, der udelukkende kan laves i 3D-print.
– Vi har længe kendt til 3D-print i metal og vidst, at det var en mulighed. Men at få lov til at arbejde med processen åbner selvfølgelig for nogle nye muligheder, hvor man som studerende i højere grad begynder at overveje 3D-print til fremtidige projekter, da det er en genial måde at fremstille ekstremt komplekse geometrier eller prototyper på, siger Rasmus Arnt Pedersen, som er formand for DanSTAR.
Løbende sparring på design
Første del af opgaven med at 3D-printe et raketbrændkammer i aluminium var at nå frem til det helt rigtige design, og her har der været en løbende dialog, hvor 3D-printeksperterne fra Teknologisk Institut har givet sparring og feedback på DanSTARs designfiler med henblik på at nå frem til det bedste resultat, som passer til rakettens kravspecifikationer, og som samtidig er muligt at printe. Det resulterede undervejs i nogle designjusteringer – fx i højden, som måtte reduceres en smule for at passe i printerens byggekammer, samt i det ydre design med henblik på at kunne få restpulver ud af brændkammerets indvendige kølekanaler.
– Vi har løbende sparret med Teknologisk Institut under designprocessen, for der undervises ikke i design med henblik på additiv fremstilling på DTU, og selvom vi har stort kendskab til FDM-plastikprintere, er det alligevel en anden sag, når det er metalprint. Derfor har det været nødvendigt at blive hjulpet lidt på vej, men det har været en stor fornøjelse, og vi er endt med en state-of-the-art raketmotor, som kun de færreste raketklubber ville turde drømme om, fortæller Rasmus Arnt Pedersen.
Netop opgaven med at få restpulver ud af brændkammerets indvendige geometrier efter selve printprocessen var en af de mere spændende udfordringer for Teknologisk Instituts 3D-printeksperter, og den gav værdifuld læring til fremtiden – og et par grå hår undervejs.
– Vi endte med en funktionsmæssig løsning med små adgangspunkter til at få restpulveret ud. De er samtidig designet, så de giver DanSTAR mulighed for at sætte termofølere på brændkammeret og få driftsdata under test. Tillige er de konstrueret så adgangspunkterne kan forsegles med specialdesignede propper, når raketten skal flyve, fortæller Kristian Rand Henriksen fra Teknologisk Institut, som designede løsningen.
Intelligent brug af aluminium
I udviklingen af raketbrændkammeret har et væsentligt fokus været at holde vægten nede, da det betyder, at der skal bruges mindre energi på at løfte raketten fra jorden. Netop her kommer 3D-print til sin ret, fordi teknologien gør det muligt at bygge i lettere materialer pga. et design, hvor man køler brændkammeret samtidig med at forbrændingen finder sted – i stedet for at vælge et tungere materiale som fx kobber, der absorberer en masse varme, har man således kunnet bygge i aluminium, som er lettere.
Kølingen er nødvendig, da forbrændingen i kammeret sker ved meget høj temperatur – helt op til 3.200 °C – og meget få materialer kan holde til den temperatur, endsige bevare deres styrke. Når Teknologisk Institut og DanSTAR har valgt at 3D-printe brændkammeret i aluminium, som egentlig smelter ved meget lavere temperatur, er det fordi kammeret køles aktivt. Det er en tilgang, som er velkendt inden for rumfart, og samtidig har DanSTAR lavet et design, som virkelig udnytter mulighederne inden for 3D-print.
– Den raketmotor vi har lavet i samarbejde med Teknologisk Institut kunne ganske enkelt ikke produceres med konventionel produktion. Motoren er regenerativt kølet, hvilket vil sige at vi cirkulerer brændstoffet inde i væggen på motoren gennem en lang spiral. Denne motortype er mest anvendt i moderne raketmotordesign, men den er enormt kompliceret at producere, fordi man er nødt til at finde en måde at få kølemidlet ført ind i væggen. Men med 3D-print er den største udfordring snarere at designe en løsning – ikke at producere den, fortæller Rasmus Arnt Pedersen.
