3D print-designforløb optimerer arbejdshandsker til superstyrke
3D print-designforløb optimerer arbejdshandsker til superstyrke
Virksomheden High Precisions Systems havde høje ambitioner med deres nyudviklede exoskelet handsker, da de gik ind til 3D print-designforløbet Design for Additive Manufacturing (DfAM). Alligevel blev virksomheden overrasket over, at teknologien i så høj grad formåede at forbedre de 3D printede titaniumhandsker ved at halvere tykkelsen og dermed øge både grebsstyrke og mindske slitage på fingerled.
De fleste kender filmene Ironman, hvor selveste jernmanden får superkræfter, når han ifører sig sin robotdragt. Referencen til Ironman er oplagt, når det kommer til den danske startup-virksomhed, High Procession Systems, der udvikler og laver exoskelet handsker – handsker, der er et nødvendigt og vigtigt redskab i industrien, hvor daglige og tunge løft kræver ekstra grebsstyrke.
“Helt konkret kan man tænke exoskelet handsker som en arbejdshandske, man tager på for at øge ens grebsstyrke markant fra håndleddet og gennem fingrene”, forklarer Niels K. B. Dahl, ejer af High Precisions Systems.
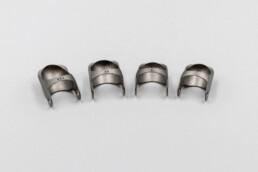
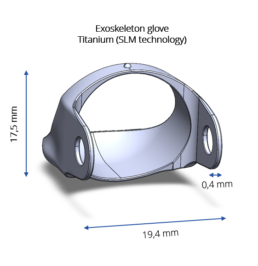
Fakta om løsningen:
- Materiale og teknologi: Titanium printet med Laser Powder Bed Fusion
- Godstykkelse: Reduceret fra 0,8 mm til 0,4 mm
- Vægtreduktion: 44 %
- Prisreduktion ved 3D print: 6 %
Lettere og stærkere end nuværende exoskelet handsker
Forud for DfAM-forløbet – et 3D print-designoptimeringsforløb – havde High Precisions Systems allerede udviklet en ny teknologi, hvor de lykkedes med at udvide anvendelsen af exoskelet handsken, så den også optager de kompressive kræfter.
“At vores handsker optager de kompressive kræfter, adskiller os særligt fra vores konkurrenter. Da graden af belastningen af et led under bevægelse er en af de store faktorer, der ligger til grund for udviklingen af slidgigt, kan vi – som de eneste os bekendt – ved at fjerne denne belastning være med til at sikre personalers fremtidige helbred”, lyder det fra Niels K.B. Dahl.
Deltagelsen i DfAM-forløbet resulterede i halvering af godstykkelse
Selvom High Precisions Systems exoskelet handske allerede havde et stort potentiale forud for DfAM-forløbet, gav deltagelsen flere væsentlige input til den videre udvikling. Særligt hvor langt det var muligt at presse grænserne for 3D print-teknologien i forhold til vægtykkelser på de printede komponenter.
“Deltagelsen i DfAM-forløbet var interessant for mig af flere årsager men særligt på grund af muligheden for at undersøge, hvor små godstykkelser det kunne lade sig gøre at producere. Godstykkelser er særlig interessante for os, da det er forskellen mellem at samle en kuglepen op med store tykke vinterhandsker eller tynde tilpassede kirurghandsker”, siger Niels K. B. Dahl:
“Dertil var det også vigtigt at producere test-emner. En ting er, at vi kan sidde og lave simuleringer på en computer, men en anden ting er, hvad der kan lade sig gøre at producere. Samtidig kan det i nogle tilfælde være svært at kvantificere et ‘feel’ af et objekt. Her er der ikke andet at gøre end at teste det i virkeligheden”.
Naturligt og tyndt fit – uden problemer
Interessen for at udfordre godstykkelsen på emnerne blev startskuddet til at sætte forløbet i gang – og det gav meget positive resultater og fornyet viden inden for 3D print.
“Fra starten havde vi lagt os fast på 0,8 millimeter i godstykkelse på de tyndeste steder på emnet. Men i forløbet undersøgte vi mulighederne og fik med stor succes godstykkelsen helt ned på 0,4 millimeter trods de komplekse geometrier. Med 3D print-teknologien gav det ingen problemer, selvom det er utrolig tyndt”, lyder det fra Niels K. B. Dahl.
Ud over at den halverede godstykkelse resulterer et mindre materialeforbrug, er den også lig et mere naturligt fit til handskens nuværende og kommende brugere.
”Man skal turde tage nogle chancer”
Niels K.B. Dahl peger særligt på én ting, som har haft stor værdi med virksomhedens deltagelse i DfAM-forløbet: Den nye opmærksomhed på 3D print-teknologiens muligheder og potentiale, som virksomheder kan få gavn af i deres udviklingsproces og konkurrencedygtighed.
“Inden DfAM-forløbet anvendte vi allerede 3D print, men jeg kendte ikke grænserne for metal 3D print, og det har været det primære at finde ud af: Altså at der er meget, der rent faktisk kan lade sig gøre”, siger Niels K. B. Dahl og uddyber vigtigheden i at turde tage chancer, når det kommer til de nye teknologier:
“Det, jeg vil sige til andre, der overvejer at deltage i et lignende forløb, er, at man skal turde tage nogle chancer og udnytte den teknologi, der er til rådighed, hvis man gerne vil forblive konkurrencedygtig – og her er 3D print en løsning, der ikke er til at komme uden om”.
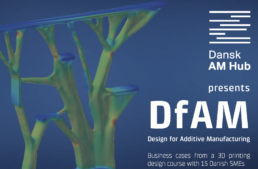
Kort om DfAM-forløbet
I løbet af 2022 har Dansk AM Hub i samarbejde med partnerne Teknologisk Institut, PLM Group, Hexagon og Wikifactory haft 15 danske SMV’er gennem et nyt innovationsforløb med henblik på at styrke virksomhederne til i endnu højere grad at drage fordel af det teknologiske og forretningsmæssige potentiale inden for 3D print. Forløbet kaldes Design for Additive Manufacturing (eller DfAM) og fokuserer på at udbrede 3D print til små- og mellemstore virksomheder samt at yde konkret støtte og hjælp til at arbejde med teknologien gennem design. Det konkrete mål for DfAM-forløbet er at re-designe deltagernes produkter eller komponenter, hvilket muliggør, at disse f.eks. kan fremstilles med større styrke, mindre materialespild, ny og bedre funktionalitet samt on-demand.
