BEWI reducerer værktøjs-vægt markant og opnår større fleksibilitet
I 3D print-designforløbet Design for Additive Manufacturing (DfAM) lykkedes flamingo-producenten BEWI med at reducere både vægt, pris og leveringstid på nogle af de værktøjer, der bruges i processen – og så ser de ud til at være mere effektive.
I videoen fortæller udviklingsmanager Ole Krebs fra BEWI om designforløbet og potentialet i 3D print-teknologien.
BEWI er en plastvirksomhed, som producerer polystyren – også kendt som flamingo – i kundetilpassede løsninger. I vores 3D print-designoptimeringsforløb DfAM kiggede virksomheden på at optimere et af værktøjerne, som indgår i støbeprocessen. Målet var at få en printet løsning, som kan bidrage med fleksibilitet – og det lykkedes. I forløbet optimerede BEWI designet på værktøjet og reducerede derved først og fremmest vægten med 74 procent i forhold til traditionelt værktøj, men også forbedrede time-to-market ved blandt andet at have skåret 25 procent af leveringstiden.
“Det giver en enorm fleksibilitet og er et potentiale, hvor vi ved at optimere værktøjet kan tilbyde mere komplekse og bedre løsninger på både kvalitet og økonomi og dermed møde de udfordringer, som vores maskinindstillinger ikke kan hjælpe os med. Desuden ser vi tegn på, at den optimerede komponent kan øge vores produktionskapacitet og sænke energiforbruget i produktionen, hvis vi implementerer den bredt – simpelthen fordi den er mere effektiv”, siger Development Manager i BEWI, Ole Krebs.
I det hele taget ser BEWI et stort potentiale i 3D print. I dag har virksomheden udfordringer i produktionen, som maskinindstillinger ikke kan hjælpe med – men ved at optimere værktøjet med 3D print opnår BEWI en større designfrihed, hvilket betyder, at man kan tilbyde en mere kompleks løsning.
Disse resultater har BEWI skabt ved hjælp af 3D print designoptimering:
- Enorm designfrihed og fleksibilitet
- 25 % kortere leveringstid
- 53 % prisreduktion i forhold til traditionelt værktøj
- 74 % vægtreduktion i forhold til traditionelt værktøj
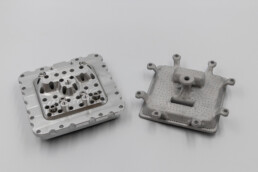
I løbet af 2022 har 15 danske virksomheder arbejdet med at redesigne et produkt eller komponent ved hjælp af 3D print gennem Dansk AM Hubs innovationsforløb: Design for Additive Manufacturing (DfAM). Ud af disse har 11 af virksomhederne haft en ’før-komponent’, som det har været muligt at sammenligne den redesignede komponent med, og i ti af disse tilfælde har det været muligt at reducere vægten med mellem 43 og 96 procent. Fordelene ved vægtreduktion har haft forskellige formål afhængig af virksomhedens specifikke produktion og slutprodukter.
Konkret i DfAM-projektet har målet været at designe deltagernes komponenter eller produkter bedre eller anderledes, så de kan fremstilles med mindre materiale, større styrke, og optimeret med ny eller bedre funktionalitet og effektivitet. Alt sammen med det formål at skabe mere bæredygtige produkter og komponenter.
Efter forløbet har de tilmeldte virksomheder stået med en fysisk redesignet komponent eller produkt, hvor en eller flere af førnævnte fordele er tænkt ind. Ud over vægtreduktion har DfAM også givet en række andre fordele såsom reduktion af produktionsomkostninger, reduktion i ”time-to-market”, partkonsolidering, større designfrihed og forøgelse af komponentstyrke.
På den måde har deltagerne fået merværdi og viden, som kan forankres lokalt i deres produktion.
Om DfAM-forløbet
- DfAM innovationsforløbet sigter mod at styrke virksomhederne til i endnu højere grad at drage fordel af det teknologiske og forretningsmæssige potentiale inden for 3D print.
- DfAM-projektet har haft til formål at udbrede kendskabet til 3D print og DfAM samt gøre danske virksomheder i stand til at udnytte de tekniske og forretningsmæssige muligheder, som AM-teknologien giver.
- Traditionelt set er 3D print blevet brugt til fremstilling af prototyper, men teknologien rummer også en lang række andre muligheder. 3D-print kan med fordel også bruges til eksempelvis pilot- og småserieproduktion, og fremstilling af fiksturer og hjælpe-værktøjer, sprøjtestøbeværktøjer, og reservedele.
- Ud over en enkelt case med en vægtforøgelse blev komponentvægten reduceret med mellem 43 procent og 96 procent på de ti cases.