Forbrændingen i kammeret kører på tokomponent brændstof – NO2(eller lattergas) og isopropyl alkohol – og ved den regenerative køling køres den ene brændstofkomponent gennem en spiral, der løber indvendigt i brændkammeret. Det har den dobbelte effekt, at brændkammeret køles, så temperaturen holdes nede på et niveau, hvor kammeret ikke smelter og stadig har strukturel styrke, og samtidig varmes brændstoffet op, så der er mindre energitab, når det skal forbrændes – på den måde øges effektiviteten af forbrændingen.
Nye byggerekorder på Teknologisk Institut
For Teknologisk Institut har det været en spændende opgave at 3D-printe brændkammeret – både fordi det er designet med nogle komplicerede og skjulte indvendige geometrier, som ikke kan fremstilles på anden vis, men også fordi det stillede nogle udfordringer i forhold til byggestørrelse og kammerstørrelse, da der både blev bygget højt og helt til kanten af printkammeret.
– Dette er faktisk det højeste byg, vi indtil nu har lavet i metal, og det jo altid spændende at flytte grænserne, så vi får en bedre idé om, hvad vi kan i fremtiden. Og så er det jo spændende at arbejde sammen med engagerede mennesker, der kommer med ny viden og nye ideer, og brændkammeret har været et godt eksempel på, hvordan man kan komme uden om traditionelle begrænsninger, når man udnytter mulighederne ved 3D-print, fortæller Nikolaj Kjelgaard Vedel-Smith, der som konsulent på Teknologisk Institut har haft det direkte samarbejde med DanSTAR.
Om DanSTAR:
DanSTAR er et studenterdrevet projekt, hvor studerende fra DTU og Maskinmesterskolen i København samarbejder med industrielle partnere om at designe og udvikle en raket, der i sommeren 2019 skal deltage i SpacePort America Cup i New Mexico, USA i konkurrence med studerende fra hele verden.
DanSTAR raketten, der er 3,5 meter høj, skal flyve op i 9 kilometers højde, og den bærer 18 kg brændstof. Under opsendelsen er trykket i det 3D-printede aluminiumsbrændkammer på 20 bar, og brændstofblandingen skal brænde i 13 sekunder ved temperaturer op til ca. 3.200 °C.
3D-print er i øvrigt ved at blive mere og mere udbredt inden for rumfartsindustrien, fordi det er den bedste måde at løse udfordringerne med komplekse geometrier, og fx bruges 3D-print også af Elon Musks SpaceX og engelske Orbex, der også har kontor i Danmark
SDG Tech Awards 2019
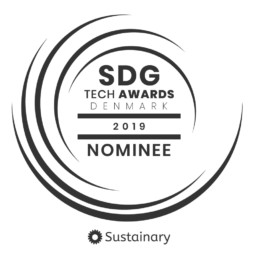
Den 6. juni afholdes SDG Tech Award Festival i København – og Dansk AM Hub er nomineret. Det er vi rigtig glade for og hvor er det fedt med fokus på, at en mere bæredygtig verden er mulig – og på hvilke teknologier, der bidrager til det. Vi er spændte på at følge alle kandidaterne, der arbejder med teknologi og bæredygtige løsninger.
Plastteknik Nordic 2019
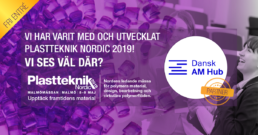
Plastteknik Nordic den 8.-9. maj i Malmø
Kom med når der er fokus på Plastteknik den 8.-9. maj i Malmø.
Du kan møde Dansk AM Hub, som er på partner på konferencen på 3D halvdagsseminaret den 8. maj kl. 13.00-16.00.
Grafisk Designpraktikant til Dansk AM Hub
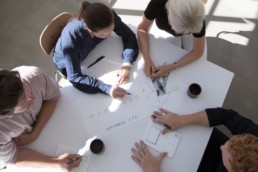
Grafisk Designpraktikant til Dansk AM Hub
Vil du være med til at udbrede kendskabet til nye teknologier, bæredygtighed og 3D print i Danmark?