Læs mere om forløbet her.
Har du spørgsmål eller interesse i at deltage i DfAM-forløbet?
Kontakt Dansk AM Hub på info@am-hub.dk
Serman & Tipsmark optimerer nøgle til hydraulikudstyr: Sparer tid, materiale og penge
Serman & Tipsmark optimerer nøgle til hydraulikudstyr:
Sparer tid, materiale og penge
Serman & Tipsmark arbejder med hydraulik og laver blandt andet testanlæg til hydrauliske komponenter. Virksomheden så et potentiate for at optimere forskellige komponenter med 3D print og valgte derfor at undersøge det nærmere i designoptimeringsforløbet Design for Additive Manufacturing (DfAM).
I videoen herunder fortæller konstruktør Rune Simonsen om Serman & Tipsmarks erfaringer med 3D print.
I DfAM-forløbet kiggede den nordjyske virksomhed Serman & Tipsmark på to mulige emner til 3D print – henholdsvis en palette og en ‘nøgle’. Det viste sig, at omkostningerne ved at 3D printe paletten umiddelbart blev for høje, og virksomheden valgte derfor at se nærmere på optimering af nøglen. Nøglen er opbygget på en måde, så der sidder en såkaldt spline i den ene ende, og i den anden ende er der et hul med en not-gang – altså et relativt komplekst emne, der tager tid at bearbejde.
De potentielle gevinster for Serman & Tipsmark ved at få nøglen 3D printet er blandt andet tid, da produktionstiden er cirka den halve ved at få den 3D printet sammenlignet med konventionel bearbejdning. Der er også en gevinst i forhold til reduceret vægt, og selvom det ikke er afgørende for dette emne, har det alligevel betydning, da prisen på 3D print bliver lavere, i takt med at man sparer materiale. Der blev lavet forskellige designiterationer af nøglen, og resultatet endte med en vægtreduktion på helt op til 79 procent i titanium – og i aluminium kunne prisen blive op til 32 procent lavere end konventionelt.
“Vi valgte at deltage i forløbet, fordi vi har mange projekter, hvor det er få styk af hvert emne. Potentialet er at lokalisere, hvor vi kan vægtoptimere – så hvis det er en hydraulikblok, kan vi måske lave noget flow-optimering og lave nogle mindre emner, end vi plejer at gøre”, forklarer konstruktør hos Serman & Tipsmark, Rune Simonsen.
Disse resultater har Serman & Tipsmark skabt ved hjælp af 3D print designoptimering:
- 79 % vægtreduktion i forhold til originalen
- Kortere leveringstid: Fra 6 uger til 2 uger
- 32 % prisreduktion ved 3D print i aluminium
- Valget faldt på titanium, hvor pris er sammenlignelig med traditionel fremstilling
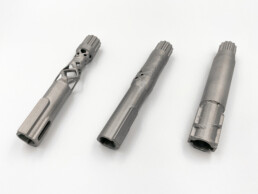
I løbet af 2022 har 15 danske virksomheder arbejdet med at redesigne et produkt eller komponent ved hjælp af 3D print gennem Dansk AM Hubs innovationsforløb: Design for Additive Manufacturing (DfAM). Ud af disse har 11 af virksomhederne haft en ’før-komponent’, som det har været muligt at sammenligne den redesignede komponent med, og i ti af disse tilfælde har det været muligt at reducere vægten med mellem 43 og 96 procent. Fordelene ved vægtreduktion har haft forskellige formål afhængig af virksomhedens specifikke produktion og slutprodukter.
Konkret i DfAM-projektet har målet været at designe deltagernes komponenter eller produkter bedre eller anderledes, så de kan fremstilles med mindre materiale, større styrke, og optimeret med ny eller bedre funktionalitet og effektivitet.
Efter forløbet har de tilmeldte virksomheder stået med en fysisk redesignet komponent eller produkt, hvor en eller flere af førnævnte fordele er tænkt ind. Ud over vægtreduktion har DfAM også givet en række andre fordele såsom reduktion af produktionsomkostninger, reduktion i ”time-to-market”, partkonsolidering, større designfrihed og forøgelse af komponentstyrke.
På den måde har deltagerne fået merværdi og viden, som kan forankres lokalt i deres produktion.
Om DfAM-forløbet
- DfAM innovationsforløbet sigter mod at styrke virksomhederne til i endnu højere grad at drage fordel af det teknologiske og forretningsmæssige potentiale inden for 3D print.
- DfAM-projektet har haft til formål at udbrede kendskabet til 3D print og DfAM samt gøre danske virksomheder i stand til at udnytte de tekniske og forretningsmæssige muligheder, som AM-teknologien giver.
- Traditionelt set er 3D print blevet brugt til fremstilling af prototyper, men teknologien rummer også en lang række andre muligheder. 3D-print kan med fordel også bruges til eksempelvis pilot- og småserieproduktion, og fremstilling af fiksturer og hjælpe-værktøjer, sprøjtestøbeværktøjer, og reservedele.
- Ud over en enkelt case med en vægtforøgelse blev komponentvægten reduceret med mellem 43 procent og 96 procent på de ti cases.
- Projektet er initieret af Dansk AM Hub i samarbejde med partnerne Teknologisk Institut, PLM Group, Hexagon og Wikifactory.
Læs mere om forløbet her.
Har du spørgsmål eller interesse i at deltage i DfAM-forløbet?
Kontakt Dansk AM Hub på info@am-hub.dk
Med 3D print spiller violinen bedre og mere bæredygtigt
Med 3D print spiller violinen bedre og mere bæredygtigt
Larsen Strings producerer nogle af verdens bedste strenge til nogle af verdens bedste musikere – og i 3D print-designoptimeringsforløb Design for Additive Manufacturing (DfAM) fik de mulighed for at teste 3D print til et specialværktøj i produktionen.
Den danske virksomhed Larsen Strings producerer strenge til celloer, violiner og violaer. I produktionen har virksomheden en forholdsvis stor værktøjskomponent, hvor der i dag med traditionel fremstilling bliver fræset en del materiale ud – materiale, der bare går til spilde. Derfor ønskede Larsen Strings at undersøge, om 3D print kunne være en mulighed, da teknologien muliggør produktion med kun akkurat den mængde materiale, der er nødvendigt for at lave komponenten.
