3D print-designforløb optimerer arbejdshandsker til superstyrke
Virksomheden High Precisions Systems havde høje ambitioner med deres nyudviklede exoskelet handsker, da de gik ind til 3D print-designforløbet Design for Additive Manufacturing (DfAM). Alligevel blev virksomheden overrasket over, at teknologien i så høj grad formåede at forbedre de 3D printede titaniumhandsker ved at halvere tykkelsen og dermed øge både grebsstyrke og mindske slitage på fingerled.
De fleste kender filmene Ironman, hvor selveste jernmanden får superkræfter, når han ifører sig sin robotdragt. Referencen til Ironman er oplagt, når det kommer til den danske startup-virksomhed, High Procession Systems, der udvikler og laver exoskelet handsker – handsker, der er et nødvendigt og vigtigt redskab i industrien, hvor daglige og tunge løft kræver ekstra grebsstyrke.
“Helt konkret kan man tænke exoskelet handsker som en arbejdshandske, man tager på for at øge ens grebsstyrke markant fra håndleddet og gennem fingrene”, forklarer Niels K. B. Dahl, ejer af High Precisions Systems.
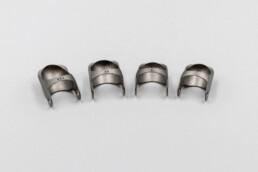
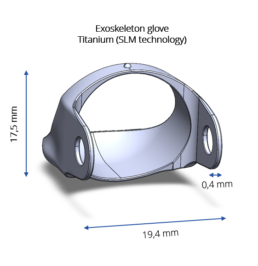
Fakta om løsningen:
- Materiale og teknologi: Titanium printet med Laser Powder Bed Fusion
- Godstykkelse: Reduceret fra 0,8 mm til 0,4 mm
- Vægtreduktion: 44 %
- Prisreduktion ved 3D print: 6 %
Lettere og stærkere end nuværende exoskelet handsker
Forud for DfAM-forløbet – et 3D print-designoptimeringsforløb – havde High Precisions Systems allerede udviklet en ny teknologi, hvor de lykkedes med at udvide anvendelsen af exoskelet handsken, så den også optager de kompressive kræfter.
“At vores handsker optager de kompressive kræfter, adskiller os særligt fra vores konkurrenter. Da graden af belastningen af et led under bevægelse er en af de store faktorer, der ligger til grund for udviklingen af slidgigt, kan vi – som de eneste os bekendt – ved at fjerne denne belastning være med til at sikre personalers fremtidige helbred”, lyder det fra Niels K.B. Dahl.
Deltagelsen i DfAM-forløbet resulterede i halvering af godstykkelse
Selvom High Precisions Systems exoskelet handske allerede havde et stort potentiale forud for DfAM-forløbet, gav deltagelsen flere væsentlige input til den videre udvikling. Særligt hvor langt det var muligt at presse grænserne for 3D print-teknologien i forhold til vægtykkelser på de printede komponenter.
“Deltagelsen i DfAM-forløbet var interessant for mig af flere årsager men særligt på grund af muligheden for at undersøge, hvor små godstykkelser det kunne lade sig gøre at producere. Godstykkelser er særlig interessante for os, da det er forskellen mellem at samle en kuglepen op med store tykke vinterhandsker eller tynde tilpassede kirurghandsker”, siger Niels K. B. Dahl:
“Dertil var det også vigtigt at producere test-emner. En ting er, at vi kan sidde og lave simuleringer på en computer, men en anden ting er, hvad der kan lade sig gøre at producere. Samtidig kan det i nogle tilfælde være svært at kvantificere et ‘feel’ af et objekt. Her er der ikke andet at gøre end at teste det i virkeligheden”.
Naturligt og tyndt fit – uden problemer
Interessen for at udfordre godstykkelsen på emnerne blev startskuddet til at sætte forløbet i gang – og det gav meget positive resultater og fornyet viden inden for 3D print.
“Fra starten havde vi lagt os fast på 0,8 millimeter i godstykkelse på de tyndeste steder på emnet. Men i forløbet undersøgte vi mulighederne og fik med stor succes godstykkelsen helt ned på 0,4 millimeter trods de komplekse geometrier. Med 3D print-teknologien gav det ingen problemer, selvom det er utrolig tyndt”, lyder det fra Niels K. B. Dahl.
Ud over at den halverede godstykkelse resulterer et mindre materialeforbrug, er den også lig et mere naturligt fit til handskens nuværende og kommende brugere.
”Man skal turde tage nogle chancer”
Niels K.B. Dahl peger særligt på én ting, som har haft stor værdi med virksomhedens deltagelse i DfAM-forløbet: Den nye opmærksomhed på 3D print-teknologiens muligheder og potentiale, som virksomheder kan få gavn af i deres udviklingsproces og konkurrencedygtighed.
“Inden DfAM-forløbet anvendte vi allerede 3D print, men jeg kendte ikke grænserne for metal 3D print, og det har været det primære at finde ud af: Altså at der er meget, der rent faktisk kan lade sig gøre”, siger Niels K. B. Dahl og uddyber vigtigheden i at turde tage chancer, når det kommer til de nye teknologier:
“Det, jeg vil sige til andre, der overvejer at deltage i et lignende forløb, er, at man skal turde tage nogle chancer og udnytte den teknologi, der er til rådighed, hvis man gerne vil forblive konkurrencedygtig – og her er 3D print en løsning, der ikke er til at komme uden om”.