Vi søger en designpraktikant, der, sammen med resten af teamet, skal udbrede kendskabet til 3D print og skabe grafisk indhold til web, sociale medier, bøger og andet trykt materiale.
Vi søger en grafisk/digital designpraktikant, der har lyst til at udfordre sig selv og med grafisk materiale til både web og print, og har lyst til at formidle kompliceret stof. Du vil få en bred erfaring med at designe og skabe grafiske elementer til alle vores platforme, og du vil stå tilbage med konkret materiale til portfolio. Du vil komme til at have dialog med vores kreative samarbejdspartnere som bl.a. Urgent Agency, Stupid Studio og VICE, m.fl.
Arbejdsopgaver
- Designe grafik og elementer til vores website
- Hjælpe med eventuelle nye websites til nye initiativer
- Billedbehandling og info-graphics
- Opsætning af booklets, tools og andet materiale til tryk, bla. vores bøger
- Opsætning af plakater m.m. til events, workshops og konferencer
- Input og storyboards til film og video
- Bestilling af tryksager m.m.
- Understøtte vores kommunikationsteam
- Hjælpe til generelt i Dansk AM Hub på linje med de resterende medarbejdere
Vi forventer, at du er vant til at bruge Adobe Photoshop, illustrator og InDesign, som vi giver adgang til.
Om Dansk AM Hub
Dansk AM Hub er en filantropisk fond og Danmarks nationale samlingspunkt for 3D print og additive manufacturing. Vi holder til i Kapselfabrikken i Valby.
Læs mere om hvem vi er, og hvad vi laver på am-hub.dk.
Kontakt:
Hvis du er interesseret i et praktikophold hos os, så send din ansøgning og CV til info@am-hub.dk
Praktikopholdet er ulønnet.
Klar til 3D print
Klar til 3D print?
Dansk AM Hub tilbyder i samarbejde med Autodesk virksomheder et værktøj til at vurdere hvor parat organisationen er til nye teknologier, som additive manufacturing og 3D print.
Værktøjet er nemt at bruge og måler hvor virksomheden står i forhold til fem områder, der kan være med til at forandre den mådevirksomheder designer, producerer og sælger deres produkter på.
“Værktøjet giver en personligt tilpasset rapport over din organisations kapacitet og giver et overblik over den bedste kombination af additive manufacturing /3D print og traditionel fremstilling, sammen med viden om, hvor du skal fokusere, når nye teknologier skal bringes i spil “, siger Mads Kjøller Damkjær, CEO, Dansk AM Hub.
Alle fremstillingsvirksomheder kan bruge værktøjet, hvis de ønsker at komme i gang på AM, eller udvide brugen, finde nye forretningsmodeller eller bare for at kickstart et nyt mindset om digitalisering i organisationen.
”I Dansk AM Hub laver vi mange aktiviteter målrettet virksomheder, der ønsker at komme i gang med 3D print, som er i gang og ønsker at udvide eller blot går med nogle ideer, hvor 3D print kan spille ind. Derfor ved vi, at der er et behov for at få viden om teknologien, men i høj grad også et behov for at arbejde med, hvordan det passer ind i virksomhederne. Her ser vi dette værktøj som et muligt første skridt”, fortæller Mads Kjøller Damkjær.
“Vi er glade for at samarbejde med Dansk AM Hub og for at se en stigning i interessen for AM-teknologi fra det danske marked og virksomheder “, siger Asif Moghal, Senior Industry Manager, Autodesk.
Fakta om vurderingsværktøjet
– Find vurderingsværktøjet her: https://fomt.autodesk.co.uk/en_eu/tool/future-of-making-things-en_eu/partner/dansk-am-hub/
– Test din parathed til at implementere 3D print i virksomheden.
– Find de primære områder, hvor du skal gøre en indsats for at tilpasse din virksomhed til nye teknologier.