Denne mulighed testede Larsen Strings i 3D print-designoptimeringsforløbet Design for Additive Manufacturing (DfAM).
Topologioptimeringen har resulteret i et design med organiske former og knoglelignende struktur.
“I dag er udfordringerne ved den her komponent, at vi til tider skal bruge en ny af den – og fordi det både er et materiale, der kan være svært at få fat i og samtidig svært at bearbejde i, vil vi gerne kigge på andre materialer, hvor vi bruger mindre mængder”, siger Product Development Engineer ved Larsen Strings, Lasse Krogh Johannsen.
I DfAM-projektet printede de komponenten i titanium, som er både let og stærkt, og derved lykkedes det at reducere vægten med 43 procent og samtidig øge styrken med 130 procent.
På trods af de imponerende resultater endte prisen desværre også med at stige med 200 procent, hvorfor Larsen Strings ikke går videre med løsningen i første omgang.
Disse resultater har Larsen Strings skabt ved hjælp af 3D print designoptimering:
- Enorm designfrihed og fleksibilitet
- 43 % vægtreduktion i forhold til traditionelt værktøj
- 130 % forøgelse af styrken i forhold til traditionelt værktøj
- 3D print i titanium – i stedet for aluminium, som tidligere blev brugt
I løbet af 2022 har 15 danske virksomheder arbejdet med at redesigne et produkt eller komponent ved hjælp af 3D print gennem Dansk AM Hubs innovationsforløb: Design for Additive Manufacturing (DfAM). Ud af disse har 11 af virksomhederne haft en ’før-komponent’, som det har været muligt at sammenligne den redesignede komponent med, og i ti af disse tilfælde har det været muligt at reducere vægten med mellem 43 og 96 procent. Fordelene ved vægtreduktion har haft forskellige formål afhængig af virksomhedens specifikke produktion og slutprodukter.
Konkret i DfAM-projektet har målet været at designe deltagernes komponenter eller produkter bedre eller anderledes, så de kan fremstilles med mindre materiale, større styrke, og optimeret med ny eller bedre funktionalitet og effektivitet. Alt sammen med det formål at skabe mere bæredygtige produkter og komponenter.
Efter forløbet har de tilmeldte virksomheder stået med en fysisk redesignet komponent eller produkt, hvor en eller flere af førnævnte fordele er tænkt ind. Ud over vægtreduktion har DfAM også givet en række andre fordele såsom reduktion af produktionsomkostninger, reduktion i ”time-to-market”, partkonsolidering, større designfrihed og forøgelse af komponentstyrke.
På den måde har deltagerne fået merværdi og viden, som kan forankres lokalt i deres produktion.
Om DfAM-forløbet
- DfAM innovationsforløbet sigter mod at styrke virksomhederne til i endnu højere grad at drage fordel af det teknologiske og forretningsmæssige potentiale inden for 3D print.
- DfAM-projektet har haft til formål at udbrede kendskabet til 3D print og DfAM samt gøre danske virksomheder i stand til at udnytte de tekniske og forretningsmæssige muligheder, som AM-teknologien giver.
- Traditionelt set er 3D print blevet brugt til fremstilling af prototyper, men teknologien rummer også en lang række andre muligheder. 3D-print kan med fordel også bruges til eksempelvis pilot- og småserieproduktion, og fremstilling af fiksturer og hjælpe-værktøjer, sprøjtestøbeværktøjer, og reservedele.
- Ud over en enkelt case med en vægtforøgelse blev komponentvægten reduceret med mellem 43 procent og 96 procent på de ti cases.
- Projektet er initieret af Dansk AM Hub i samarbejde med partnerne Teknologisk Institut, PLM Group, Hexagon og Wikifactory.
Læs mere om forløbet her.
Har du spørgsmål eller interesse i at deltage i DfAM-forløbet?
Kontakt Dansk AM Hub på info@am-hub.dk
Linatech: "Designfriheden ved 3D print er genial"
Linatech: “Designfriheden ved 3D print er genial”
Under det nyligt overståede 3D print-designforløb Design for Additive Manufacturing (DfAM) fik Linatech mulighed for at optimere en komponent til en maskine, der håndterer blodprøver. Forløbet gav ikke blot gode resultater men også endnu mere blod på tanden til at give sig i kast med 3D print.
Virksomheden Linatech fungerer som industriel samarbejdspartner på B2B-markedet, hvor de laver specialløsninger til flere forskellige industrielle segmenter inden for blandt andet produktion, logistik og processtyring. Et af disse segmenter er medicinalindustrien, hvor Linatech laver udstyr til forsendelse og håndtering af blodprøver – og her er 3D print i den grad er oplagt.
”For nogle år tilbage skulle vi udvikle nyt udstyr til vores portefølje, og vi var på det tidspunkt tvunget til at gøre noget andet og tænke anderledes end tidligere. Det betød også, at 3D print stod lige for døren, og det var en kæmpe revolutionerende udviklingsfrihed, hvor de begrænsninger, der før har været, forsvandt. Det var en øjenåbner dengang – og det er det stadigvæk i dag”, lyder det fra Martin Arberg, direktør og ejer af Linatech.
Og netop introduktionen til 3D print samt en konkret problemstilling til en af deres maskiner til håndtering af blodprøver betød, at deltagelsen i DfAM-forløbet var perfekt timet og meget aktuelt for Linatech, da forløbet netop sætter fokus på at designoptimere komponenter til 3D print-teknologien.
Styrke og vægt var vigtige faktorer
Selve problemstillingen, som Linatech gik ind i forløbet med, omhandlede en komponent, der skulle vægtreduceres for at få den ønskede effekt. For at komme i mål med det ønske var første skridt at undersøge mulighederne i at forbedre designet, hvilket resulterede i en optimeret polymer-komponent, som efterfølgende skulle overfladebehandles.
”Vi havde en problematik vedrørende vægtreduktion på en komponent, der skal rotere 300 omdrejninger i minutter, og hvor selve komponenten både skulle have styrke og samtidig være let. Og med 3D print blev det muligt både at lave et emne, der var hult for at reducere vægten og samtidig havde en rigtig stor styrke”, forklarer Martin Arberg.
