Fast Track via 3D-printede sprøjtestøbeforme
Når danske virksomheder står over for at skulle lancere et nyt produkt, der skal fremstilles via plaststøbning, står de over for et forløb, der dækker over en
1) produktudviklingsfase, og
2) produktlancering.
Den første fase er ofte en stor investering, og det er også en risikoladet post, hvilket gør, at der er en hurdle i forhold til at forfølge produktidéer. Selv den bedste planlægning og et budget lagt efter de bedst tilgængelige informationer og vurderinger kan vise sig at ikke holde stik.
Udviklingsfasen består normalt af et forløb, hvor der bliver fremstillet et antal prototyper som testes af. Traditionelt skal man til dette fremstille et støbeværktøj, hvilket hurtigt kan koste 50.000 kr. og opefter og forbruge mindst 10 uger.
Tilmed, hvis det støbte emne viser sig at skulle ændres, skal man højst sandsynligt indkøbe et nyt værktøj med yderligere ventetid. Muligheden for at teste idéer af ud over det helt strengt fastlagte (er derfor ringe.
Additive Manufacturing har betydet en lettelse i produktudviklingsfasen. Prototyper kan fremstilles meget hurtigt i en række materialer, særligt ABS, PLA og Nylon.
For mange virksomheder er dette dog ikke nok. Fordi
1) prototyperne ønskes i det rigtige materiale, og
2) de skal sprøjtestøbes
Så opfører de sig som det færdige produkt i forhold til alle de produktegenskaber der er ønskelige. Det være sig udseende, styrke, elasticitet m.m.
3D PIM
For at afhjælpe dette er sprøjtestøbning ved brug af 3D-printede forme (3DPIM) kommet på banen. Emnerne bliver sprøjtestøbt i det rigtige materiale, og formene kan produceres hurtigt og billigt. Typisk vil man kunne fremstille et par hundrede emner pr. form, inden den nedbrydes.
3DPIM har indtil nu fået nogen udbredelse i verden. Den store 3D-print-producent Stratasys har fx en forretning inden for 3DPIM. Deres erfaring er, at der spares 50-90% af tid og 50-70% af pris i udviklingsfasen. En støbeform leveres på op til 4 uger. Dette er en væsentlig forbedring. I Danmark har man set nogen brug af 3DPIM, men mest på småprojekt-stadiet, med udvikling på DTU for en stor dansk produktionsvirksomhed samt på Teknologisk Institut. Området er stadig ret nyt og ukendt for virksomhederne.
FREEFORM INJECTION MOLDING (FIM)
Som noget nyt inden for 3DPIM er det blevet muligt at producere forme endnu hurtigere og friere ved Freeform Injection Molding (FIM). Her opløses formene efter størkning af emnerne, hvorved emnerne frigøres. Herved behøver produktdesignerne ikke tænke i skillelinjer, hvilket kan betyde en væsentlig fordyrelse af støbeværktøjet og være en showstopper. Med andre ord fjerner 3DPIM-FIM hindringer mellem produktdesigneren og den sprøjtestøbeansvarlige. Det styrker flowet fra idé til fremstillet produkt.
I 3DPIM er opstarten langt hurtigere end blot plaststøbning. Ved split-molds er emnefremstillingen lige så hurtig som normal plaststøbning – ved FIM skal formene printes pr. emne, men selve støbningen er næsten lige så hurtig som for split-molds.
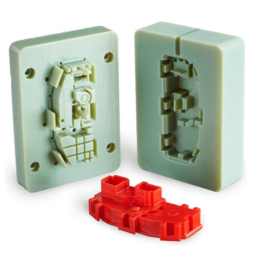
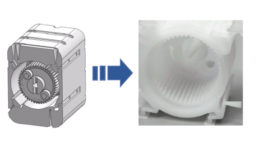

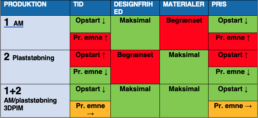
Related Posts
10/07/2025
Dansk AM Hub udvider med nyt teknologilaboratorium i Frederikssund
Danmark har fået en ny platform for…
19/06/2025
Print og byg: Kan 3D-print i stor skala blive et nyt værktøj for byggebranchen?