Om Dansk AM Hub
Dansk AM Hub er Danmarks nationale samlingspunkt for Additive Manufacturing. Vores mål er at styrke dansk erhvervslivs konkurrenceevne ved at fremme brugen af Additive Manufacturing og 3D print. Vores fokus er på små og mellemstore virksomheder og udvikling af nye forretningsmodeller, som kan føre til vækst, innovation og bæredygtige løsninger.
Dansk AM Hub er initieret og udviklet af Industriens Fond.
Om Autodesk
Autodesk laver software til fremstillingsindstrier. Hvis du nogensinde har kørt en bil med høj ydeevne, beundret en skyskraber, brugt en smartphone eller set en god film, har du har du chancerne for, hvad millioner af Autodesk-kunder gør med vores software.
Læs mere
Fremtidens krav til 3D-print bliver sat nu
Fremtidens krav til 3D-print bliver sat nu
3D-print er hastigt på vej frem og det samme er standarder på området. Lige nu bliver der sat krav til alt lige fra processer, materialer, testmetoder og kvalitetsspecifikationer til data, design, miljø, sundhed og sikkerhed.
I takt med, at 3D-print i stigende grad indgår i produktionen, skaber de nye muligheder også behov for specifikke standarder for 3D-print. Det kan være inden for kvalitetssikring, kontrolmetoder og muligheden for at kunne graduere slutproduktets egenskaber fx i forhold til styrke.
– Kontrollen skal skræddersys til emnet. Jo mere kritisk en komponent er – økonomisk eller sikkerhedsmæssigt – des mere minutiøs og grundig er kvalitetskontrollen. Og der er også forskellige behov til fx styrkegraden afhængigt af, om det er lavrisikoforbrugsprodukter eller højrisikoprodukter, fortæller Nikolaj Kjelgaard Vedel-Smith, der er konsulent på Teknologisk Institut med særligt fokus på 3D-print.
Lavrisikoprodukter kunne fx være briller, pick-up’er og urremme eller nogle typer af produktionsværktøjer som laksegribere, småkagetyller og formværktøjer. I den modsatte ende af spektret finder man højrisikoprodukter som fx beslag til fly, hjulophæng til lastbiler eller brændkamre til raketter.
Der mangler fælles testmetoder
Noget af det, der er brug for i de kommende standarder, er således retningslinjer for testmetoder og kontrol samt klassificerings- eller gradueringsmuligheder, fx for styrkeniveauet.
– Ved defektbeskrivelser er der også behov for at kunne lave en klassificering. Der vil altid være imperfektioner i ting. I traditionelle støbninger er der også fejl, der bliver accepteret til en vis grænse. Vi har brug for noget tilsvarende på 3D-print området, hvor fx spændinger opbygges anderledes i emner end ved andre fremstillingsmetoder og kan resultere i deformation og revner, hvis ikke proceduren er korrekt forklarer Nikolaj Kjelgaard Vedel-Smith.
På samme måde er der brug for nye testmetoder til at detektere nogle typer af fejl, eller en kobling til eksisterende standarder, der hvor de kan finde gyldig anvendelse.
Der mangler kort sagt nogle rammer for, hvornår noget er godt nok, og nogle fælles retningslinjer og metoder til at udføre test og kontrol. Det gælder både traditionelle NDT (Non Destructive Testing), hvor man skal kunne udføre test på selve emnet uden at ødelægge det (fx CT-scanning, hvor eventuelle porøsiteter vil opdages) og hårdhedsprøver, metallurgiske prøver mv.
– Vi har på Teknologisk Institut været med i et Europæisk projekt (RepAIR) sammen med Lufthansa og Boeing omkring kvalitetssikring af 3D-print til flyindustrien. Her er en del af løsningen bl.a. at bygge overlappende trækprøvestænger sammen med komponenten i både X-, Y-, og Z-retningen. Ved efterfølgende at trække i stængerne, sikrer man sig, at der ikke er byggefejl i nogle dele af emnet, fortæller Nikolaj Kjelgaard Vedel-Smith og uddyber.