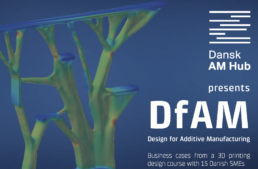
Kort om DfAM-forløbet
I løbet af 2022 har Dansk AM Hub i samarbejde med partnerne Teknologisk Institut, PLM Group, Hexagon og Wikifactory haft 15 danske SMV’er gennem et nyt innovationsforløb med henblik på at styrke virksomhederne til i endnu højere grad at drage fordel af det teknologiske og forretningsmæssige potentiale inden for 3D print. Forløbet kaldes Design for Additive Manufacturing (eller DfAM) og fokuserer på at udbrede 3D print til små- og mellemstore virksomheder samt at yde konkret støtte og hjælp til at arbejde med teknologien gennem design. Det konkrete mål for DfAM-forløbet er at re-designe deltagernes produkter eller komponenter, hvilket muliggør, at disse f.eks. kan fremstilles med større styrke, mindre materialespild, ny og bedre funktionalitet samt on-demand.
Læs mere om forløbet her.
Har du spørgsmål eller interesse i at deltage i DfAM-forløbet?
Kontakt Dansk AM Hub på info@am-hub.dk
Related Posts
16/01/2025
Med 3D-print og bæredygtighed i fokus: KK Wind Solutions baner vejen for fremtidens vindmøller
KK Wind Solutions har udviklet en ny…
18/11/2024
PERFI Prints a Hearing Aid in Seconds – Could Transform the Entire Industry
The startup company won a pitch…
19/09/2024
Derfor er industriel 3D-print en gevinst for historisk byggeri
Matteo Baldassari fra virksomheden…
12/12/2023
Redesignet kølesystem laver varmt vand til fjernvarmen
Heatflow, som laver kølesystemer til…
12/06/2023
Kan man designe en væg med mindre materiale og samme bæreevne?
Apex Wall er et bemærkelsesværdigt…
20/03/2023
Prototal Damvig cases: Højere kvalitet, funktionalitet og reduceret time to market
Prototal Damvig har på det seneste…
17/03/2023
3DCP Group genopbygger ukrainsk børnehave med 3D print
I april tager 3DCP Group - en gruppe…
18/10/2022
BEWI reducerer værktøjets vægt markant og opnår større fleksibilitet
I forløbet Design for Additive…
18/10/2022
3D print gav Newtecs kamerakomponent mere styrke og mindre vægt
Newtec laver optiske sorteringsmaskiner…
18/10/2022
Serman & Tipsmark optimerer nøgle til hydraulikudstyr: Sparer tid, materiale og penge
Serman & Tipsmark arbejder bl.a.…
18/10/2022
Med 3D print spiller violinen bedre og mere bæredygtigt
Larsen Strings producerer strenge til…
18/10/2022
3D print-designforløb satte fart på udviklingshjulene hos CeramicSpeed
CeramicSpeed er specialister i lejer…
18/10/2022
Design med 3D print giver mere effektive vaskerobotter hos Washpower
Virksomheden Washpowers har udviklet en…
18/10/2022
3D printet design får drone til at flyve længere og løfte tungere
Den danske startup Airflight testede…
13/10/2022
3D printede designs giver god genlyd hos Scan-Speak
Virksomheden Scan-Speak fik under et 3D…
15/02/2022
Dansk iværksætter opfinder 3D-printet ”køkkenmaskine” til fremstilling af cannabisolie
Ingeniør og iværksætter Peter Selmer…
27/12/2021
SEJMA Industries bekæmper klimaproblemer med 3D teknologi
SEJMA Industries har i 3DP Try Out…
20/12/2021
3D print løfter produktion, sikkerhed og service for DANILIFT
DANILIFT har deltaget i Dansk AM Hubs…
18/12/2021
Dansk teknologi skaber cirkulær produktion af indlægssåler
Create It REAL har udviklet teknologien…
15/12/2021
Fra uger til timer: 3D print optimerer SIK Tekniks produktudvikling
SIK Teknik har stort fokus på…
08/12/2021
ChromaViso sparer lysår på fremstilling af prototyper
I 3DP Try-Out forløbet lånte ChromaViso…
08/09/2021
Maskiningeniør og jazzmusiker udvikler 3D-printet elektrisk violin
Mød Laurent Bernadac - maskiningeniør…
18/03/2021
Med disruptiv teknologi forbedrer EYE-GO øjenpatienters vilkår
Ved at kombinere AM og sprøjtestøbning…
18/03/2021
Carmo A/S kombinerer AM og sprøjtestøbning og finder frem til en game changer
Kombinationen af AM og sprøjtestøbning…
30/04/2020
3D print sikrer hurtig produktion af værnemidler under corona-krisen
Hos AddiFab i Jyllinge fandt man, under…
02/03/2020
Med 3D print får vi langt mindre spild i designprocessen
Hos møbelvirksomheden NORR11 er det…
02/03/2020
Danitech: Langt om længe er vi nået til et stadie, hvor det giver mening at 3D printe i metal
For sønderjyske Danitech, der er…