- Projektet er initieret af Dansk AM Hub i samarbejde med partnerne Teknologisk Institut, PLM Group, Hexagon og Wikifactory.
Læs mere om forløbet her.
Har du spørgsmål eller interesse i at deltage i DfAM-forløbet?
Kontakt Dansk AM Hub på info@am-hub.dk
Related Posts
16/01/2025
Med 3D-print og bæredygtighed i fokus: KK Wind Solutions baner vejen for fremtidens vindmøller
KK Wind Solutions har udviklet en ny…
18/11/2024
PERFI Prints a Hearing Aid in Seconds – Could Transform the Entire Industry
The startup company won a pitch…
19/09/2024
Derfor er industriel 3D-print en gevinst for historisk byggeri
Matteo Baldassari fra virksomheden…
12/12/2023
Redesignet kølesystem laver varmt vand til fjernvarmen
Heatflow, som laver kølesystemer til…
12/06/2023
Kan man designe en væg med mindre materiale og samme bæreevne?
Apex Wall er et bemærkelsesværdigt…
20/03/2023
Prototal Damvig cases: Højere kvalitet, funktionalitet og reduceret time to market
Prototal Damvig har på det seneste…
17/03/2023
3DCP Group genopbygger ukrainsk børnehave med 3D print
I april tager 3DCP Group - en gruppe…
05/01/2023
Med AM-teknologi vil Wohn bygge billige og mere bæredygtige Tiny Houses
WOHN er en dansk startup med en vision…
04/01/2023
Dansk genanvendt metalpulver revolutionerer 3D metalprint industrien
Nordic Metals indsamler maskin- og…
13/12/2022
Lostboyslab demonstrerer potentialet ved AM i en cirkulær økonomi
Lostboyslab har skabt et maker lab,…
18/10/2022
3D print gav Newtecs kamerakomponent mere styrke og mindre vægt
Newtec laver optiske sorteringsmaskiner…
18/10/2022
3D print-designforløb optimerer arbejdshandsker til superstyrke
Gennem DfAM-forløbet halverede…
18/10/2022
Serman & Tipsmark optimerer nøgle til hydraulikudstyr: Sparer tid, materiale og penge
Serman & Tipsmark arbejder bl.a.…
18/10/2022
Med 3D print spiller violinen bedre og mere bæredygtigt
Larsen Strings producerer strenge til…
18/10/2022
3D print-designforløb satte fart på udviklingshjulene hos CeramicSpeed
CeramicSpeed er specialister i lejer…
18/10/2022
Design med 3D print giver mere effektive vaskerobotter hos Washpower
Virksomheden Washpowers har udviklet en…
18/10/2022
3D printet design får drone til at flyve længere og løfte tungere
Den danske startup Airflight testede…
13/10/2022
3D printede designs giver god genlyd hos Scan-Speak
Virksomheden Scan-Speak fik under et 3D…
15/02/2022
Dansk iværksætter opfinder 3D-printet ”køkkenmaskine” til fremstilling af cannabisolie
Ingeniør og iværksætter Peter Selmer…
27/12/2021
SEJMA Industries bekæmper klimaproblemer med 3D teknologi
SEJMA Industries har i 3DP Try Out…
20/12/2021
3D print løfter produktion, sikkerhed og service for DANILIFT
DANILIFT har deltaget i Dansk AM Hubs…
18/12/2021
Dansk teknologi skaber cirkulær produktion af indlægssåler
Create It REAL har udviklet teknologien…
15/12/2021
Fra uger til timer: 3D print optimerer SIK Tekniks produktudvikling
SIK Teknik har stort fokus på…
08/12/2021
ChromaViso sparer lysår på fremstilling af prototyper
I 3DP Try-Out forløbet lånte ChromaViso…
08/09/2021
Maskiningeniør og jazzmusiker udvikler 3D-printet elektrisk violin
Mød Laurent Bernadac - maskiningeniør…
18/03/2021
Med disruptiv teknologi forbedrer EYE-GO øjenpatienters vilkår
Ved at kombinere AM og sprøjtestøbning…
18/03/2021
Carmo A/S kombinerer AM og sprøjtestøbning og finder frem til en game changer
Kombinationen af AM og sprøjtestøbning…
19/01/2021
Terma reducerer materialeforbrug og produktionstid markant med AM
Hidtil har Terma A/S haft et højt…
30/04/2020
3D print sikrer hurtig produktion af værnemidler under corona-krisen
Hos AddiFab i Jyllinge fandt man, under…
02/03/2020
Med 3D print får vi langt mindre spild i designprocessen
Hos møbelvirksomheden NORR11 er det…
02/03/2020
Danitech: Langt om længe er vi nået til et stadie, hvor det giver mening at 3D printe i metal
For sønderjyske Danitech, der er…