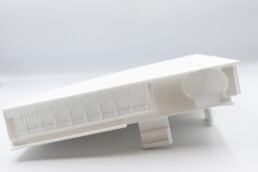
Fakta om løsningen:
- Materiale og teknologi: Nylon printet med Laser Powder Bed Fusion
- Vægtreduktion: 81%
- Prisreduktion: 42,8%
- Energibesparelse per år: 638 Watt
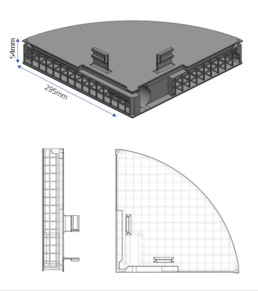
Reducering af vægten – men bevarelse af styrke
Ud over at bibeholde styrken fremhæver Martin Arberg også, hvordan vægtreduktionen har en positiv gevinst i form af en reel energibesparelse, når maskinen kører. Desuden giver 3D print mulighed for at lave avancerede geometrier – uden det koster ekstra.
”Reduktionen af vægten er en klar energieffektivisering – f.eks. når du skal accelerere noget op eller ned i hastighed. Jo mindre masse du har, jo nemmere er det også at holde på plads, og jo mindre energi skal du også bruge til opbremsning og acceleration”, lyder det fra Martin Arberg:
”Normalvis ville det tage rigtig mange timer, hvor man med 3D print kan lave nogle utrolig avancerede strukturer, uden at det koster mere. Skulle man f.eks. have bearbejdet det i aluminium eller et andet materiale, ville en lignende komponent slet ikke kunne lade sig gøre at lave, så derfor er designfriheden med 3D print genial”.
Budskabet er klart: Hop med på 3D print teknologien
Går man som virksomhed og overvejer at deltage i et lignende forløb eller generelt at udvikle sin horisont inden for 3D print, er hverken Martin Arberg eller teknisk chef hos Linatech, Simon Paarup, i tvivl om, at teknologien giver helt nye muligheder.
”Som virksomhed er det nødvendigt, at man udvider sin horisont og ikke tror, at man allerede har fundet de vise sten. For så er jeg overbevist om, at man bliver overhalet inden om, fordi der er uanede muligheder med 3D print”, vurderer Simon Paarup”
”Jeg vil til enhver tid også sige, at hvis man begynder at arbejde med 3D print, er der ikke nogen vej tilbage, fordi teknologien er noget, der bidrager som en god gevinst og et innovativt indspark for en virksomhed – så det er bare med at hoppe på vognen”, lyder det afsluttende fra Martin Arberg.
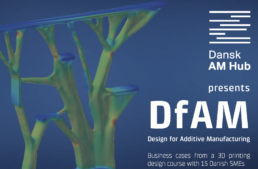
Kort om DfAM-forløbet
I løbet af 2022 har Dansk AM Hub i samarbejde med partnerne Teknologisk Institut, PLM Group, Hexagon og Wikifactory haft 15 danske SMV’er gennem et nyt innovationsforløb med henblik på at styrke virksomhederne til i endnu højere grad at drage fordel af det teknologiske og forretningsmæssige potentiale inden for 3D print. Forløbet kaldes Design for Additive Manufacturing (eller DfAM) og fokuserer på at udbrede 3D print til små- og mellemstore virksomheder samt at yde konkret støtte og hjælp til at arbejde med teknologien gennem design. Det konkrete mål for DfAM-forløbet er at re-designe deltagernes produkter eller komponenter, hvilket muliggør, at disse f.eks. kan fremstilles med større styrke, mindre materialespild, ny og bedre funktionalitet samt on-demand.
Læs mere om forløbet her.
Har du spørgsmål eller interesse i at deltage i DfAM-forløbet?
Kontakt Dansk AM Hub på info@am-hub.dk
3D print-designforløb satte fart på udviklingshjulene hos CeramicSpeed
3D print-designforløb satte fart på udviklingshjulene hos CeramicSpeed
Inden for cykelsport tæller hvert et gram på cyklen. Det ved CeramicSpeed, som har specialiseret sig i lejer til cykler. Derfor valgte virksomheden at deltage i innovationsforløbet Design for Additive Manufacturing (DfAM), hvor de undersøgte, om en af deres komponenter kunne optimeres med 3D print.
Med cyklerne fast parkeret i Holstebro har CeramicSpeed siden 2004 sørget for hurtige omdrejninger med deres speciale i keramiske kuglelejer til cykelsport. Virksomheden havde allerede gode erfaringer med 3D print-teknologien – f.eks. bruger de 3D print til deres tandhjul i titanium, de såkaldte pulleyhjul, som er verdens letteste. Med disse erfaringer i cykeltasken var det derfor en nem beslutning for CeramicSpeed at takke ja til at deltage i 3D print-designoptimeringsforløbet DfAM.
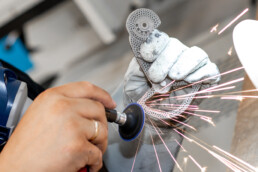
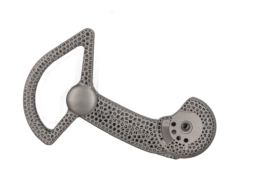
Fakta om løsningen:
- Materiale og teknologi: Titanium printet med Laser Powder Bed Fusion
- Vægtforøgelse: 188 %
- Reduktion af volumen: 43 %
- Designfrihed: Høj
CeramicSpeed var interesseret i at arbejde med en komponent, nemlig en holder på cyklens bagskifter, som bliver brugt i forbindelse med gearskiftet, hvor den fastholder de to førnævnte pulleyhjul.
“I dag bliver vores holder trykstøbt i kulfiberforstærket polymer, mens vores pulleyhjul bliver 3D printet, når det skal være ekstravagant og se rigtig godt ud. Det var netop også derfor, at ideen om også at 3D printe holderen opstod – timet med at muligheden også opstod”, fortæller Carsten Ebbesen, R&D Manager hos CeramicSpeed.
Brug af nyt materiale
I forbindelse med 3D print af holderen blev det også undersøgt, om det var muligt at skifte materiale. Holderen bliver støbt i kulfiberforstærket polymer, fordi det er et let og stærkt materiale, men i DfAM-forløbet forsøgte man at udskifte kulfiber med titanium.
“De to primære årsager til at 3D printe holderen var, at vi gerne ville prøve at se, om vi kunne printe den i titanium for at undersøge, om vi kunne gøre den endnu stærkere og smartere med gitterstruktur – og samtidig gøre den lettere”, lyder det fra Carsten Ebbesen.