– Top og bund af trækprøvestængerne bruges til metallurgisk prøvning (hårdhed og SEM) og de små kugler, der sidder langs kanten af emnet, kvalitetssikrer, at iltniveauet ikke har overskredet de tilladte grænser under byggeprocessen.
Som et resultat af RepAIR projektet har Lufthansa i 2018 oprettet en 3D-printafdeling, der skal se på at fremstille sikkerhedskritiske reservedele til fly.
Et andet område, hvor der ifølge Nikolaj Kjelgaard Vedel-Smith kan være gavn af brugen af standarder er ISO-9001 i samspil med de gældende standarder for 3D-print, herunder særligt ISO-17296.
– Det meget fine pulver, som benyttes til metal 3D-print, skal man have respekt for, og det er derfor vigtigt at sikre et godt og sikkert arbejdsmiljø og de korrekte arbejdsprocedurer. Hos Teknologisk Institut er det et vedgående arbejde, som vi ønsker at løfte yderligere via ISO-9001. Dette er et vigtigt skridt, da det er forudsætningen for at kunne arbejde videre frem mod de standarder, der er, og kommer, inden for 3D-print til medicinal industrien.
Hvad kan og skal 3D-print leve op til?
Standarderne skal således være med til at sætte en ramme for den tekniske fremstillingsproces, procedurer, kontrol osv. Hvilket alt sammen i større eller mindre grad er en del af fundamentet for den forretning, man gerne vil bygge op, eller den sikkerhed, man behøver, når man køber produkter.
– Det handler altså i høj grad også om at ”få papir på”, at teknologien kan de ting, vi ved, den kan, understreger Nikolaj Kjelgaard Vedel-Smith
Dette er Mads Kjøller Damkjær, der er CEO i AM Hub, helt enig i.
– 3D print har som teknologi 30 år på bagen, men vi har været lidt bagud herhjemme. Det handler til dels om økonomi. De lande, der er længere fremme, er særligt lande med bil- og flyindustri. Her har større virksomheder kunnet investere mere og få et større udbytte. Men det handler også om, at mange danske virksomheder har været lidt tilbageholdende med at kaste sig ud i 3D-print, fordi de ikke føler, at det er gennemtestet nok, siger Mads Kjøller Damkjær.
Usikkerheden kan således handle om, at man er bange for at stå med et slutprodukt, som ikke er sikkert nok, eller som man ikke kan få solgt, fordi markedet ikke føler sig trygt ved at aftage det. Fælles kvalitetskrav og testmetoder kan være med til at fjerne barriererne og usikkerheden og åbne markedet.
– Hvad kan og skal 3D-print leve op til, hvordan matcher teknologien materialerne og hvordan kan man teste kvaliteten og sikkerheden? Det er her, standarder kan hjælpe. Der er allerede en del standarder og regulativer på vej, og det vil helst sikkert være med til at øge interessen for 3D-print, mener Mads Kjøller Damkjær.
Det handler ikke længere kun om teknik
Der er allerede sket en markant stigning i antallet af danske virksomheder, der anvender 3D-print, inden for de sidste par år. 25 pct. af danske fremstillingsvirksomheder bruger ifølge Dansk AM Rapport 2019 i dag 3D-print. Teknologien bruges primært til at fremstille prototyper til at understøtte produktudvikling og til støtteværktøjer, fx gribere og andet i produktionssammenhæng.
– Ved industriel brug er der særligt kommet fart på metal- og plastprint, og vi vil se flere og flere, der bruger 3D-print i slutprodukter også, mener Mads Kjøller Damkjær og fortsætter:
– Noget af det, der er rigtig interessant, er, at de henvendelser, vi får, ikke længere kun handler om teknik, men også om arbejdsmiljø, strategi, supply chain osv. Det fortæller mig, at 3D-print har fået en meget større plads i virksomheden, og at der er strategisk fokus på det til blandt andet at fremme innovation.