Mindre materialeforbrug, lavere CO2…
17/06/2025
AM Summit vender tilbage i 2025 i nyt format med fokus på små og mellemstore virksomheder
Efter et succesfuldt AM Summit 2024…
05/03/2025
3DCP sætter betonprint på skoleskemaet sammen med Herningsholm Erhvervsskole
I et undervisningsforløb mellem 3DCP…
16/01/2025
Med 3D-print og bæredygtighed i fokus: KK Wind Solutions baner vejen for fremtidens vindmøller
KK Wind Solutions har udviklet en ny…
18/11/2024
PERFI Prints a Hearing Aid in Seconds – Could Transform the Entire Industry
The startup company won a pitch…
30/10/2024
AM Summit skabte et kreativt rum mellem udstillere og deltagere
Paneldebat om verdens hurtigste cykel…
19/09/2024
Derfor er industriel 3D-print en gevinst for historisk byggeri
Matteo Baldassari fra virksomheden…
19/08/2024
Space Challenge: Design the Future of Space Exploration
Dreaming of space? Now’s your chance to…
12/12/2023
Redesignet kølesystem laver varmt vand til fjernvarmen
Heatflow, som laver kølesystemer til…
29/09/2023
Danmarks første additive manufacturing (3dprint) pris uddeles til spirende startup, der har printet en børnehave i Ukraine
Verdens største AM-messe Formnext har…
27/06/2023
Danmark udnævnes til kernepartner for verdens største 3D print messe
Verdens største AM-messe Formnext har…
13/06/2023
AM Summit 2023: Presenting this year’s strong programme
40+ speakers. 45+ exhibitors. 450+…
12/06/2023
Kan man designe en væg med mindre materiale og samme bæreevne?
Apex Wall er et bemærkelsesværdigt…
12/06/2023
Helt grøn på klimakommunikation? Sådan undgår du faldgruberne
Vil du undgå greenwashing? Så har…
09/06/2023
Er Additive Manufacturing løsningen på vores forsynings- sikkerheds- og klimakrise?
Direktør Frank Rosengreen Lorenzens…
30/05/2023
Nyt projekt: 3D print skal kunne følge med sprøjtestøbning
AM Farm: Nyt projekt vil sikre, at en…
03/05/2023
Dansk AM Hub mødte tusindvis af nysgerrige på årets VTM
I april var Dansk AM Hub blandt de 116…
28/04/2023
Wohlers Rapport 2023 afslører fortsat tocifret vækst i AM industrien
Wohlers Associates, drevet af ASTM…
20/04/2023
Mød os på VTM Summit og bliv klogere på 3D print i metalindustrien
Mød os på VTM Summit 2023 fra 25.-28.…
14/04/2023
Se billeder fra vores AM Talenters besøg hos The LEGO Group
Sammen med 20 talenter fra vores AM…
30/03/2023
Lær om AM teknologiens fulde potentiale på nyt dansk masterfag
Fra foråret 2023 udbydes faget Value…
24/03/2023
6. kl. skifter klasseværelset ud med et besøg i Damvigs 3D print-produktion
I marts var 18 elever fra 6. klasse på…
24/03/2023
Vær med til at accelerere den cirkulære omstilling på LOOP Forum
Nordens førende event om cirkulær…
22/03/2023
Debat: Lad fremtidens teknologi genopbygge Ukraine
AM rummer et stort potentiale både ift.…
20/03/2023
Prototal Damvig cases: Højere kvalitet, funktionalitet og reduceret time to market
Prototal Damvig har på det seneste…
21/02/2023
Join other AM Talents for a behind-the-scenes visit to the LEGO Group’s AM Facilities
Join other AM Talents for a…
07/02/2023
AM Magazine 2023: Additive Manufacturing & fire konkrete trin til en grønnere produktion
I AM Magazine 2023 får du fire konkrete…
07/02/2023
New report: Sustainable Manufacturing of the Future: The Role of Additive Manufacturing
This report gathers our approach to…
30/01/2023
Chatbot leverer lynhurtigt SWOT-analyse af 3D print-teknologiens potentiale for at skabe mere bæredygtig produktion
Dansk AM Hub er hoppet med på trenden…
16/01/2023
Ny Roland Berger-rapport: Hvor bæredygtigt er AM egentlig?