Potentiale til videre udvikling
I DfAM-forløbet lykkedes det at få printet en stærk holder med gitterstruktur, der samtidig reducerede mængden af materiale. Men for at nå helt i mål med en ny holder vil der også skulle justeres på vægten.
“Undervejs i projektet har vi fundet ud af, at vægten er problematisk, når vi 3D printer holderen i titanium. Derfor vil det videre arbejde bestå i at undersøge, om vi kan komme ned i vægt med titanium ved at lave forskellige designændringer”, forklarer Carsten Ebbesen.
3D print kan gøre udviklingsprocessen mere konkret
Selvom der stadig ligger et udviklingsarbejde med den 3D printede holder i titanium, er Carsten Ebbesen ikke i tvivl om, at 3D print har mange fordele.
“3D print har givet os muligheden for at få holderen håndgribeligt i hænderne, og det har været noget helt andet end at sidde og lave tegninger. Derudover har vi fået mulighed for at lave gitterkonstruktioner på holderen, som kun er mulige at lave med 3D print”, lyder det fra Carsten Ebbesen:
“Det har også haft stor værdi, at jeg konkret har kunnet vise mine kolleger, hvad vi har lavet undervejs i forløbet. Det har betydet, at vi hurtigere har kunnet fornemme, hvor mulighederne var”.
Ingen begrænsninger på design
Carsten Ebbesen fremhæver især designfriheden som en af de helt store fordele, når det kommer til CeramicSpeeds oplevelse med 3D print i DfAM-forløbet.
“Vores holdning og oplevelse med 3D print er, at det er en fantastisk teknologi, fordi der ikke er nogen begrænsninger, når det kommer til designmulighederne. Samtidig er vores produkter meget drevet af design, og udseendet betyder meget for både os og kunderne, så produkterne må gerne have en ‘bling’ effekt – og det kan vi opnå med 3D print”, lyder det fra Carsten Ebbesen.
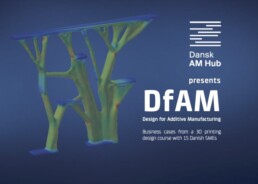
Kort om DfAM-forløbet
I løbet af 2022 har Dansk AM Hub i samarbejde med partnerne Teknologisk Institut, PLM Group, Hexagon og Wikifactory haft 15 danske SMV’er gennem et nyt innovationsforløb med henblik på at styrke virksomhederne til i endnu højere grad at drage fordel af det teknologiske og forretningsmæssige potentiale inden for 3D print. Forløbet kaldes Design for Additive Manufacturing (eller DfAM) og fokuserer på at udbrede 3D print til små- og mellemstore virksomheder samt at yde konkret støtte og hjælp til at arbejde med teknologien gennem design. Det konkrete mål for DfAM-forløbet er at re-designe deltagernes produkter eller komponenter, hvilket muliggør, at disse f.eks. kan fremstilles med større styrke, mindre materialespild, ny og bedre funktionalitet samt on-demand.
Læs mere om forløbet her.
Har du spørgsmål eller interesse i at deltage i DfAM-forløbet?
Kontakt Dansk AM Hub på info@am-hub.dk
Design med 3D print giver mere effektive vaskerobotter hos Washpower
Design med 3D print giver mere effektive vaskerobotter hos Washpower
Virksomheden Washpowers deltagelse i 3D print-forløbet Design for Additive Manufacturing (DfAM) har givet mulighed for at udvikle på en komponent til deres serie af vaskerobotter til svinestalde. I fremtiden kan udviklingen med 3D print betyde en væsentlig reduktion på vand- og energiforbruget.
Den danske virksomhed Washpower blev etableret i 2016, og herefter fik man hurtigt fart på salget af vaskerobotter og automatiserede vaskeløsninger til svinestalde og kyllingehuse. Vaskerobotterne bliver i dag solgt i over 30 lande – og flere lande er på vej.
– Målet for Washpower er at udvikle brugervenlige robotter, der tager det hårde arbejde med vask – og når landmanden fx sætter sin vaskerobot i gang om aftenen, er det vigtigt, at den har gjort sit arbejde den næste morgen, fortæller Martin Kamp, teknisk udvikler hos Washpower.
Med henblik på at effektivisere deres robotter yderligere og gøre de automatiserede vaskeløsninger mere fordelagtige for landmændene, var det uden tøven, at Washpower sagde ja til at deltage i 3D print-designforløbet DfAM, som er initieret af Dansk AM Hub.
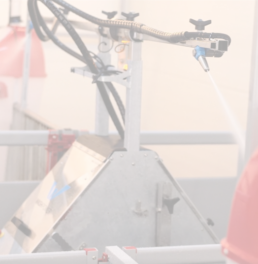
Fakta om løsningen:
- Materiale og teknologi: Titanium printet med Laser Powder Bed Fusion
- Reduktion af antal parter: Fra 2 parter til 1 part
- Designfrihed: Mulighed for at teste forskellige former og geometrier
Washpower vil lave en patentansøgning på baggrund af resultaterne.
3D print giver nye muligheder med stor betydning
Undervejs i DfAM-forløbet undersøgte Washpower, om det var muligt at optimere en komponent til deres x100 serie af vaskerobotter.
”For os var det oplagt at undersøge muligheden for at optimere en specifik komponent i vores x100 serie og dermed udnytte potentialet for at gøre vores robotter endnu mere effektive”, lyder det fra Martin Kamp:
”Undervejs har vi haft særligt fokus på at optimere vandforbruget under vaskeprocessen. Det kan også vise sig, at vi med den nyudviklede komponent gør robotten mere effektiv, så man kan vaske hurtigere og på den måde optimere energi- og vandforbruget yderligere – eller måske opnå en større rækkevidde. Så der er mange parametre, vi har kigget på i dette projekt, og det er klart en stor drivkraft”.
Gevinsten er større designfrihed og en hurtigere udviklingsproces
Netop denne fokus på energi- og vandbesparelse er afhængig af flere dele – herunder optimering af designet og de komponenter, der sidder i maskinen. Derfor var 3D print i særdeleshed oplagt med sin store designfrihed, der kan gøre nye løsninger og ideer mulige.
”Det, jeg ser ved 3D print, er, at man kan begynde at lave geometrier indvendigt på komponenterne. Det ville være utroligt svært med almindelige bearbejdningsformer, fordi man ikke kan komme derind med sit værktøj – for eksempel er den komponent, vi har arbejdet med i projektet, ikke særlig stor, og her har 3D print givet nye muligheder for at printe de indre geometrier”, fortæller Martin Kamp.