Denne udvikling øger behovet for standarder, der med fordel kan bruges allerede i produktudviklingsfasen – dels som et fundament af viden, man kan bygge ovenpå, og dels for at sikre, at man lever op til markedskravene på området. Af samme grund, kan det også være en god ide at være med, når standarderne bliver udviklet.
– Ved at deltage i standardiseringsarbejdet får virksomhederne tidlig viden, om, hvad der rører sig på området. Og den viden, kan bruges fx i produktudviklingen, forklarer Berit Aadal, der er seniorkonsulent i Dansk Standard og ansvarlig for det danske udvalg, der bidrager til at udvikle internationale 3D-print standarder.
Danske virksomheder kan påvirke fremtidens markedskrav
Udover muligheden for at få viden om markedet før alle andre, har danske virksomheder lige nu en unik mulighed for at påvirke udviklingen af de kommende standarder for 3D-print, fordi standardiseringsarbejdet stadig er i sin vorden.
– Standarderne kommer til at danne grundlag for fremtidens markedskrav til 3D-print på tværs af brancher og faggrænser. Derfor kan danske virksomheder få rigtigt meget ud af at sidde med rundt om bordet, når standarderne skal skrives, siger Berit Aadal.
Der er indtil videre udgivet 9 standarder inden for 3D-print. 25 er undervejs og der er 20 nye forslag til standarder ude. I det internationale standardiseringsarbejde fokuseres der bl.a. på terminologien omkring 3D-print, processer, materialer, testmetode, kvalitetsspecifikationer, data, design, miljø, sundhed og sikkerhed. Der er altså en lang række områder, hvor danske virksomheder kan være med til at styre innovationen og påvirke de krav, der skal stilles til 3D-print i fremtiden. Læs mere her: ds.dk/3d-print
Kom til MorgenBriefing
Vil du høre mere om 3D-print? Kom til gratis MorgenBriefing hos Dansk Standard den 22. maj, hvor du bl.a. kan høre Mads Kjøller Damkjær og Nikolaj Kjelgaard Vedel-Smith fortælle om, hvilke nye forretningsmuligheder 3D-print åbner op for. Tilmeld dig gratis her: ds.dk/morgenbriefing
Vil du gerne endnu mere i dybden med 3D-print og det internationale standardiseringsarbejde? Så tilmeld dig også til temamødet om 3D-print, der afholdes i umiddelbar forlængelse af MorgenBriefing: ds.dk/da/kurser/moede-om-3dprint
Fakta om standardiseringsarbejdet
Standardiseringsarbejdet er fordelt på følgende arbejdsgrupper, der udvikler standarder:
Arbejdsgruppe 1: Terminology
Arbejdsgruppe 2: Processes, systems and materials
Arbejdsgruppe 3: Test methods and quality specifications
Arbejdsgruppe 4: Data and Design
Arbejdsgruppe 5: Additive manufacturing in aerospace applications
Arbejdsgruppe 6: Environment, health and safety
Arbejdsgruppe 7: Additive manufacturing for plastics
Udover arbejdsgrupperne er der etableret over 20 ‘Joint Groups’ mellem ISO og ASTM, der er forankret under arbejdsgrupperne og som arbejder sammen om at udvikle standarder på forskellige områder.
I ISO/TC 261 opererer man med tre forskellige niveauer af standarder inden for 3D-print:
1) Generelle standarder: standarder der angiver generelle begreber, fælles krav eller som generelt er gældende for de fleste typer af 3D materialer, processer og applikationer
2) Kategoristandarder: standarder der angiver krav, der er specifikke for en materialekategori eller en proceskategori
3) Specialiserede standarder: standarder der angiver krav, der er specifikke for et materiale, en proces eller en applikation.
Tue Mantoni live i Charlie Tangos studie
Tue Mantoni, bestyrelsesformand i Dansk AM Hub live i Charlie Tangos studie om mulighederne i 3D print.