En ny Roland Berger rapport tager et…
12/01/2023
Nyt industrifællesskab hjælper danske virksomheder med at 3D printe i metal
Nu går en lang række aktører sammen i…
12/01/2023
Danish AM Hub launches Report on Additive Manufacturing in Crisis Response
Danish AM Hub, in cooperation with…
05/01/2023
Med AM-teknologi vil Wohn bygge billige og mere bæredygtige Tiny Houses
WOHN er en dansk startup med en vision…
04/01/2023
Dansk genanvendt metalpulver revolutionerer 3D metalprint industrien
Nordic Metals indsamler maskin- og…
13/12/2022
Lostboyslab demonstrerer potentialet ved AM i en cirkulær økonomi
Lostboyslab har skabt et maker lab,…
12/12/2022
AM Power Insights: Sustainability of Metal Additive Manufacturing
I en ny rapport kortlægger AM Power det…
07/12/2022
Dansk AM Hub lancerer karriereplatform for nye AM-talenter
I det nye år vil Dansk AM Hub lancere…
01/12/2022
Dansk AM Hub kursus: Hvordan kan vi skabe værdi gennem Additive Manufacturing?
Dansk AM Hub udbyder et nyt kursus, der…
01/12/2022
Nyt masterkursus uddanner virksomheder i at udnytte 3D print-teknologien
Dansk AM Hub har i samarbejde med SDU…
16/11/2022
Webinar: Bliv klogere på potentialerne ved additive manufacturing
Se dette webinar, der kan gøre dig…
12/10/2022
AM Summit 2022: See pictures from this year’s exhibitors
AM Summit 2022: See pictures from this…
11/10/2022
3D printede designs sætter virksomheders produkter på slankekur
I DfAM-forløbet har 10 ud af 11…
05/10/2022
Hver anden virksomhed fortsætter med AM-teknologien efter 3D print-hybrid-forløb
Når først virksomheder har oplevet de…
05/10/2022
Mød os på Digital Tech Summit – og få 40 % rabat på din billet
Dansk AM Hub taler på Digital Tech…
04/10/2022
Maker-program inspirerer virksomheder til optimerede design- og produktionsmetoder
I 2022 har Dansk AM Hub for første gang…
04/10/2022
AM Summit 2022 breakout session: Learn from Danish AM Experts
Read more from AM Summit 2022 breakout…
04/10/2022
AM Summit 2022 breakout session: Meet the Women in 3D Printing
Read more from Women in 3D Printing -…
27/09/2022
AM Summit 2022 breakout session: Sustainable Materials
Read more from Sustainable Materials -…
14/09/2022
AM Summit 2022 breakout session: 3D Printing Sustainable Cities
Read more from 3D Printing Sustainable…
14/09/2022
AM Summit 2022 breakout session: Changing Paradigms
Read more from Changing Paradigms - one…
13/09/2022
More people than ever gather for sustainable 3D print conference
AM Summit 2022 marked another…
13/09/2022
Flere end nogensinde samles til grøn 3D print konference
AM Summit 2022 slog igen i år rekord…
05/09/2022
3D print konference nytegner byggeri med den bæredygtige blyant
Additive manufacturing (AM) og 3D…
18/08/2022
Seminar gør dig klogere på avanceret og bæredygtig produktion
Udenrigsministeriet afholder i…
18/08/2022
Konference kalder kvinderne til 3D print-produktionsgulvene
Der er ikke mange kvinder repræsenteret…
18/08/2022
3D print konference: Materialer gør afgørende forskel for bæredygtig produktion
Vi skal have vores samlede…
04/08/2022
Live fra AM Summit 2022: Guns N’ Roses rocker på en 3D printet guitar
AM Summit 2022 inviterer til koncert…
13/07/2022