Ud over de fornyede muligheder med indre geometrier peger Martin Kamp også på, hvordan 3D print kan bidrage til et hurtigere udviklingsforløb, fordi Washpower meget hurtigt kan lave fysiske dele, som kan indgå som funktionelle prototyper og dermed forkorte udviklingstiden væsentligt frem til et produktionsklart emne.
Et større netværk og ny erfaring
Når Martin Kamp skal beskrive, hvad Washpower har fået ud af at deltage i DfAM-forløbet, er et større netværk og det tværfaglige samarbejde ikke til at komme udenom.
”Hvis man overvejer at deltage i et sådant forløb, skal man også gøre det, fordi det giver et godt netværk. Det er i min verden rigtigt vigtigt at have, fordi man kommer ud og snakker med andre, der har gang i noget lignede”, lyder det fra Martin Kamp, der tilføjer, hvordan et godt netværk kan være positivt i et fremtidigt perspektiv:
”Ens netværk kan også gøre, at man kommer lettere over de bump, der uundgåeligt dukker op, hvilket altid er en positiv ting. Men helt generelt med 3D print, så gør et forløb som dette, at man hurtigere kan få en 3D printet prototype, som rent faktisk virker”.
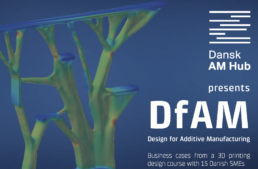
Kort om DfAM-forløbet
I løbet af 2022 har Dansk AM Hub i samarbejde med partnerne Teknologisk Institut, PLM Group, Hexagon og Wikifactory haft 15 danske SMV’er gennem et nyt innovationsforløb med henblik på at styrke virksomhederne til i endnu højere grad at drage fordel af det teknologiske og forretningsmæssige potentiale inden for 3D print. Forløbet kaldes Design for Additive Manufacturing (eller DfAM) og fokuserer på at udbrede 3D print til små- og mellemstore virksomheder samt at yde konkret støtte og hjælp til at arbejde med teknologien gennem design. Det konkrete mål for DfAM-forløbet er at re-designe deltagernes produkter eller komponenter, hvilket muliggør, at disse f.eks. kan fremstilles med større styrke, mindre materialespild, ny og bedre funktionalitet samt on-demand.
Læs mere om forløbet her.
Har du spørgsmål eller interesse i at deltage i DfAM-forløbet?
Kontakt Dansk AM Hub på info@am-hub.dk
3D printet design får drone til at flyve længere og løfte tungere
3D printet design får drone til at flyve længere og løfte tungere
Den danske startup Airflight testede metal 3D print i designoptimeringsforløbet Design for Additive Manufacturing (DfAM), hvor de lykkedes med at med at reducere vægten med hele 67 procent på et letvægtsbeslag til vingerne på deres fragtdrone.
I videoen herunder kan du høre mere om Airflights optimeringsarbejde fra ejer og direktør Mikkel Kærsgaard Sørensen – og ikke mindst se dronen i luften.
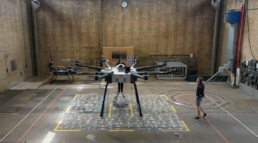
Airflight har til huse i Brønderslev, hvorfra de bygger nogle af verdens største multirotorer – i princippet en forvokset drone – til at flyve med komponenter og værktøjer i vindmølleindustrien. Den største drone har otte arme og kan løfte helt op til 200 kg.
Virksomheden valgte at deltage i 3D print-designoptimeringsforløbet DfAM for at undersøge mulighederne for de beslag, der holder armene på dronen. I projektet blev beslagene designoptimeret med 3D print, så de blev både lettere og alligevel kunne modstå belastningerne – og samtidig 3D printede man dem i titanium. Det førte til en vægtreduktion på 67 procent – eller hele 11 kg per drone.
“Gennem projektet har vi opnået 11 kg vægtreduktion og reduceret materialemængden med 80 procent. Værdien for os er den ekstreme designfleksibilitet, hvor vi kan opnå større styrke-til-vægt-forhold, hvilket er en vigtig del i aviation, da det betyder, at vi kan flyve i længere tid eller med en tungere last”, siger ejer og direktør i Airflight, Mikkel Kærsgaard Sørensen.
Disse resultater har Airflight skabt ved hjælp af 3D print designoptimering:
- 59 % vægtreduktion på hvert beslag
- 11 kg vægtreduktion på hele dronen
- 80 % reduktion af materialemængden
- Mindre materialespild end ved at fræse beslaget ud
I løbet af 2022 har 15 danske virksomheder arbejdet med at redesigne et produkt eller komponent ved hjælp af 3D print gennem Dansk AM Hubs innovationsforløb: Design for Additive Manufacturing (DfAM). Ud af disse har 11 af virksomhederne haft en ’før-komponent’, som det har været muligt at sammenligne den redesignede komponent med, og i ti af disse tilfælde har det været muligt at reducere vægten med mellem 43 og 96 procent. Fordelene ved vægtreduktion har haft forskellige formål afhængig af virksomhedens specifikke produktion og slutprodukter.
Konkret i DfAM-projektet har målet været at designe deltagernes komponenter eller produkter bedre eller anderledes, så de kan fremstilles med mindre materiale, større styrke, og optimeret med ny eller bedre funktionalitet og effektivitet. Alt sammen med det formål at skabe mere bæredygtige produkter og komponenter.
Efter forløbet har de tilmeldte virksomheder stået med en fysisk redesignet komponent eller produkt, hvor en eller flere af førnævnte fordele er tænkt ind. Ud over vægtreduktion har DfAM også givet en række andre fordele såsom reduktion af produktionsomkostninger, reduktion i ”time-to-market”, partkonsolidering, større designfrihed og forøgelse af komponentstyrke.
På den måde har deltagerne fået merværdi og viden, som kan forankres lokalt i deres produktion.
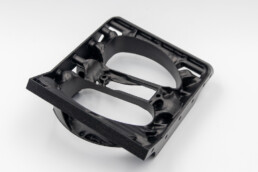
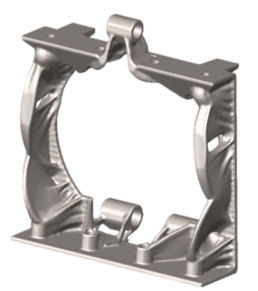
Om DfAM-forløbet
- DfAM innovationsforløbet sigter mod at styrke virksomhederne til i endnu højere grad at drage fordel af det teknologiske og forretningsmæssige potentiale inden for 3D print.