Deltag i Design for Additive Manufacturing (DfAM) – afslutningsevent
Bliv introduceret til DfAM-projektet og…
29/06/2022
Studerende og virksomheder står allerede i kø til ny 3D print-uddannelse
Efter sommerferien begynder det første…
16/06/2022
3D print-konference udfordrer, hvordan et produkt designes, udvikles og produceres
AM Summit 2022 sætter fokus på, hvordan…
14/06/2022
Grøn Tech-tillæg: Sådan kan 3D print hjælpe dansk produktion i den grønne førertrøje
I Grøn Tech-tillægget i Berlingske og…
13/06/2022
Dansk AM Hub taler bæredygtig dansk produktion på AMGTA Summit
Med indførelse af en ny dansk…
30/05/2022
Stor fremgang i 3D print rykker konference til større lokaler
AM og 3D print har haft vokseværk de…
25/05/2022
Produktionsvirksomheder printer sig til bedre produkter – kom og hør hvordan
Vær med når Industriens Fond byder på…
12/05/2022
Prototal Damvig indfører ny 3D print teknologi til Danmark
Som de første i Danmark - og med den…
11/05/2022
WEF Rapport sammenligner 13 AM Hubs globalt: Fremhæver dansk bæredygtigt fokus
Læs den nyeste rapport om Global…
29/04/2022
McKinsey: Industrien for medicinsk udstyr har stor succes med AM teknologien
Industrien for medicinsk udstyr har i…
13/04/2022
LOOP: Her er løsningen på stigende mængder affald og øget ressourceforbrug
LOOP bringer viden, erfaringer,…
06/04/2022
Nye indsatser kan afhjælpe mangel på kvalificeret arbejdskraft
Flere små og mellemstore danske…
29/03/2022
Wohlers rapport 2022 viser stærk vækst i AM-industrien
Wohlers Report is an industry-leading…
28/03/2022
Portræt: Steffen skal inspirere dig til at printe i metal
Læs et portræt af Dansk AM Hubs CTO…
25/03/2022
More and more Danish manufacturing companies use AM technology
In 2021, more than ever Danish…
10/03/2022
Danskere 3D printer årepresser til sårede i Ukraine
Det danske 3D print-miljø samles nu om…
09/03/2022
Danske virksomheder skal designe bedre produkter med 3D teknologi
DfAM er vores nye innovationsforløb,…
02/03/2022
A Guidebook for the Adoption of Additive Manufacturing in Operations
A new guidebook aims to provide…
04/02/2022
Danske virksomheder griber gratis mulighed for at prøve 3D print
Flere danske virksomheder har i 2021…
13/12/2021
Investorer og iværksættere viste endnu en gang AMs store potentiale
AM Venture Day handler om at bringe…
01/12/2021
Venture Day 2021: Dansk AM Hub matcher iværksættere og investorer
AM Venture Day handler om at bringe…
18/11/2021
Vinderne af den landsdækkende 3D-print-konkurrence er nu fundet
Simon og Emil fra Herningsholm…
28/10/2021
Dansk AM-teknologi printer huse i Afrika mere bæredygtigt
Danske COBOD International har nu 3D…
19/10/2021
Debat: Forsyningskrisen skal få os til at gentænke produktionssystemet
Forsyningskrisen afslører behovet for…
18/09/2021
Watch – or rewatch! – all of the presentations from AM Summit 2021
The presentations from AM Summit 2021…
17/09/2021
Webinar: Analyse viser, at Additive Manufacturing sparer penge, tid og CO2
LCA rapporten udearbejdet efter vores…
15/09/2021
Wikifactory og Dansk AM Hub: Danmark skal være midtpunkt for bæredygtig produktion
Danmarks AM-miljø er blandt årsagerne…
27/08/2021
Vil du deltage i et forløb om prøvelse af 3D printede fiksturer?