- DfAM-projektet har haft til formål at udbrede kendskabet til 3D print og DfAM samt gøre danske virksomheder i stand til at udnytte de tekniske og forretningsmæssige muligheder, som AM-teknologien giver.
- Traditionelt set er 3D print blevet brugt til fremstilling af prototyper, men teknologien rummer også en lang række andre muligheder. 3D-print kan med fordel også bruges til eksempelvis pilot- og småserieproduktion, og fremstilling af fiksturer og hjælpe-værktøjer, sprøjtestøbeværktøjer, og reservedele.
- Ud over en enkelt case med en vægtforøgelse blev komponentvægten reduceret med mellem 43 procent og 96 procent på de ti cases.
- Projektet er initieret af Dansk AM Hub i samarbejde med partnerne Teknologisk Institut, PLM Group, Hexagon og Wikifactory.
Læs mere om forløbet her.
Har du spørgsmål eller interesse i at deltage i DfAM-forløbet?
Kontakt Dansk AM Hub på info@am-hub.dk
3D printede designs giver god genlyd hos Scan-Speak
3D printede designs giver god genlyd hos Scan-Speak
Virksomheden Scan-Speak fik under et 3D print-designoptimeringsforløb mulighed for at give sig i kast med udviklingen af højdetaljerede prototyper – det gav blandt andet anledning til at anvende nye materialer.
Virksomheden Scan-Speak er en mindre vestjysk virksomhed, der til dagligt udvikler håndbyggede high-end højtalere til selvbyggere og flere store virksomheder – både nationalt og internationalt. For at blive klogere på mulighederne og potentialet i 3D print til højtalerkomponenter valgte Scan-Speak at deltage i 3D print-designforløbet Design for Additive Manufacturing (DfAM).
Når det kommer til designmulighederne af enheder til højtalere, er der dog visse begrænsninger. Enhederne fungerer nemlig i lukkede systemer, fordi tryk og stød er essentielle for, at den helt rigtige lyd kommer ud af højtalerne. Derfor var optimering af eksempelvis vægten ikke udgangspunktet for Scan-Speak. Til gengæld var der en stor interesse for muligheden for at 3D printe protyper af høj og nøjagtig kvalitet for at sikre en effektiv proces med henblik på at optimere og udvikle hele produktionslinjen.
Fik øjnene op for prototypers høje kvalitet
Forud for projektet havde Scan-Speak allerede kendskab til 3D print, da virksomheden tidligere havde investeret i en ældre 3D printer. Problemet var dog, at den ikke altid gav et tilfredsstillende resultat, når det kom til prototyper, der krævede en højere detaljeringsgrad.
”I DfAM-forløbet startede vi med at printe nogle testenheder, der faktisk havde en meget høj og præcis kvalitet modsat de prototyper, vi selv har kunnet printe. Det betød, at vi kunne se, hvordan det så ud som færdigt produkt. Da vi fik den printede prototype, blev vi virkelig positivt overraskede over både kvalitet og udseende”, lyder det fra Jacob Sand Nielsen, mekanisk ingeniør hos Scan-Speak.
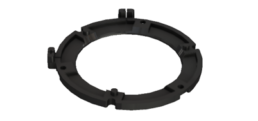
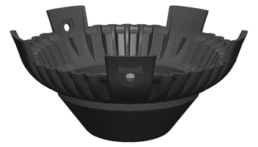
Fakta om løsningen:
- Materiale og teknologi: Nylon og Aluminium printet med Laser Powder Bed Fusion samt TPU (fleksibelt plast) printet med Multi Jet Fusion
- Tolerancer: Godkendt
- Overflader: Godkendt
- Leveringstid: 10 arbejdsdage
Print af prototyper giver rigtig god mening
Med det positive resultat printede Scan-Speak flere prototyper, hvor det store potentiale i 3D print-teknologien ikke var til at tage fejl af:
”Vi har blandt andet fået printet et specialdesignet skin (etui, red.) til en kunde, der skulle have nogle højtalere. Her har vi netop fået mulighed for at prøve at printe i et blødt plastmateriale, så dette skin blev, som det vil være til slut, og vi fik også testet printede komponenter i aluminium. Det har stor betydning, at vi kan teste, inden vi sætter yderligere værktøjer i gang – ligesom det har været en åbenbaring, at man kan printe i et blødt materiale”, fortæller Jacob Sand Nielsen:
”Derfor har det givet rigtig god mening at få printet prototyper, inden man trykker på den store knap og får sat i gang i et større maskineri. På den måde kan vi få testet det hele af med både finish og materialer”.
”Det er bare med at springe ud i det”
For Scan-Speak har deltagelsen i DfAM-forløbet betydet unik sparring omkring fremtidige muligheder inden for 3D print samt fornyet viden. Af samme grund er budskabet hos Scan-Speak også klart, hvis man som virksomhed overvejer at deltage i et fremtidigt DfAM-forløb.
”Det er bare med at springe ud i det! Og hvis man ikke har en 3D printer, er det en oplagt mulighed for at se, hvad teknologien kan. Især mulighederne i forhold til traditionel fremstilling, hvor man jo kan finde ud af, at et værktøj ikke passer, og at noget skal flyttes en millimeter – men man kan jo ikke bare omstøbe noget en millimeter, og så bliver du nødt til at starte helt forfra, og det er dyrt. Så hvis der er nogle, der endnu ikke er kommet i gang med 3D print-teknologien, er det bare med at prøve det”, lyder det fra Jacob Sand Nielsen.
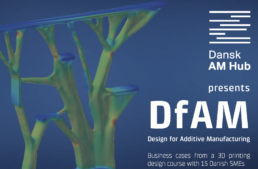
Kort om DfAM-forløbet
I løbet af 2022 har Dansk AM Hub i samarbejde med partnerne Teknologisk Institut, PLM Group, Hexagon og Wikifactory haft 15 danske SMV’er gennem et nyt innovationsforløb med henblik på at styrke virksomhederne til i endnu højere grad at drage fordel af det teknologiske og forretningsmæssige potentiale inden for 3D print. Forløbet kaldes Design for Additive Manufacturing (eller DfAM) og fokuserer på at udbrede 3D print til små- og mellemstore virksomheder samt at yde konkret støtte og hjælp til at arbejde med teknologien gennem design. Det konkrete mål for DfAM-forløbet er at re-designe deltagernes produkter eller komponenter, hvilket muliggør, at disse f.eks. kan fremstilles med større styrke, mindre materialespild, ny og bedre funktionalitet samt on-demand.