I efteråret 2021 tilbydes fem…
25/08/2021
Nordiske virksomheder vil (be)vise vejen i den grønne omstilling via Additive Manufacturing
Med en række partnere vil Dansk AM Hub…
25/05/2021
Sådan skaber vi dansk bæredygtighed gennem Additive Manufacturing
Direktør i Dansk AM Hub, Frank…
19/05/2021
40 millioner skal styrke dansk bæredygtig produktion
Industriens Fond geninvesterer i Dansk…
07/05/2021
Protected: Dansk AM Hub indgår samarbejde med 3D Eksperten
Dansk AM Hub indgår samarbejde med 3D…
18/03/2021
Endnu et vellykket Hybrid-forløb: Virksomheder forbedrer produkter, mens de sparer penge, tid og bliver mere bæredygtige
Læs her om fem virksomheder, som…
17/03/2021
Ny rapport viser global vækst for 3D print trods pandemi
Wohlers report giver en status på AM…
15/03/2021
AM udgør et stærkt våben i America Makes’ kamp mod COVID19 – og fremtidige kriser
Læs om hvordan America Makes spillede…
12/03/2021
Webinar-optagelse: AM – Leading the Rebound of American Manufacturing
How do we use Additive Manufacturing…
23/02/2021
Webinar: AM – Leading the Rebound of American Manufacturing
I dette webinar hører vi amerikanske…
11/02/2021
Webinar: Genanvendt plast og 3D print – effektiv grøn omstilling
Genanvendt plast og 3D print er temaet…
10/02/2021
Norden samles for at styrke et fælles fokus på 3D print
Sammen med Alfred Nobel Science Park,…
03/02/2021
Wikifactory is moving its global headquarters from Hong Kong to Denmark
Wikifactory is moving its global…
01/02/2021
Dansk AM Rapport 2021: Potentiale til en bæredygtig fremtid
Dansk AM Rapport 2021 - bliv klogere på…
12/01/2021
Dit juridiske ansvar i markedsføringen af 3D-teknologiens bæredygtige potentiale
Accura advokater har endnu engang…
08/12/2020
Nyt europæisk projekt etablerer produktionsberedskab til fremtidige sundhedskriser
Nyt fælleseuropæisk projekt skal sikre…
24/11/2020
Accuras juridiske anbefalinger til dig, der bruger 3D print
Accura advokater har samlet en række…
22/10/2020
Additive Manufacturer Green Trade Association Announces New Members
Danish AM Hub becomes part of a global…
28/08/2020
Vær bevidst om dit juridske ansvar ved brug af 3D print
Accura advokater har samlet en række…
04/06/2020
The Impact of COVID-19 on the Future of Advanced Manufacturing and Production
Insights from the World Economic…
26/05/2020
Terma reducerer materialeforbrug og produktionstid markant med AM
Hidtil har Terma A/S haft et højt…
15/04/2020
Hybrid: 3D print og sprøjtestøbning skaber adapter til snorkelmaske
I kampen mod Corona har AddiFab med…
07/01/2020
Svenske Prototal AB køber den danske 3D-print virksomhed Damvig A/S
Damvig A/S har indtil salget været ejet…
05/12/2019
Danish AM Hub as winner of German Design Award 2020
In the fall of 2019, Danish AM Hub won…
24/09/2019
3D Print kommer til at revolutionere implantat-markedet
Particle3D har med sloganet "We print…
12/06/2019
Dansk AM Hub vil hente udenlandsk kapital til danske start-up virksomheder inden for 3D print
Et nyt initiativ fra Dansk AM Hub skal…
14/01/2019
40 AM eksperter giver deres bud på udviklingen i 2019
Michael Petch fra medievirksomheden 3D…
08/01/2019
The potential in Additive Manufacturing
07/12/2018
Additive Manufacturing er drivkraften for bilindustriens fremtid
Forbes artikel skrevet af Sarah Goehrke…
27/11/2018
Addifab fordobler omsætningen det første år med 3D print og sprøjtestøbning
Sidste år vandt AddiFab i Jyllinge…
10/09/2018
Dansk AM Hub er dansk anker på nordisk samarbejde om 3D print
Det er første gang der samles et…
07/06/2018
Danske virksomheders konkurrenceevne skal styrkes med 3D print
3D print og Additive Manufacturing er…
06/06/2018
Monoqool var halvvejs i skifteretten – en 3D-printer forhindrede likvidering og grundlagde en millionforretning
Danske virksomheder kan lære meget af…
06/06/2018
Danske virksomheder sakker bagud i milliardstort 3D-kapløb
Med 46 mio. kr. i ryggen skal Dansk AM…
21/03/2018
Siemens investerer stort i 3D print
30/01/2018
Regeringens nye digitale vækstinitiativ vil skabe synergi med AM Hub
I forlængelse af mødet i…
23/01/2018
Huismans 3D printede kran-krog testet til bæreevne på 80.000 kg
Huisman, en verdensomspændende…
22/01/2018
Harvard forskningsprojekt udvikler roterende 3D print metode, der producerer som naturen gør det
Kompositmaterialer, der findes…