Læs mere om forløbet her.
Har du spørgsmål eller interesse i at deltage i DfAM-forløbet?
Kontakt Dansk AM Hub på info@am-hub.dk
3D printede designs sætter virksomheders produkter på slankekur
3D printede designs sætter virksomheders produkter på slankekur
I løbet af 2022 har 15 danske virksomheder arbejdet med at redesigne et produkt eller komponent ved hjælp af 3D print gennem Dansk AM Hubs innovationsforløb: Design for Additive Manufacturing (DfAM). Ud af disse har 11 af virksomhederne haft en ’før-komponent’, som det har været muligt at sammenligne den redesignede komponent med, og i ti af disse tilfælde har det været muligt at reducere vægten med mellem 43 og 96 procent.
Konkret i DfAM-projektet har målet været at designe deltagernes komponenter eller produkter bedre eller anderledes, så de kan fremstilles med mindre materiale, større styrke, og optimeret med ny eller bedre funktionalitet og effektivitet. Alt sammen med det formål at skabe mere bæredygtige produkter og komponenter.
– I Dansk AM Hub har vi holdt øje med, hvordan DfAM som metode har fået fat i udlandets tunge industrier som fly-, bil- og våbenindustrien. Desværre har der været langt mellem de gode danske erfaringer, men det har vi nu lavet om på, siger direktør i Dansk AM Hub, Frank Rosengreen Lorenzen:
– For i dette forløb har vi gjort Design for Additive Manufacturing konkret for dansk produktion. Det er lykkes os at sammensætte de stærkeste internationale ekspertiser med vores danske eksperter, og skabe en proces, som for alvor har rykket dette område ud på de danske produktionsgulve, og nu har den danske industri konkrete erfaringer at lære fra.
Fordelene ved vægtreduktion har haft forskellige formål afhængig af virksomhedens specifikke produktion og slutprodukter. Eksempelvis har droneproducenten Airflight reduceret vægten på deres emne med 67 procent, hvilket gør dem i stand til enten at flyve længere eller med større last per flyvning. Og hos BEWI lykkedes det at reducere vægten med op imod 74 procent, hvilket betød en markant reduktion i materialeforbrug – og en reduktion i prisen på komponenten på 53 procent.
– Gennem projektet har vi opnået 11 kg vægtreduktion og reduceret materialemængden med 80 procent. Værdien for os er den ekstreme designfleksibilitet, hvor vi kan opnå større styrke til vægt-forhold, hvilket er en vigtig del i aviation, da det betyder, at vi kan flyve i længere tid eller med en tungere last, siger Mikkel Kærsgaard Sørensen, ejer og direktør i Airflight.
Og netop designfriheden fremhæves også af Ole Krebs, udviklingsmanager hos Plastvirksomheden BEWI:
– Ved at designoptimere med 3D print har vi først og fremmest reduceret vægten på produktet med 74 procent i forhold til traditionelt værktøj, men også forbedret vores time-to-market ved blandt andet at have skåret 25 procent af leveringstiden. Det giver en enorm fleksibilitet og er et potentiale, hvor vi ved at optimere værktøjet kan tilbyde mere komplekse og bedre løsninger på både kvalitet og økonomi og dermed møde de udfordringer, som vores maskinindstillinger ikke kan hjælpe os med. Desuden ser vi tegn på, at den optimerede komponent kan øge vores produktionskapacitet og sænke energiforbruget i produktionen, hvis vi implementerer den bredt – simpelthen fordi den er mere effektiv.
Efter forløbet har de tilmeldte virksomheder stået med en fysisk redesignet komponent eller produkt, hvor en eller flere af førnævnte fordele er tænkt ind. Ud over vægtreduktion har DfAM også givet en række andre fordele såsom reduktion af produktionsomkostninger, reduktion i ”time-to-market”, partkonsolidering, større designfrihed og forøgelse af komponentstyrke.
På den måde har deltagerne fået merværdi og viden, som kan forankres lokalt i deres produktion.
Om DfAM-forløbet
DfAM-projektet har haft til formål at udbrede kendskabet til 3D print og DfAM samt gøre danske virksomheder i stand til at udnytte de tekniske og forretningsmæssige muligheder, som AM-teknologien giver.
Traditionelt set er 3D print blevet brugt til fremstilling af prototyper, men teknologien rummer også en lang række andre muligheder. 3D-print kan med fordel også bruges til eksempelvis pilot- og småserieproduktion, og fremstilling af fiksturer og hjælpe-værktøjer, sprøjtestøbeværktøjer, og reservedele.
Fakta:
- DfAM innovationsforløbet sigter mod at styrke virksomhederne til i endnu højere grad at drage fordel af det teknologiske og forretningsmæssige potentiale inden for 3D print.
- Ud over en enkelt case med en vægtforøgelse blev komponentvægten reduceret med mellem 43 procent og 96 procent på de ti cases.
- Projektet er initieret af Dansk AM Hub i samarbejde med partnerne Teknologisk Institut, PLM Group, Hexagon og Wikifactory.
Mød virksomhederne fra DfAM-forløbet 2022:
BEWI fik lavere pris, kortere leveringstid og øget effektivitet med 3D printede designs
3D print-designforløb optimerer arbejdshandsker til superstyrke
3D print gav Newtecs kamerakomponent mere styrke og mindre vægt
Linatech: ”Designfriheden ved 3D print er genial”
3D printet design får drone til at flyve længere og løfte tungere
3D print-designforløb satte fart på udviklingshjulene hos CeramicSpeed
Med 3D print spiller violinen bedre og mere bæredygtigt
3D printede designs giver god genlyd hos Scan-Speak
BenBen håndbygger bedre cykler med 3D printede komponenter
Design med 3D print giver mere effektive vaskerobotter hos Washpower
Serman & Tipsmark optimerer nøgle til hydraulikudstyr: Sparer tid, materiale og penge
Med 3D print er der medvind på materialespild og klimaaftryk
Og find mange flere stærke cases i vores casearkiv.